IAI America RCM-GW-DV User Manual
Page 103
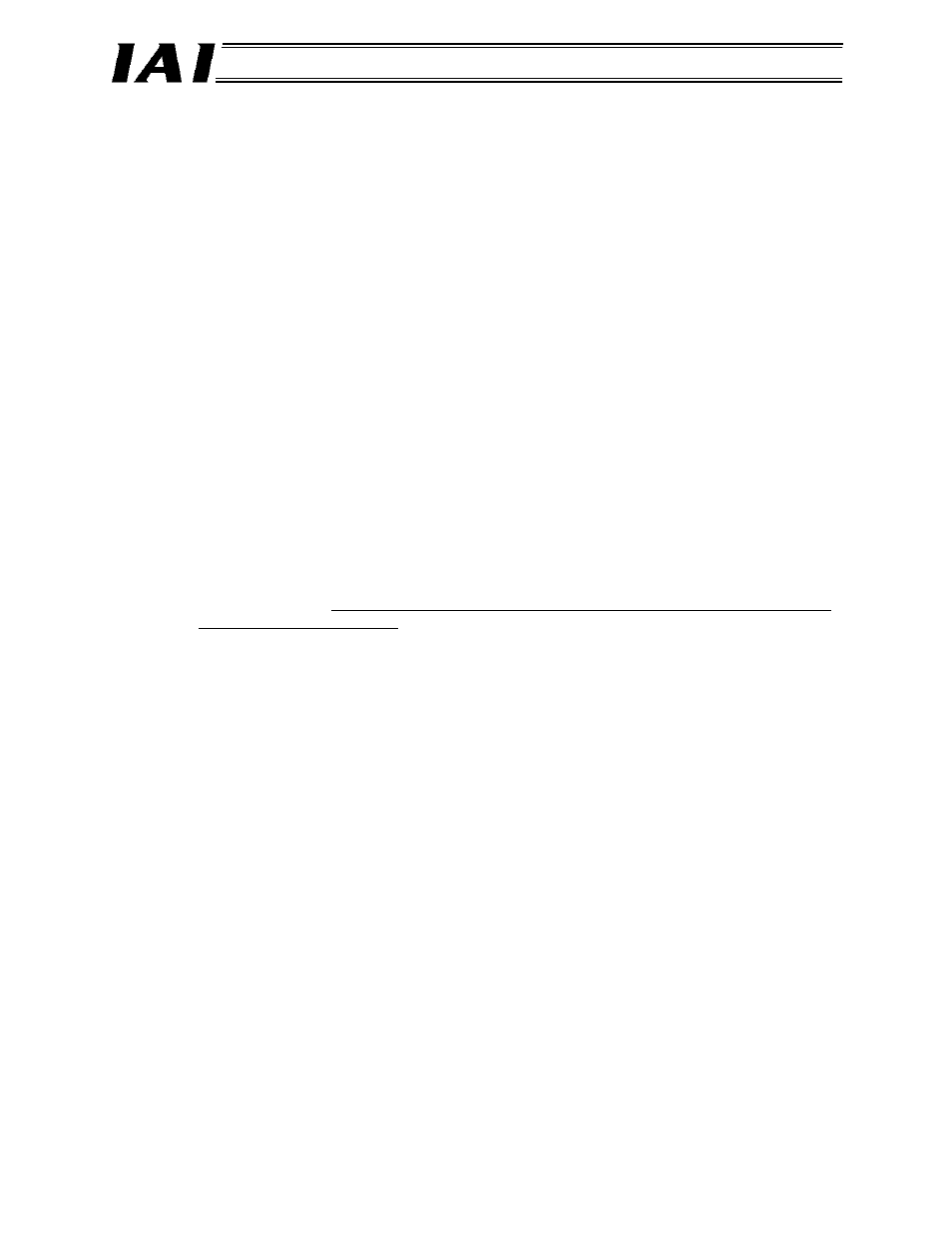
97
DeviceNet Gateway
(5) Simple direct operation (Command specification mode)
The actuator is operated by writing the target position data in the PLC’s link register and specifying
other data such as the speed, acceleration/deceleration, positioning band and push-current limiting
value in the position table.
Preparation
Set all position data other than the target position (= speed, acceleration/deceleration, positioning
band and push-current limiting value, etc.) in the position table.
Operation
[Normal positioning operation]
[1] Set the target position data in the position data specification register.
[2] Set the position number in the command position number register.
[3] Turn the start command (CSTR) signal “1” (ON) after confirming that the position complete
(PEND) signal is “1” (ON) or moving (MOVE) signal is “0” (OFF).
The target position data is read by the controller at the “0” (OFF)
“1” (ON) edge of CSTR
(= leading edge of the signal).
[4] PEND turns “0” (OFF) tdpf after CSTR has turned “1” (ON).
[5] Turn CSTR “0” (OFF) after confirming that the PEND signal has turned “0” (OFF) or MOVE
signal has turned “1” (ON).
Do not change the target position data until CSTR is turned “0” (OFF).
[6] MOVE turns “1” (ON) simultaneously as PEND turns “0” (OFF) or within 1 Mt thereafter.
[7] The current position data is constantly refreshed. When the remaining travel falls within the
specified positioning band (INP), PEND turns “1” (ON) if CSTR is “0” (OFF).
Accordingly, when reading the data of the position at which the actuator has stopped upon
completion of positioning, check the data after waiting for an appropriate time after PEND has
turned “1” (ON) (= time needed to complete the remaining travel).
Also take note that the current position data may change slightly due to vibration, etc., even
when the actuator is stopped.
[8] MOVE turns “0” (OFF) simultaneously as PEND turns “1” (ON) or within 1 Mt thereafter.
[9] The target position data can be changed while the actuator is moving.
To change the target position while the actuator is moving, change the target position data,
wait for an elapse of at least the PLC scan time, and then turn CSTR “1” (ON).
In this case, turn CSTR “1” (ON) for at least tdpf. Also wait for 1 Mt or more after CSTR is
turned “0” (OFF) until CSTR is turned “1” (ON) again.
[Push-motion operation]
Push-motion operation is performed by setting the push-current limiting value in the “Push” field of
the position table in the preparation stage and then performing positioning by specifying the
applicable position number.