Festo Контроллер позиционирования CPX-CMAX User Manual
Page 87
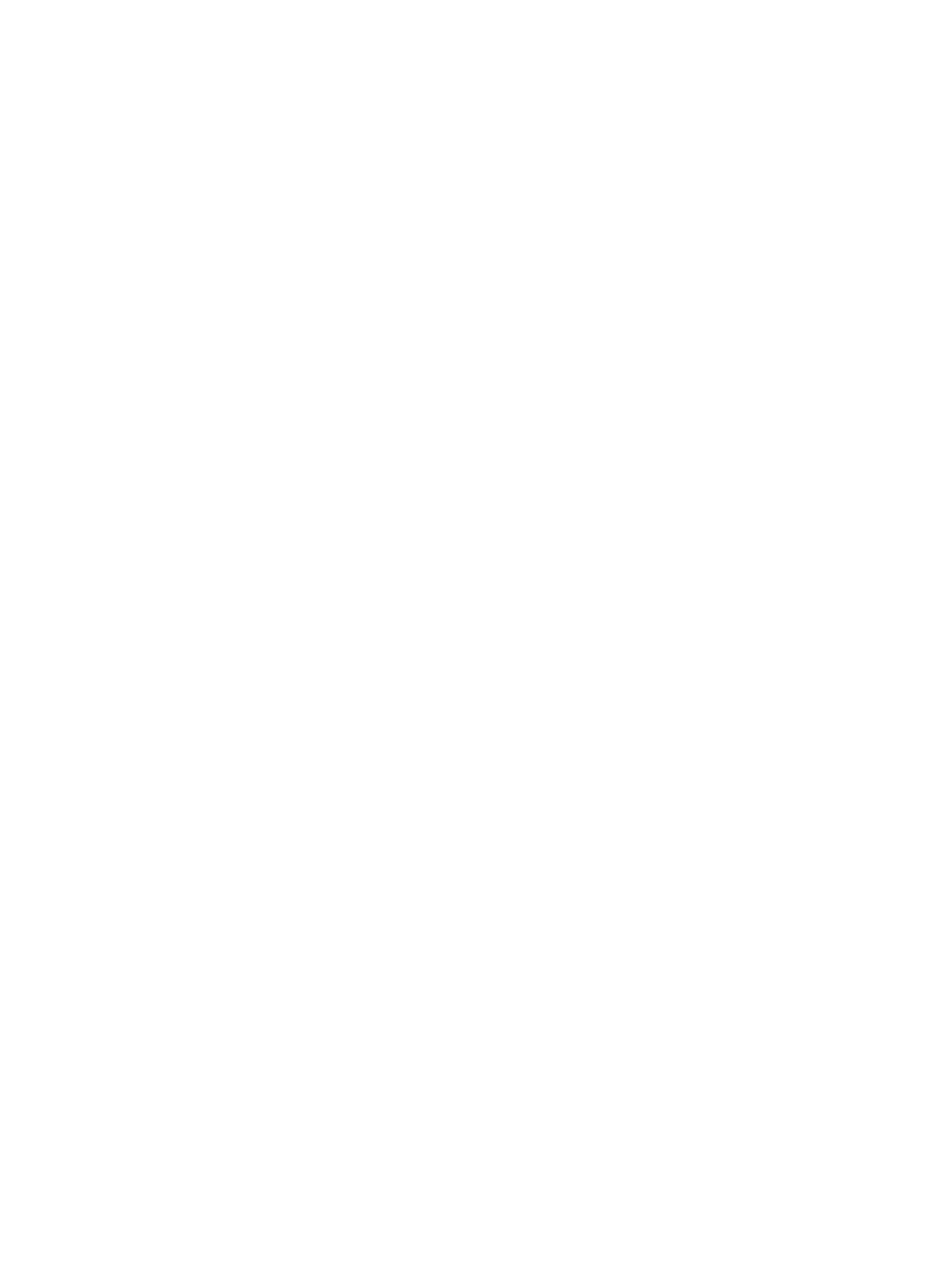
4. Commissioning
4−9
Festo P.BE−CPX−CMA X−SYS−EN en 0908NH
Delivery status
(first switch−on or after data reset)
ć
The connected components (valve and displacement enĆ
coder/sensor interface) are automatically looked for at
the axis interface. The contained information is read out.
ć
The recognised components are
not automatically acĆ
cepted as the target state.
ć
The controller cannot be activated until the axis data is
completely parameterised
1)
. Actual values are then not
updated.
1)
The target configuration (of the mechanics data) must
have been compared with the actual configuration.
Normal start−up
ć
The connected components (valve and displacement enĆ
coder/sensor interface) are automatically looked for at
the axis interface. The contained information is read out.
ć
The found actual configuration is compared with the
target configuration. If there is a deviation, this leads to
an error and the controller is not activated.
This error can only be acknowledged after comparing the
target and actual configurations.
Recognisable parameters
The CMAX automatically acquires all parameter values
which are stored in the drive, sensor (displacement encoder)
or valve. The FCT plug−in can read these values out of the
CMAX. They do not have to be entered in the FCT project.
The acquired data cannot be overwritten.