Polled i/o connection – Lincoln Electric IM8002 POWER WAVE MANAGER User Manual
Page 49
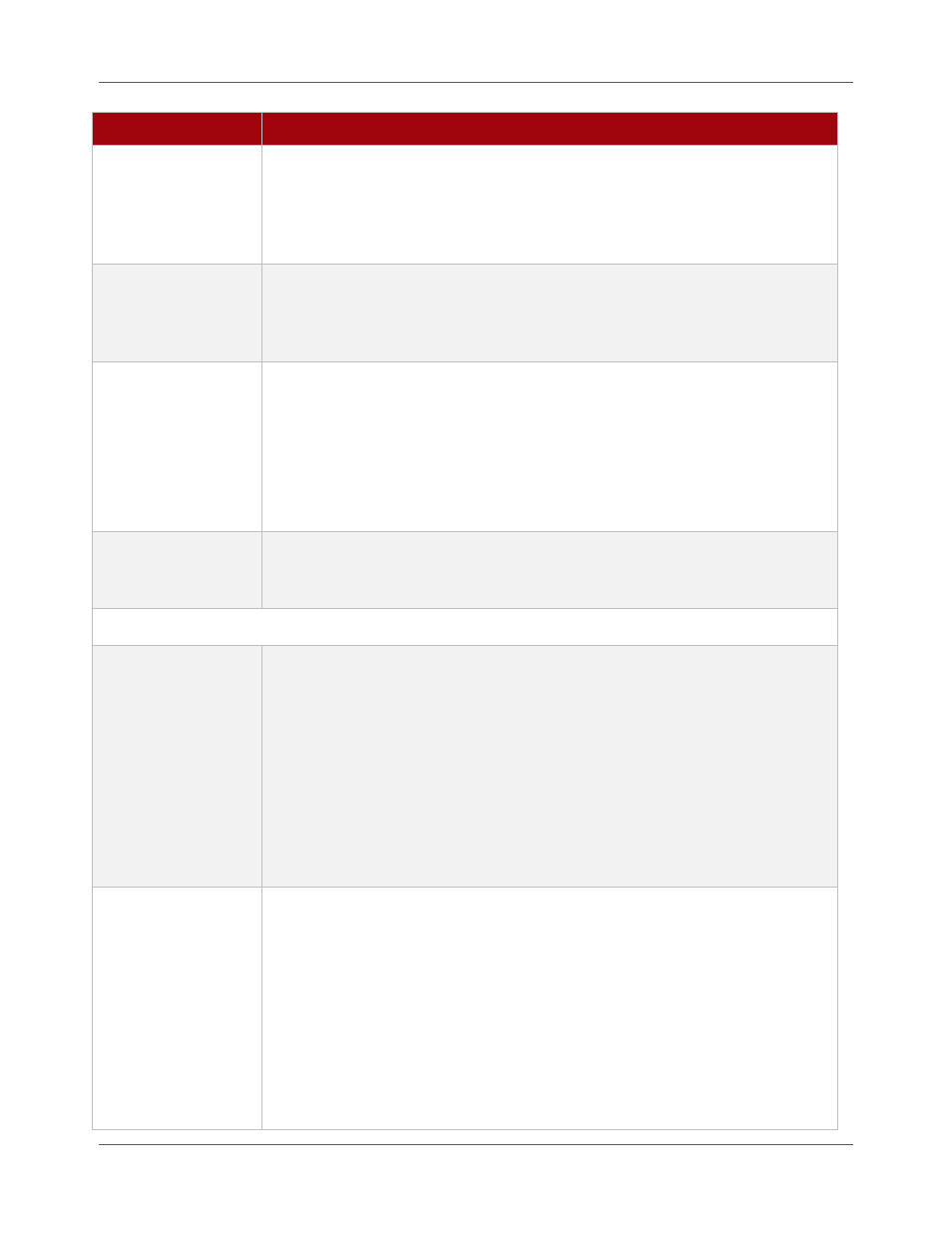
DeviceNet
Chapter 7. Network Settings
IM8002
Power Wave® Manager User Manual
7.7
Field
Description
TAST update
frequency
This parameter is used for Through the Arc Seam Tracking (TAST). The lower
the number the more often the feedback is updated, but higher the system load
on the boards. In general, if TAST is being used, this frequency is set to a value
between 10 and 20. Otherwise, a value of 100 is usually acceptable. This value
is only relevant for the PW455, 455M, 655, 355, and ACDC1000.
Meter time constant
This parameter sets the filtering of the feedback data. The default value of 400
is usually used unless TAST is being done. With TAST, this field is usually set to a
value around 75. This value is only relevant for the PW455, 455M, 655, 355,
and ACDC1000.
Analog scans
between updates
This determines how often the analog input channels (i.e., workpoint, trim, and
wave control) update the system in terms of polled I/O scans. For example, if
you enter 50, every 50th I/O scan will be accepted.
The setting of this item depends on how often the Welding Power Source is
scanned. For systems with a scan rate of 200 or more, the default is generally
50. For systems with very low scan rates, such as 10 Hz, a setting as low as 2
might be needed.
Cold-inch wire feed
speed
This parameter sets the feed speed of the wire while cold-inching or jogging the
wire. This value is used for either cold-inching forward (Jog +) or cold-inching
reverse (Jog -). This value is in units of inches per minute (IPM).
Polled I/O Connection
Workpoint input
This indicates whether the values passed to the system through the analog
DeviceNet channels for the Workpoint parameter are raw values or scaled
engineering values. For most applications, choose Engineering units.
For example, when the Workpoint is in inches per minute and you choose
Engineering units, a value between 50 and 800 might be expected to be
commanded on the DeviceNet analog input for the Workpoint. This would
represent a value of 50 to 800 inches per minute.
When you choose the Unscaled values option, the commands for Workpoint
range from 0 to 32767, corresponding to the minimum and maximum
Workpoint of the selected Weld Mode.
Trim/Wave
Control input
This indicates whether the values passed to the system through the analog
DeviceNet channels for the Trim and Wave Control parameters are raw values
or scaled engineering values.
For example, when the Trim is in volts and you choose Engineering units, a value
between 75 and 520 might be expected to be commanded on the DeviceNet
analog input for the Trim. This would represent a value of 7.5 to 52.0 volts.
When you choose the Unscaled values option, the commands for Trim and
Wave Control range from -32768 to 32767 with 0 representing a nominal value.
A great majority of applications will require Trim and Wave Control command
values to be set near the nominal value.