HEIDENHAIN TNC 620 (34056x-04) Cycle programming User Manual
Page 232
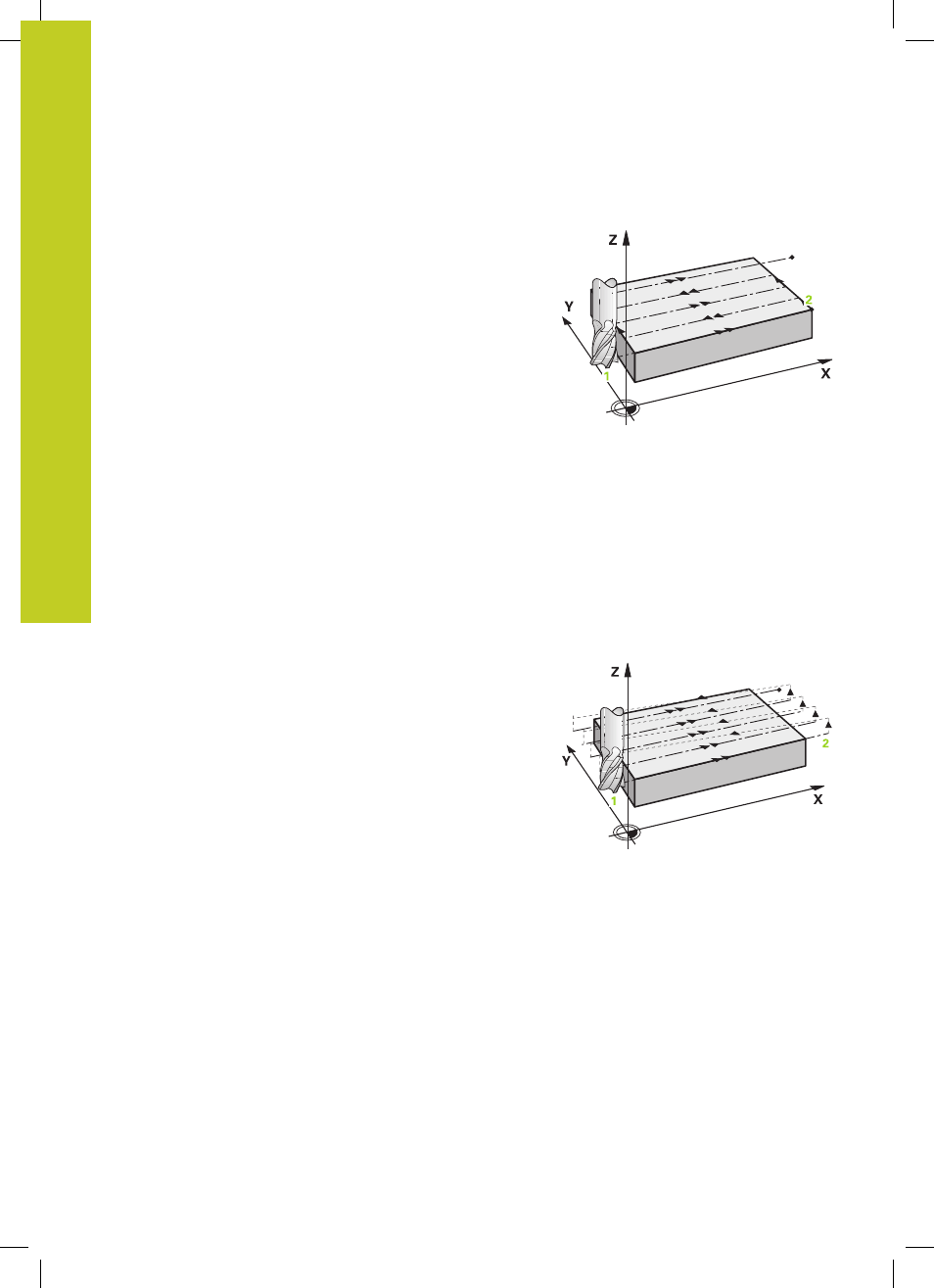
Fixed Cycles: Multipass Milling
10.4
FACE MILLING (Cycle 232, DIN/ISO: G232, software option 19)
10
232
TNC 620 | User's Manual Cycle Programming | 5/2013
Strategy Q389=1
3 The tool subsequently advances to the stopping point
2
at the
programmed feed rate for milling. The end point lies
within
the surface. The control calculates the end point from the
programmed starting point, the programmed length and the tool
radius.
4 The TNC offsets the tool to the starting point in the next pass
at the pre-positioning feed rate. The offset is calculated from
the programmed width, the tool radius and the maximum path
overlap factor.
5 The tool then moves back in the direction of the starting point
1
. The motion to the next line occurs within the workpiece
borders.
6 The process is repeated until the programmed surface has been
completed. At the end of the last pass, the tool plunges to the
next machining depth.
7 In order to avoid non-productive motions, the surface is then
machined in reverse direction.
8 The process is repeated until all infeeds have been machined. In
the last infeed, simply the finishing allowance entered is milled
at the finishing feed rate.
9 At the end of the cycle, the tool is retracted in
FMAX to the 2nd
set-up clearance.
Strategy Q389=2
3 The tool subsequently advances to the stopping point
2
at the
programmed feed rate for milling. The end point lies outside
the surface. The control calculates the end point from the
programmed starting point, the programmed length, the
programmed safety clearance to the side and the tool radius.
4 The TNC positions the tool in the spindle axis to the set-up
clearance over the current infeed depth, and then moves at the
pre-positioning feed rate directly back to the starting point in the
next line. The TNC calculates the offset from the programmed
width, the tool radius and the maximum path overlap factor.
5 The tool then returns to the current infeed depth and moves in
the direction of the next end point
2
.
6 The multipass process is repeated until the programmed
surface has been completed. At the end of the last pass, the
tool plunges to the next machining depth.
7 In order to avoid non-productive motions, the surface is then
machined in reverse direction.
8 The process is repeated until all infeeds have been machined. In
the last infeed, simply the finishing allowance entered is milled
at the finishing feed rate.
9 At the end of the cycle, the tool is retracted in
FMAX to the 2nd
set-up clearance.