Fanuc robots, Appendix b fanuc robots, Fanuc systems and ip addresses – Lincoln Electric IM8002 POWER WAVE MANAGER User Manual
Page 107
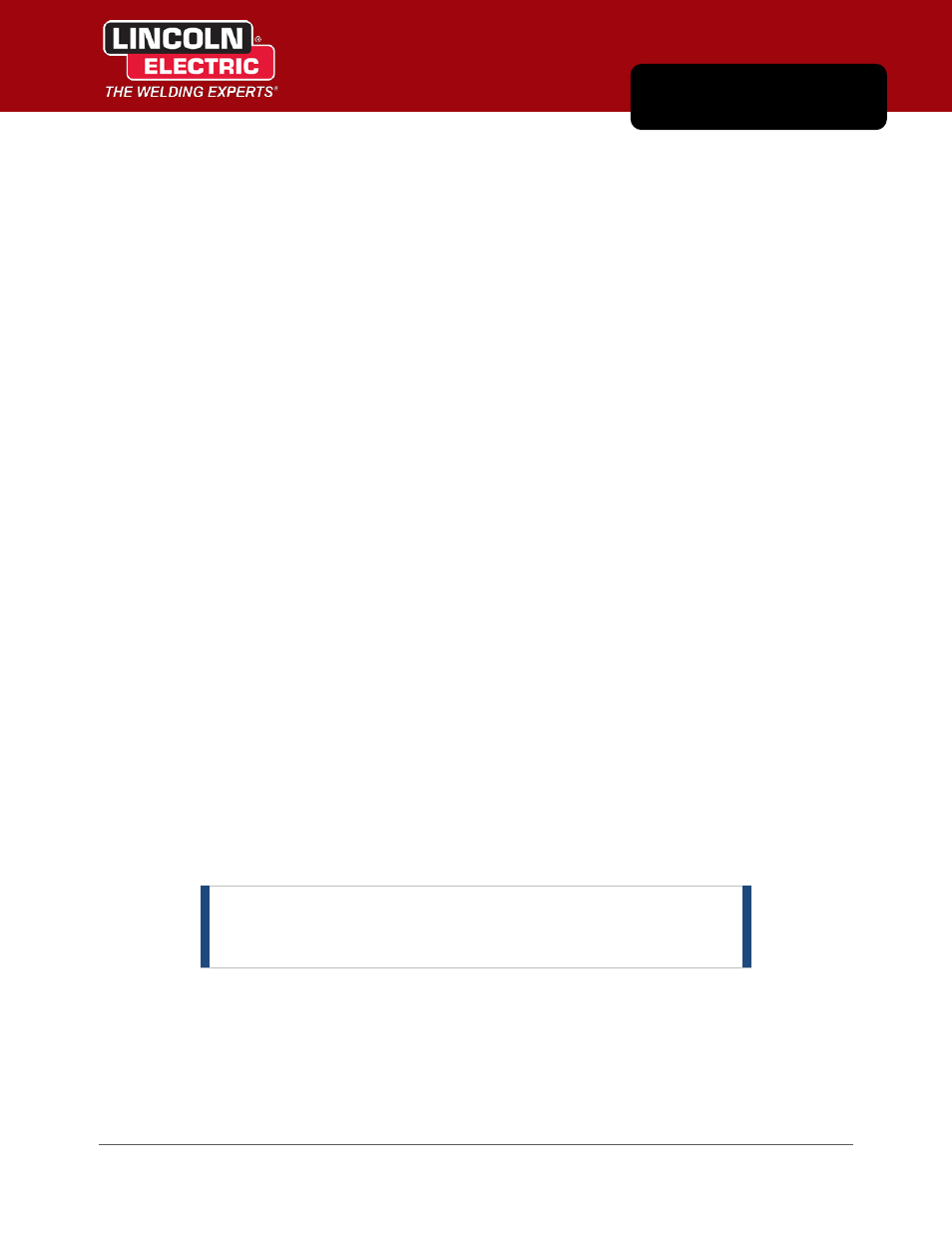
IM8002
Power Wave® Manager User Manual
B.1
Appendix B
FANUC Robots
FANUC Systems and IP Addresses
When connecting to Welding Power Sources that provide welding power for FANUC robot controllers it is
important to understand the connection path between the computer running Power Wave® Manager and
the Power Wave® power source.
The FANUC robot controller acts as a proxy server for messages between Power Wave® Manager and the
connected Power Wave® Welding Power Source. FANUC R-30iA and R-30iB robot controllers include two
Ethernet ports:
Port 1 is normally connected to a building network.
Port 2 is connected to the local Power Wave® Welding Power Source.
When you connect Power Wave® Manager to the Power Wave® power source, the most convenient way to
do this is to connect the computer running Power Wave® Manager to the same network as Port 1 of the
robot controller.
When you start Power Wave® Manager, choose the I know the address of the welder option on the
Connection tab and enter the IP address assigned to Port 1 of the robot controller. The proxy server will
pass messages to the Power Wave® Welding Power Source.
For more detailed information, please refer to the ArcTool Setup and Operations manual for your FANUC
robot.
FANUC® Robot Application (Prior to v7.70P/21)
Production Monitoring™/CheckPoint™ is a tool within the Welding Power Source that sends weld process
data to a remote computer for monitoring. You can also use it to alert the robot operator if a weld process
has exceeded predetermined limits. You can monitor the following limits: WeldScore™, current, voltage,
wire feed speed and time. If the robot exceeds the limits set for the weld, an alarm can be generated at the
robot to alert the operator.
Production Monitoring™/CheckPoint™ uses programs already loaded into the robot to monitor and to
check if the weld is within the limits set in the Weld Profile. These programs will then generate an alarm or
other desired action to alert the robot operator.
NOTE |
Production Monitoring™/CheckPoint™ determines if a weld
is within specified limits. It does not determine if the weld
is good or bad.
Page B.8 discusses support for Production Monitoring™/CheckPoint™ in a FANUC robot starting with the
v7.70P/21 release.