2 direct numerical specification mode, Direct numerical specification mode – IAI America RCM-GW-DV User Manual
Page 53
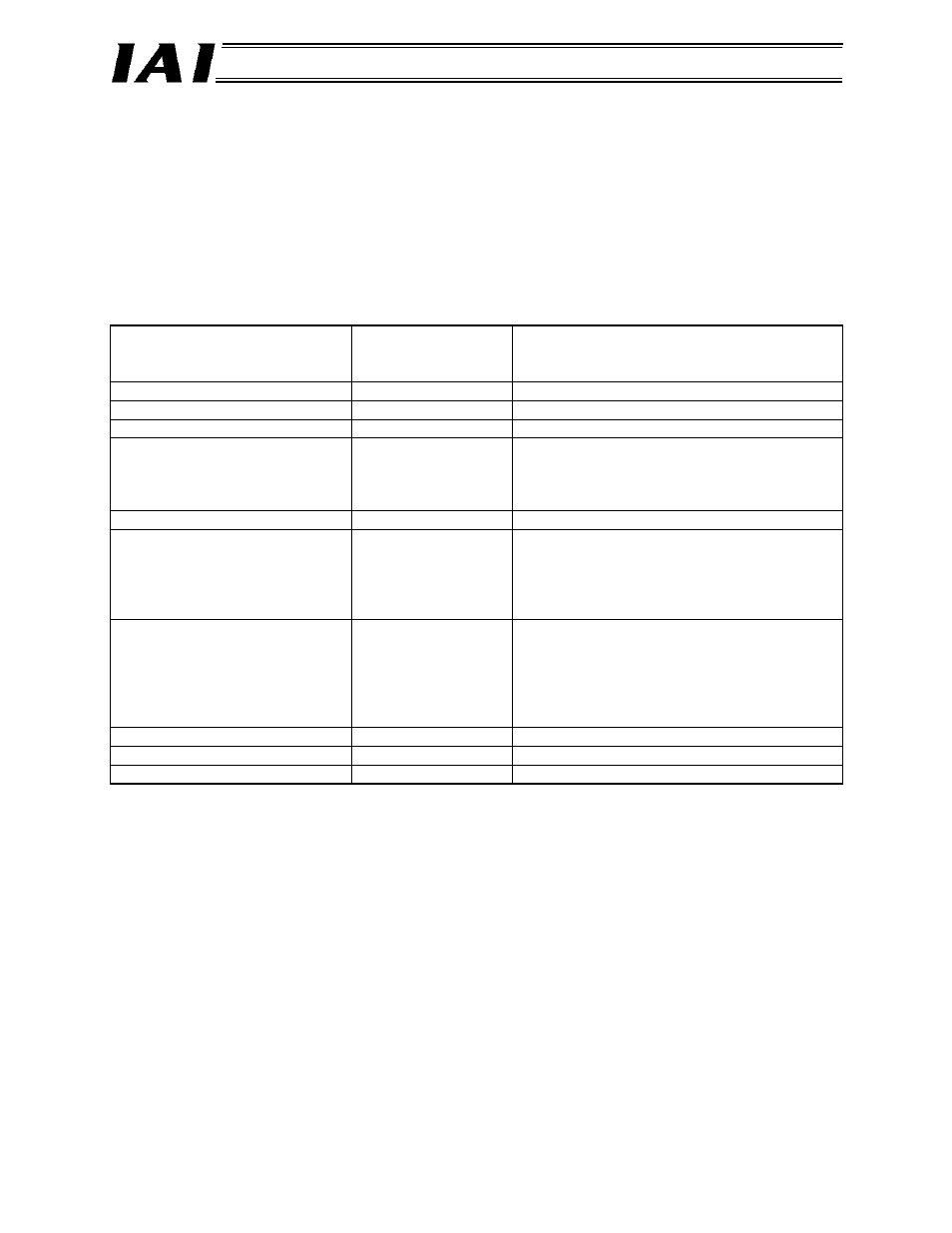
47
DeviceNet Gateway
6.2
Direct Numerical Specification Mode
In the direct numerical specification mode, the actuator is operated by specifying the position data, speed,
acceleration/deceleration, positioning band (push band), and current-limiting value for push-motion
operation, directly in numerical values.
There are five patterns, each accommodating a different number of connected axes. (The pattern is set
using the mode setting switch SW1.)
The current position data can be read at any time.
There is no need to set the position table for each axis.
The key functions that can be controlled in this mode are summarized in the table below.
Key function
: Direct control
Δ: Indirect
control
X: Disabled
Remarks
Home return operation
Positioning operation
Speed/acceleration setting
Pitch (incremental) feed
X
Pitch feed data cannot be processed directly.
The host PLC must issue each command by
adding/subtracting the pitch-feed distance
data to/from the current position.
Push-motion operation
Speed change during movement
Speed data is accepted at the start of
positioning. To change the speed during
movement, therefore, change the speed data
during movement and then restart the
positioning operation.
Operation with acceleration and
deceleration set differently
Acceleration/deceleration data is accepted at
the start of positioning. To specify a
deceleration different from the acceleration,
therefore, change the deceleration data
during movement and then restart the
positioning operation.
Pause
Zone signal output
X
Monitor the current position using the PLC. *1
PIO pattern selection
X
*2
*1 No strobe signal is provided for current position data. To check the current position from the PLC
during movement, set zones and check if the data has remained inside a given zone for at least two
scans.
*2 Set the PIO pattern selection parameter (No. 25) of each connected controller to “0” (standard type).
(PCON-C/CG, ACON-C/CG, SCON-C, ERC-2NP/PN)