2 actuator operation pattern, 3 various controller settings, 1) setting the axis number – IAI America RCM-GW-DV User Manual
Page 125: 2) setting the baud rate for sio communication, 3) creating a position table, Actuator operation pattern, Various controller settings, Caution
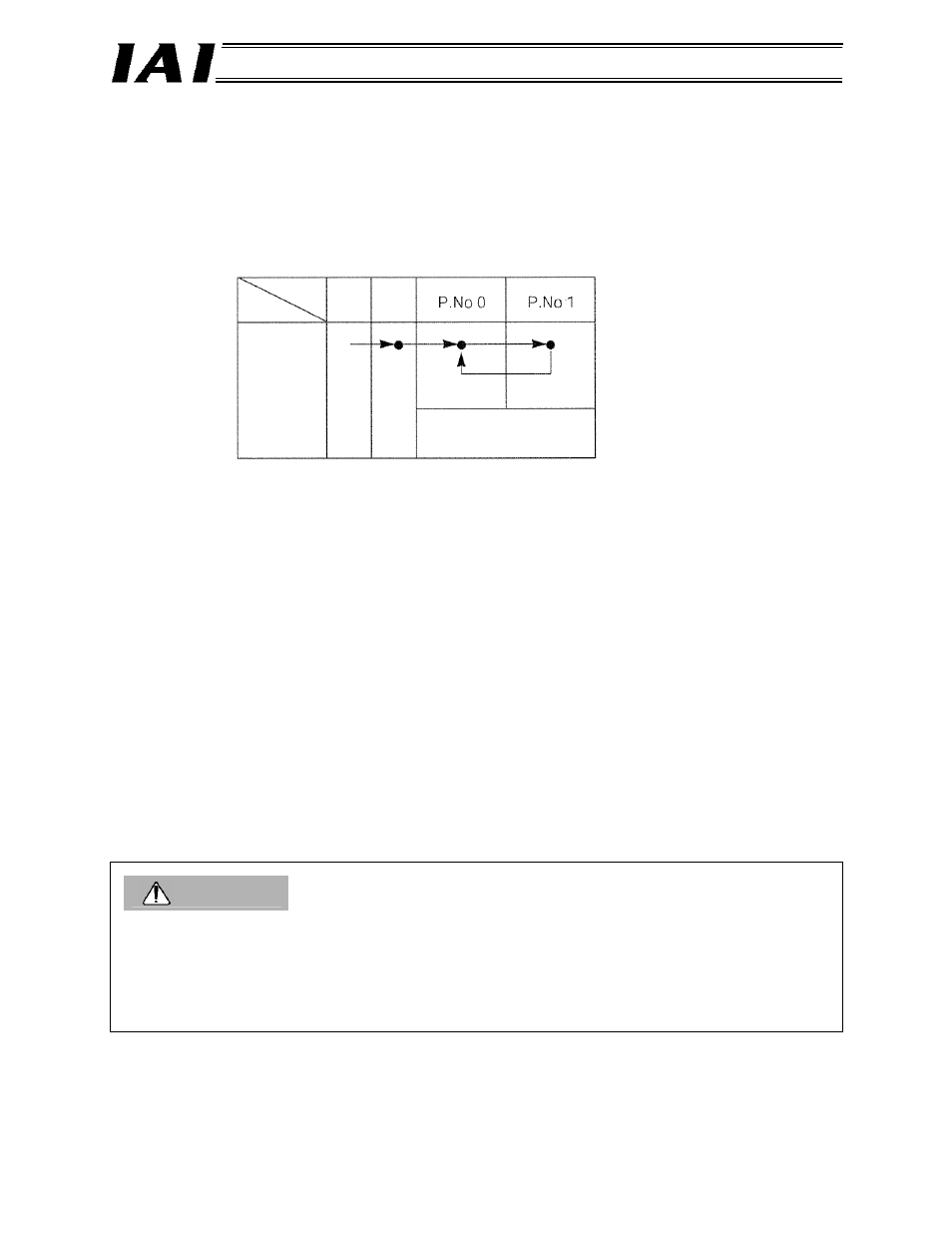
119
DeviceNet Gateway
9.2
Actuator Operation Pattern
Both linked axes 0 and 1 are operated in the position-number specification mode.
The operation pattern is specified below. Specifically, position No. 0 is specified to cause the actuator to
move to position No. 0 after completion of home return. The actuator pauses for 1 second in this position,
after which position No. 1 is specified to cause the actuator to move to position No. 1. The actuator
pauses for 1 second in this position, after which position No. 0 is specified. These steps are repeated to
make the actuator move back and forth between position Nos. 0 and 1.
9.3
Various Controller Settings
(1) Setting the axis number
Refer to 8.2.
(2) Setting the baud rate for SIO communication
Refer to 8.2.
(3) Creating a position table
After (2), perform the following steps in the initial window of the PC software:
[1] Click
Position (T), and then select Edit/Teach (E).
[2] Select axis 0, click >, and then click OK.
[3] When the position data edit window for axis 0 appears, enter the applicable data.
[4] Transfer the data to the controller, and then click X to close the edit window.
[5] Repeat steps [1] to [4] by selecting axis 1.
[6] Shut down the PC software.
[7] Remove the PC cable from the Gateway unit, and turn the port switch OFF.
Caution
After specifying any of the various settings pertaining to each SIO-linked axis or creating a position
table by connecting the PC (software) or teaching pendant to the Gateway Unit, always change the
MANU operation mode to
pendant.
Otherwise, the controller cannot be started from the PLC next time.
For details, refer to the operation manual for your PC software or teaching pendant.
Axis
Position
Home
Linked axis 0
Linked axis 1
The actuator pauses for 1
second after completing
positioning.