Caution – Yokogawa YVP110 User Manual
Page 36
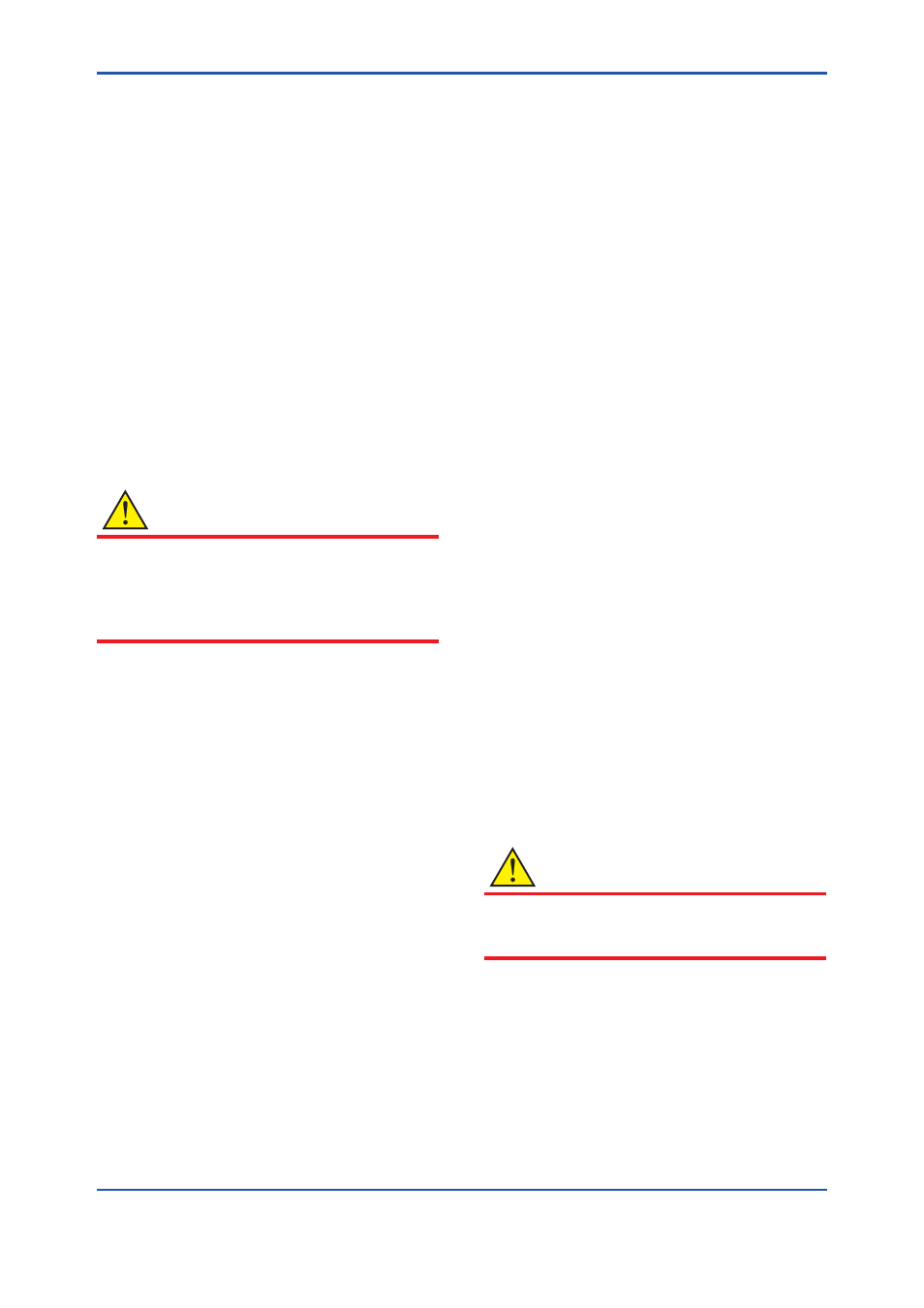
<5. Setup>
5-3
IM 21B04C01-01E
The tuning result will be written to AUTO_
TUNE_RESULT. The value of AUTO_TUNE_
RESULT is 255 and is displayed as “In
operation” while auto tuning is running, and will
change to 1 which is displayed as “Succeeded”
when auto tuning has finished successfully. In
the event of a warning or error, a value other
than those below will be displayed. For details,
see the specifications for the transducer block.
1 = succeeded
2 = canceled
255 = in operation
The values of the hysteresis of valve actions
and the air supply pressure measured during
auto tuning are stored in parameters of the
transducer block inside the YVP110. Note that
pressure data such as air supply pressure data
are available only for a YVP110 with an optional
pressure sensor.
CAUTION
Ensure that the pressure of the air supply to
the YVP110 positioner is regulated within the
specified range. If it differs from the pressure
during actual operation, or if it is unstable,
optimum tuning results may not be obtained.
The following parameters are tuned by carrying out
auto tuning: (For details, see secction A6.4)
SERVO_GAIN
(static loop gain of internal valve control loop)
SERVO_RESET (integral time)
SERVO_RATE (derivative time)
SERVO_RATE_GAIN (derivative gain)
SERVO_DEADBAND
(dead band of integral action)
SERVO_OFFSET (offset of integral action)
BOOST_ON_THRESHOLD
(threshold to switch on the boost action)
BOOST_OFF_THRESHOLD
(threshold to switch off the boost action)
BOOST_VALUE
SERVO_I_SLEEP_LMT
(timer setting for integral action)
SERVO_P_ALPHA
(multiplication coefficient for the square of
proportional factor)
INTERNAL_GAIN
(total gain of I/P module,control relay and the
valve)
X_BST_ON_THRESHOLD *
(the addition value to threshold for switching
on boost action for exhaust.)
X_BST_OFF_THRESHOLD *
(the addition value to threshold for switching
off boost action for exhaust)
X_BOOST_VALUE *
(the addition boost value for exhaust)
*Applicable only for Double Acting Type
Normally, control parameters need not be
readjusted after auto tuning. (Should there be a
problem, see Chapter 16, “Troubleshooting.”)
If you want to carry out fine adjustments of the
zero-point and span settings, perform the travel
calibration as follows.
l
Travel Calibration
If the full stroke of the valve is too large for the
maximum required flow rate, you can change
the span of the travel by carrying out a travel
calibration.
(1) First, vary the value of FINAL_VALUE.value
(see caution) to move the stem and adjust the
stem to the desired point that you want to set as
the 100% position.
(2) Next, write 3 to TRAVEL_CALIB_EXEC. This
changes the span while leaving the zero point
unchanged.
TRAVEL_CALIB_EXEC:
1 = off
2 = 0%-point calibration (no change to span)
3 = span calibration (no change to 0% point)
4 = 50%- point calibration
(no change to either span or 0% point)
CAUTION
Only when the target mode's in both the AO and
transducer blocks are O/S, can FINAL_VALUE.
value be written.
The result of the travel calibration will be written to
TRAVEL_CALIB_RESULT.