Lincoln Electric IM8002 POWER WAVE MANAGER User Manual
Page 96
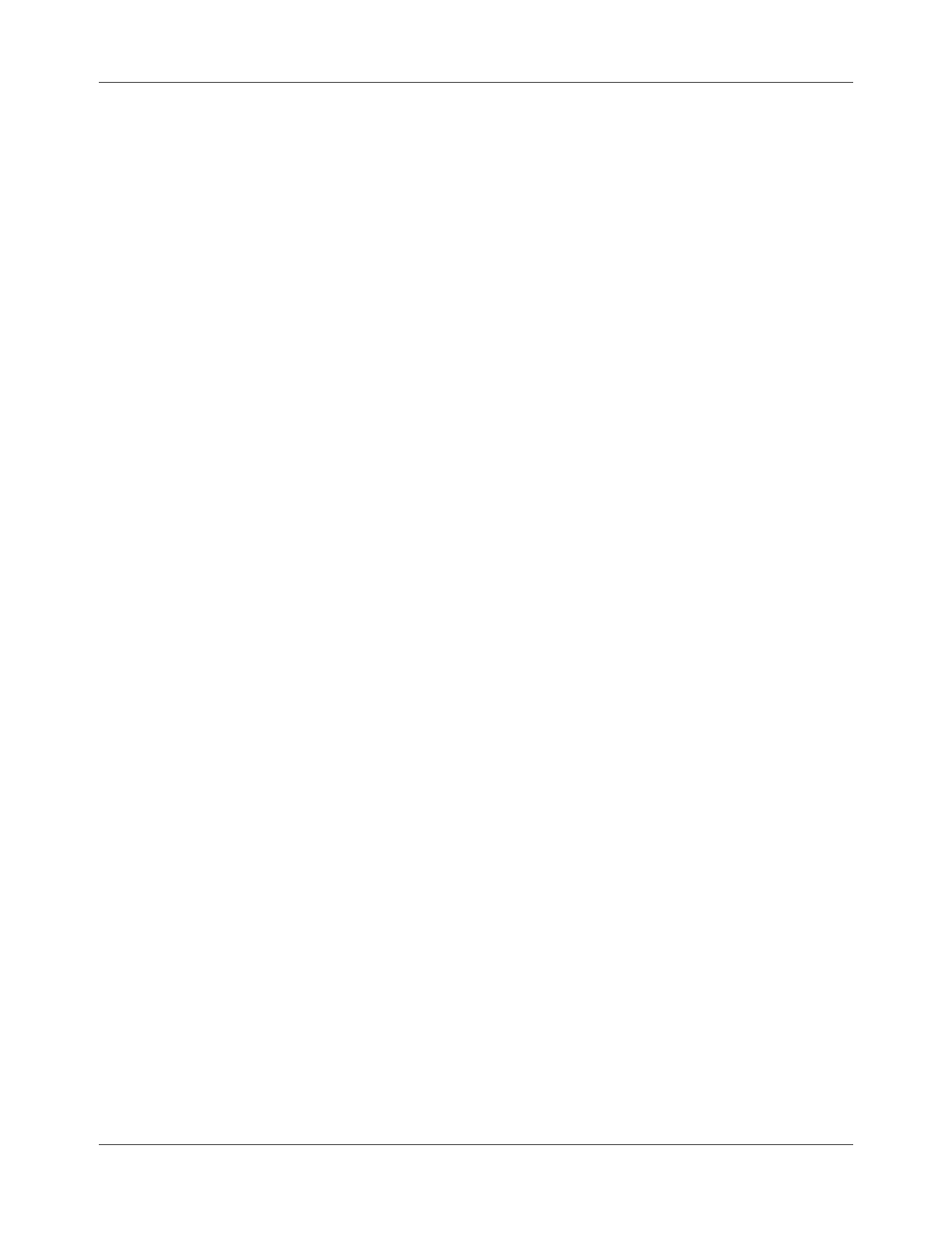
Chapter 11. Training
WeldScore™
11.2
Power Wave® Manager User Manual
IM8002
addition to traditional current and voltage measurements, WeldScore™ also looks at 30 to 40 additional
variables that help to make it more reliable and accurate than traditional weld monitoring systems.
Consistency and repeatability are the keys to make your use of WeldScore™ effective. In order to assign a
score, the Welding Power Source must first be taught what is considered to be an acceptable weld. This is
done through the training section of Power Wave® Manager. When a score is assigned to a future weld, it
is done by comparing it to the taught weld. Therefore, it is necessary to teach the Welding Power Source
every weld for which a WeldScore™ is desired. Some examples of when new training is required include
changes in wire feed speed, voltage, joint type or position.
WeldScore™ is able to accommodate both welds with very tight tolerances and welds that have some
acceptable process variation. If the welds taught to the Welding Power Source all have very little variation,
then the only welds that will receive a passing WeldScore™ are ones that meet that very tight tolerance.
Likewise, if there is room for some variation (e.g., small changes in electrical stickout) and the acceptable
variations are used in the training process, then WeldScore™ will assign passing scores to welds that fall
within those variations.
Where to Use WeldScore™
WeldScore™, like any statistical analysis method or technique, requires a controlled process. WeldScore™
works best with a consistent and repeatable process. It will produce the most accurate results with single-
pass welds or welds with a small number of passes because, as more passes are used, the process
inherently becomes less repeatable. If there are a large number of variables that are allowed, a significant
amount of variation, the criteria may be too broad for the WeldScore™ to be a meaningful value.
Meaning of the WeldScore™ Value
An instantaneous WeldScore™ value is calculated every 0.25 seconds. The average of these scores over the
entire weld is reported as an overall score displayed on the User Interface, in Production Monitoring™ or in
CheckPoint™.
Keep in mind that this overall WeldScore™ is an average over the entire weld. A weld could still have a high
WeldScore™ even if there is a problem for a short portion of the weld time. For example, if a 50-inch weld
has a score of 95% for 49 inches, but a score of 45% for the last inch, the overall score will be a 94%.
However, that last inch is actually problematic and not acceptable.
The Out-of-Limit features in Power Wave® Manager alert you when the WeldScore™ goes below the
minimum you set for a defined moving window of time. This helps ensure the integrity of the overall
WeldScore™. See pages 10.5 and 10.7 for more details on these features.