Training, Before you begin training a weld weldscore, How weldscore™ works – Lincoln Electric IM8002 POWER WAVE MANAGER User Manual
Page 95: Chapter 11, Chapter 11 training, Before you begin training a weld, Weldscore
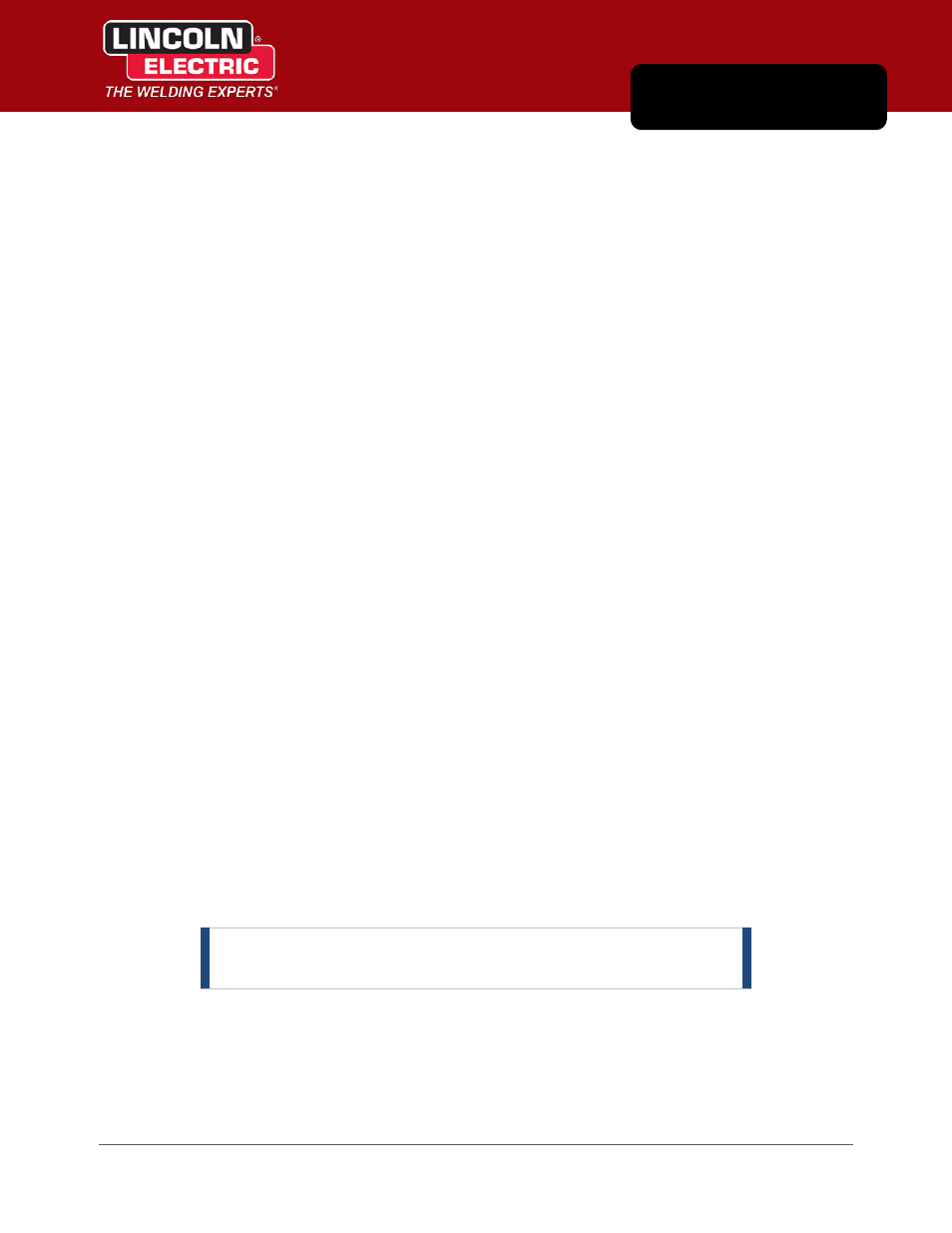
IM8002
Power Wave® Manager User Manual
11.1
Chapter 11
Training
For third-generation Welding Power Sources, you need to create training models in order to use
WeldScore™. For second-generation power sources (which do not support WeldScore™), training models
simply help you set limits for current, voltage and wire feed speed. You use both the Profile limits tab
(page 10.7) and the Training section (this chapter) to maintain your Weld Profiles.
Before You Begin Training a Weld
Before you begin setting up your Weld Profiles and creating training models, you need to do some planning.
Planning the Weld Profiles helps make sure that they provide that consistent and repeatable process so
important for an accurate WeldScore™. Be sure you have completed the following before you begin
teaching welds on the Welding Power Source:
Read through this Training chapter in its entirety. Be sure you fully understand the nature of
WeldScore™ and how to create a training model.
Determine how many Weld Profiles you need.
Decide which Weld Profile numbers you want to use on this Welding Power Source.
Decide how many example welds you want to train for each Weld Profile you want to use. If you
train a small number of consistent and repeatable welds, you create a low tolerance for
variability in production. A larger number of training welds allows a bit of flexibility when
making welds in production.
Plan the attributes of each example weld in terms of parameter settings and physical changes.
Remember: You want to create an acceptable average for the training model using these
individual training welds. (Page 11.3 explains the welds to train in more detail.)
WeldScore™
WeldScore™, a new feature available in all third-generation Welding Power Source models (including the
Power Wave® i400, C300, S350, S500 and AC/DC 1000 SD), can be used to support a weld quality control
program. It assigns a score to welds on a 0% to 100% scale that indicates the acceptability of the weld. The
score is based on a comparison to previously trained welding conditions. A weld with a score of 85% to
90% or above can be considered, with a reasonable amount of confidence, to be an acceptable weld.
WeldScore™ can be used independently on the power source or together with Production Monitoring™ or
CheckPoint™.
NOTE |
WeldScore™ is not a guarantee of quality and is not
intended to replace a quality control system.
How WeldScore™ Works
Traditional weld-monitoring systems measure current and voltage and must then guess what the Welding
Power Source is trying to do before attempting to determine how well it is actually doing it. WeldScore™ is
built right into the Welding Power Source control system, which gives the control system a significant
advantage by removing the guesswork involved with how the power source should be functioning. In