IAI America RCM-GW-DV User Manual
Page 64
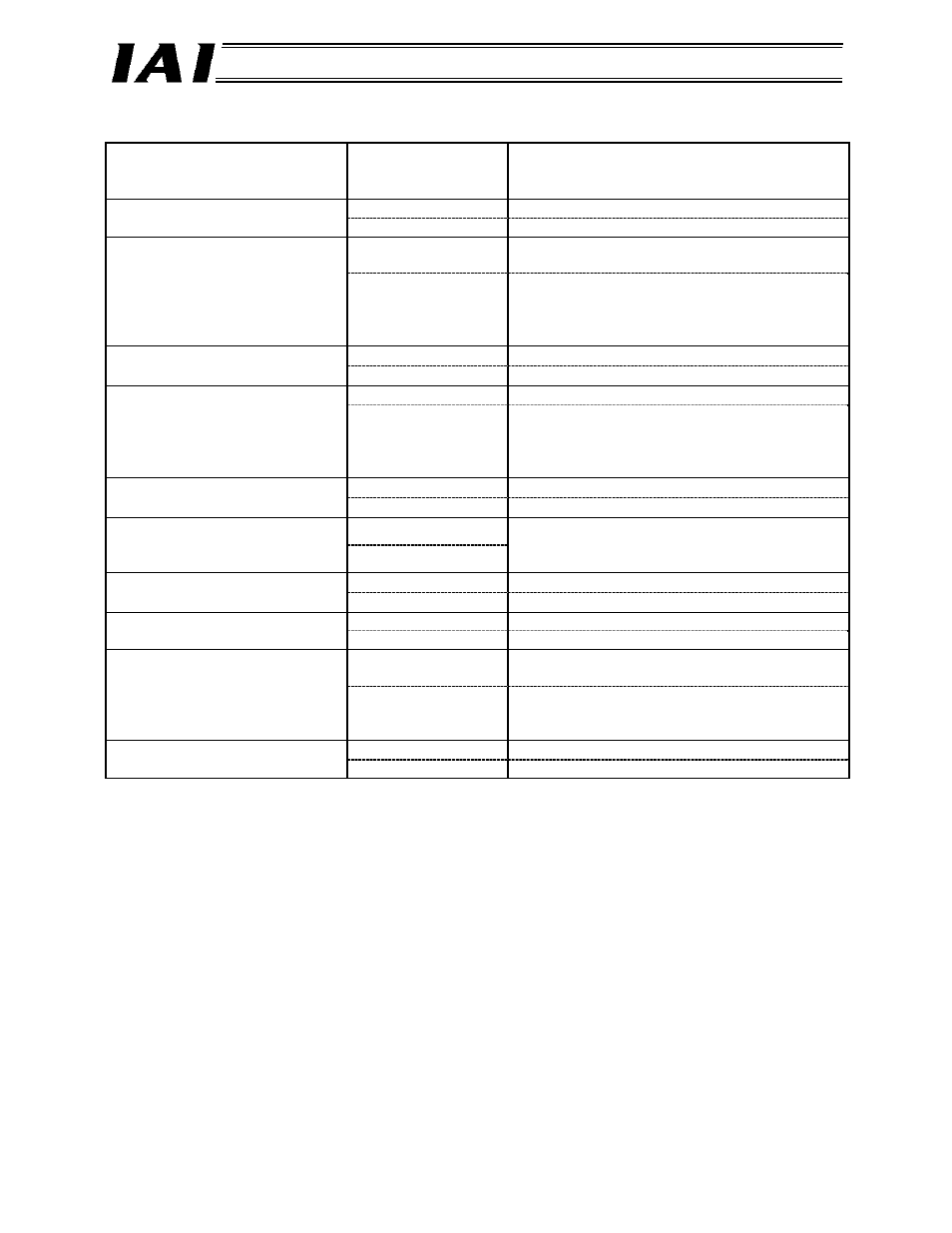
58
DeviceNet Gateway
With each function, the top row indicates positioner operation, while the bottom row indicates simple direct
operation.
Key function
: Direct control
Δ: Indirect
control
X: Disabled
Remarks
Home return operation
Δ
Positioning operation is performed by specifying an
applicable number in the position table. *1
Positioning operation
Δ
Set all positioning data other than position data
in the position table, and specify the position
data and position table number at the same
time.
Δ
Set in the position table. *1
Speed/acceleration setting
Δ
Set in the position table.
Δ
Set in the position table. *1
Pitch (incremental) feed
X
Pitch feed data cannot be processed directly.
The host PLC must issue each command by
adding/subtracting the pitch-feed distance data
to/from the current position.
Δ
Set in the position table. *1
Push-motion operation
Δ
Set in the position table.
Δ
Speed change during movement
Δ
Speed change is implemented by combining
two or more position numbers. (Refer to the
operation manual for your controller.)
Δ
Set in the position table. *1
Operation with acceleration and
deceleration set differently
Δ
Set in the position table.
Pause
The zone signal output is set in the position
table or via a parameter. *2
Zone signal output
X
The current position data is constantly output
from the Gateway, so use the PLC to monitor
the current position data. *3
*4
PIO pattern selection
X *5
*1 The position table data can be written (rewritten) from the PLC using a request command (position
table data write). To use this function, the necessary data must be written to the position data
beforehand.
*2 The current position data can be read using a request command, but this data is not output constantly.
*3 No strobe signal is provided for the current position data. To check the current position from the PLC
during movement, set zones and check if the data has remained inside a given zone for at least two
scans.
*4 This parameter (No. 25) is not available with PCON-SE, ACON-SE and ERC2-SE controllers.
*5 Set the PIO pattern selection parameter (No. 25) of each connected controller to “0” (standard type).