HEIDENHAIN TNC 620 (34056x-04) Cycle programming User Manual
Page 297
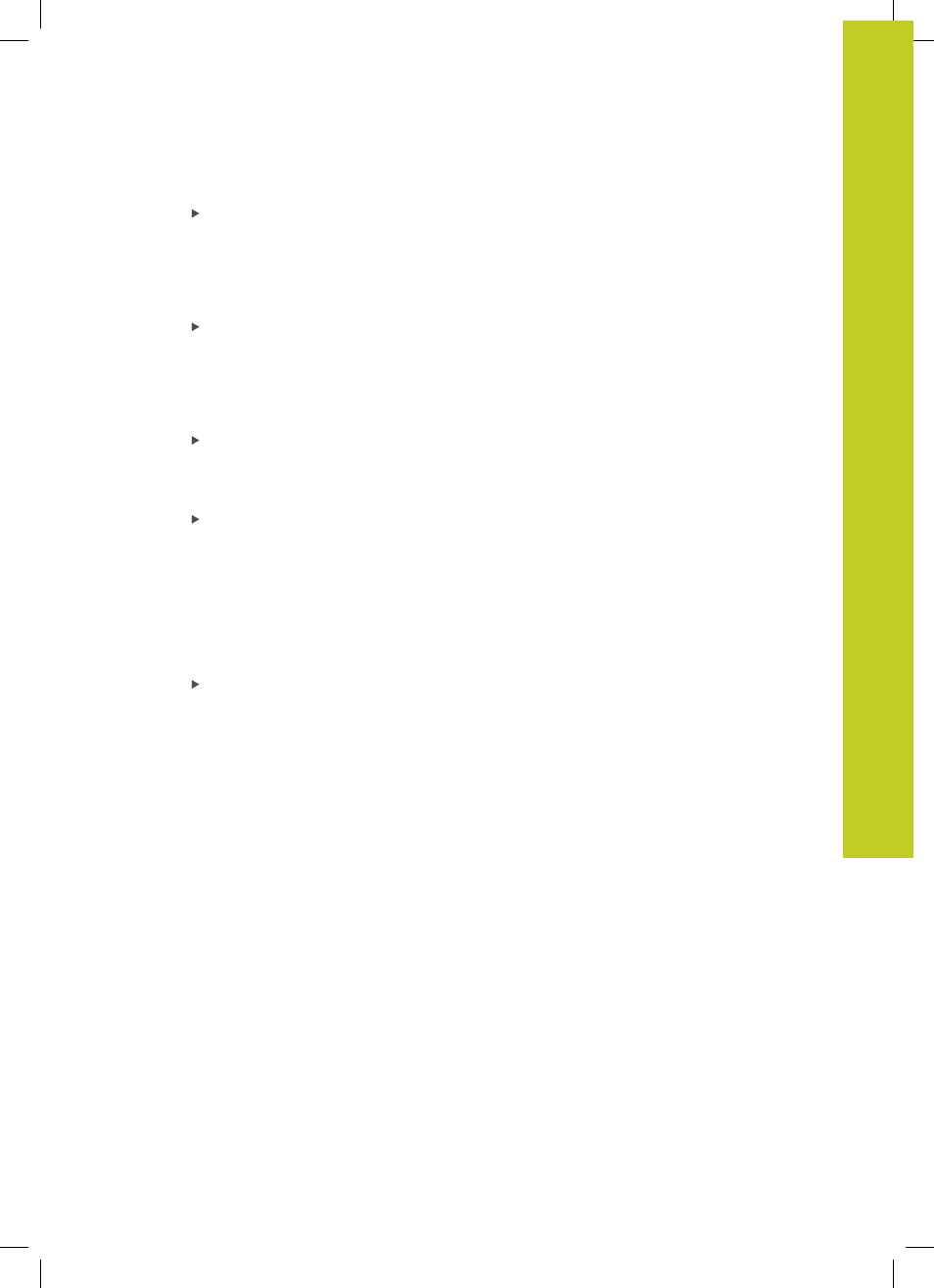
BASIC ROTATION compensation via rotary axis (Cycle 403, DIN/
ISO: G403, software option 17)
14.5
14
TNC 620 | User's Manual Cycle Programming | 5/2013
297
Axis for compensation movement Q312: Define
which rotary axis the TNC uses to compensate the
measured misalignment:
4
: Compensate misalignment with rotary axis A
5
: Compensate misalignment with rotary axis B
6
: Compensate misalignment with rotary axis C
Set to zero after alignment Q337: Define whether
the TNC should set the display of the aligned rotary
axis to 0:
0
: Do not set the rotary axis display to 0 after
alignment
1
: Set the rotary axis display to 0 after alignment.
Number in table Q305: Enter the number in the
preset table/datum table in which the TNC is to set
the rotary axis to zero. Only effective if Q337 is set
to 1. Input range 0 to 2999
Measured value transfer (0, 1) Q303: Specify if
the determined basic rotation is to be saved in the
datum table or in the preset table:
0
: Write the measured basic rotation as datum shift
active datum table. The reference system is the
active workpiece coordinate system
1
: Write the measured basic rotation into the
preset table. The reference system is the machine
coordinate system (REF system).
Reference angle? (0=ref. axis) Q380: Angle
with which the TNC is to align the probed straight
line. Only effective if the rotary axis C is selected
(Q312=6). Input range -360.000 to 360.000