2 fail-safe action, 3 operation result integration, 4 recording of revisions – Yokogawa YVP110 User Manual
Page 74: 7 control parameters, 8 temperature and pressure measurement, Fail-safe action -5, Operation result integration -5, Recording of revisions -5, Control parameters -5, Temperature and pressure measurement -5
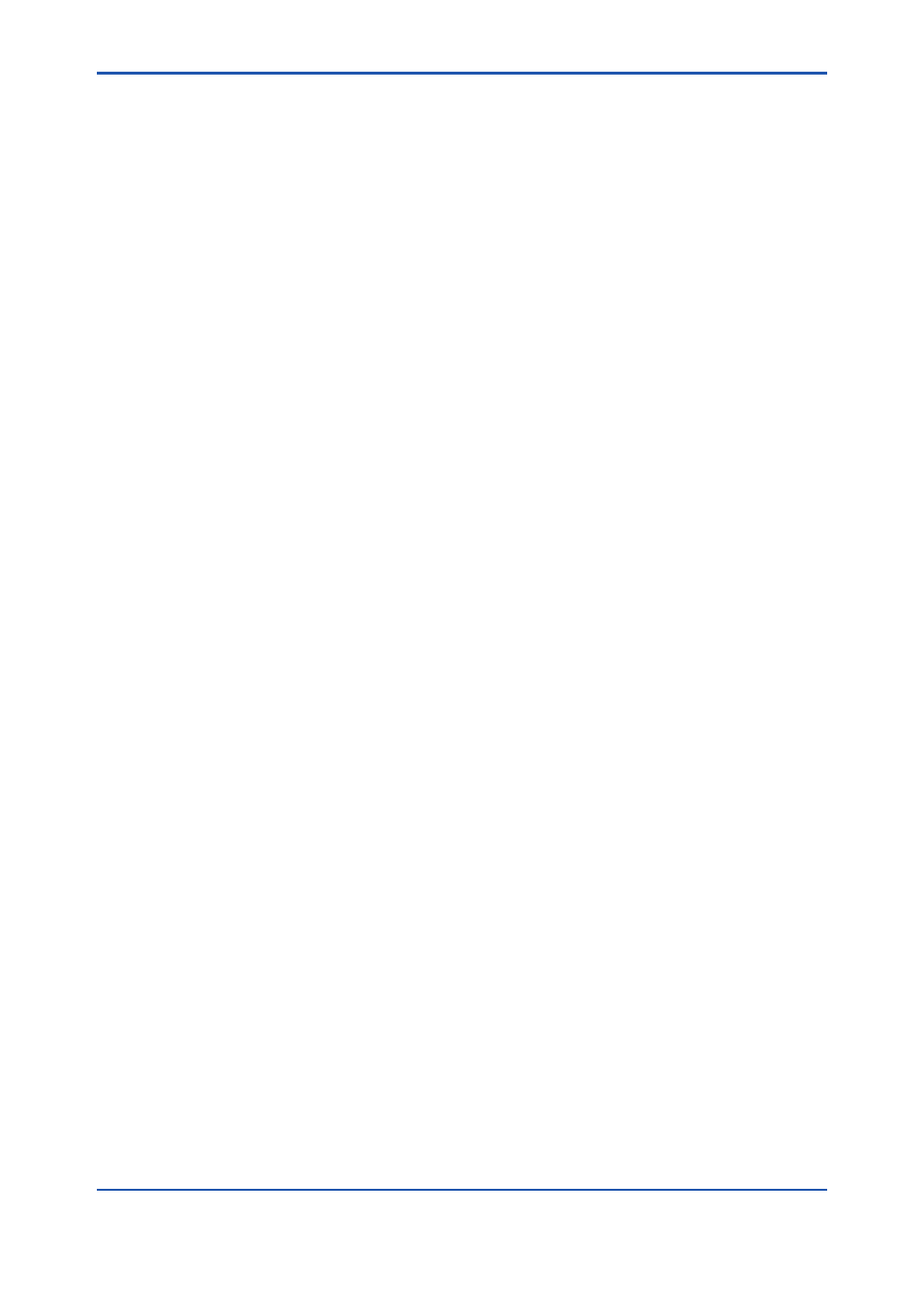
<12. Transducer Block>
12-5
IM 21B04C01-01E
12.6.2 Fail-safe Action
If the “A/D converter failure,” “position sensor
failure,” or “deviation error” event occurs in the
XD_ERROR described above, the transducer block
activates the specified fail-safe action by cutting the
current signal to I/P module to zero. In addition, in
the event of “position sensor failure” or “deviation
error,” the fail-safe action will not be deactivated
even when the cause of the failure/error is
cleared. Writing “Clear non-latch” to the parameter
RELEASE_FAILSAFE will finally deactivate the
fail-safe action in this case. The fail-safe action
activated in the event of “A/D converter failure” will
be deactivated automatically when the cause of the
failure is cleared.
12.6.3 Operation Result Integration
The YVP110 has a function to integrate the
following operation result quantities individually.
To reset an integrated quantity, write 0 to the
corresponding parameter.
• TOTAL_CYCLE_COUNT:
Incremented by 1 at each change in the
direction of the valve action and indicates the
total number of times of changes in direction of
valve actions.
• TOTAL_TRAVEL:
Total travel distance of the stem position shown
as a percentage of the valve position span.
• TOTAL_OPEN_TIME and TOTAL_CLOSE_
TIME:
TOTAL_CLOSE_TIME contains the integrated
time periods (in hours) when the valve position
is equal to or less than the thresholds previously
set in OPEN_CLOSE_THRESHOLD. TOTAL_
OPEN_TIME is the integrated time periods (in
hours) other than TOTAL_CLOSE_TIME.
• TOTAL_NEAR_CLOSE_TIM:
Total time period (in hours) when the valve
position is within the threshold set in NEAR_
CLOSE_THRESHOLD.
• SERVO_WARN_COUNT:
Total number of times the servo output drift
warning occurred.
Indicates the total number of times a drift
warning occurred regarding the output current
to the I/P module.
12.6.4 Recording of Revisions
When the user makes a change to the setting of a
static parameter, the change is counted-up in the
parameter ST_REV and update event is generated.
12.7 Control Parameters
The following control parameters in a YVP110 can
be set up by auto tuning: (For details, see section
A6.4)
SERVO_GAIN
SERVO_RESET
SERVO_RATE
SERVO_RATE_GAIN
SERVO_DEADBAND
SERVO_OFFSET
BOOST_ON_ THRESHOLD
BOOST_OFF_THRESHOLD
BOOST_VALUE
SERVO_I_SLEEP_LMT
SERVO_P_ALPHA
INTERNAL_GAIN
X_BOOST_ON_THRESHOLD *
X_BOOST_OFF_THRESHOLD *
X_BOOST_VALUE *
* Applicable only for Double Acting Type
12.8 Temperature and Pressure
Measurement
The YVP110 measures the surface temperature
of the amplifier and sets it in the parameter
ELECT_TEMP in the transducer block. The unit of
temperature is defined by TEMPERATURE_UNIT
and can be selected from:
1001 = °C
1002 = °F
A YVP110 with an optional pressure sensor can
measure the output air pressure to the valve
actuator and sets it in the parameter OUT_
PRESSURE. The unit of pressure is defined
by Unit Code in SPRING_RANGE and can be
selected from:
1133 = kPa
1137 = bar
1141 = psi
1145 = kgf/cm
2