0 electrical and wiring, 1 general, 2 supply wiring – Reznor RECC Unit Installation Manual User Manual
Page 41
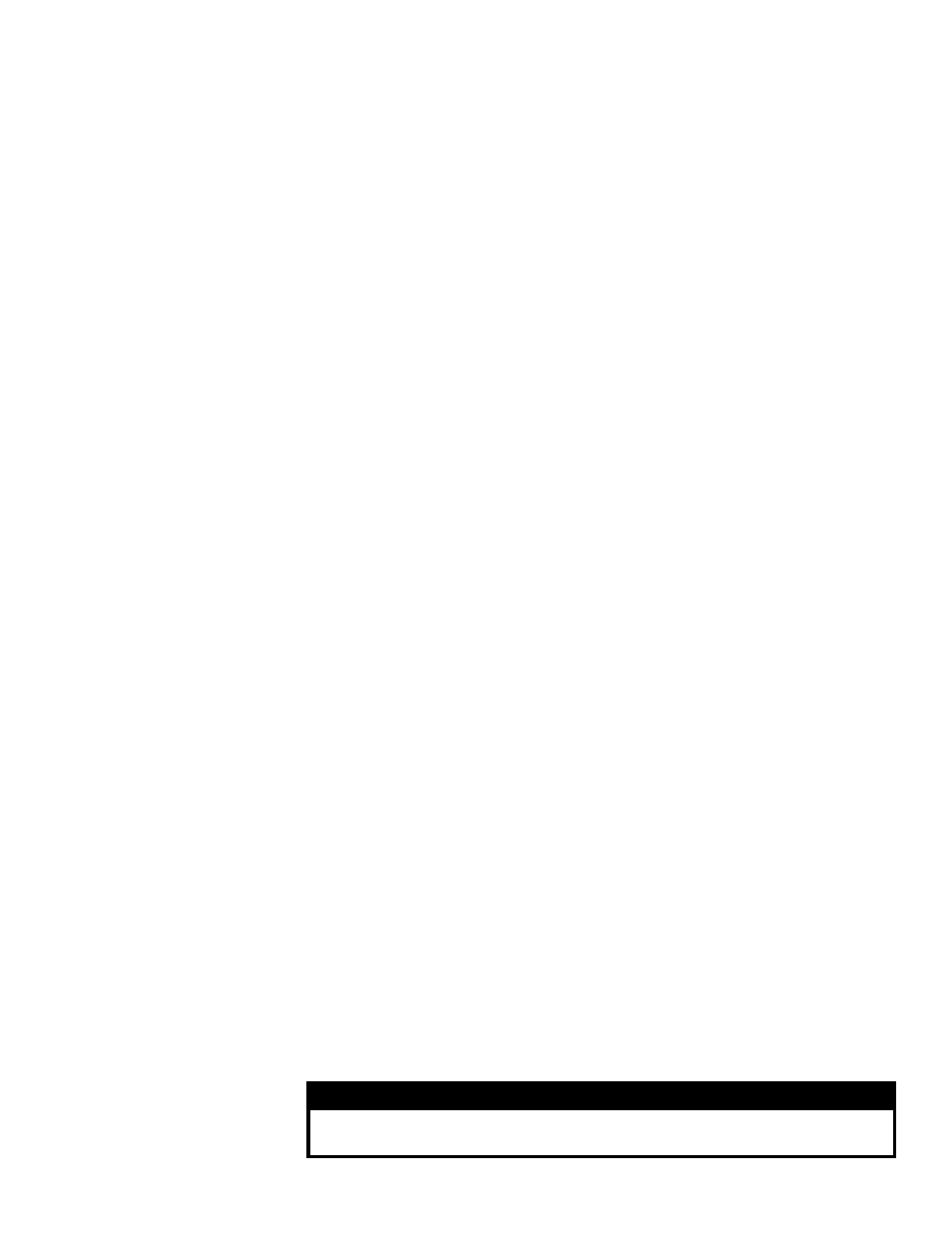
Form I-MAPSIII&IV, P/N 222917R9, Page 41
6.6.6 Optional
Variable Frequency
Drive and Controls
When an optional variable frequency drive is ordered, the motor will operate on vary-
ing speeds as determined by the electrical frequency. The drive requires remote field
installation. The minimum ambient temperature for installing a VFD is 18°F (-8°C).
Maximum distance of the VFD from the unit is 50 ft (15M). Follow the manufacturer's
instructions included with the package and the system wiring diagram. (
NOTE: If spe-
cific wiring for desired VFD operation was not requested on the order, the VFD wiring
on the system wiring diagram is for two speed.)
Depending on which control (Option VFC) was selected, the variable frequency drive
is controlled by a wall-mounted two or three speed control, by duct or building static
pressure, or by a space CO2 monitor. See control information in Paragraph 8.2.
Generally, high speed is used for cooling and low speed for heating. Minimum high
speed is 60 Hertz. Maximum speed for low speed heating is the frequency that will
provide the maximum temperature rise of the heater. Maximum allowable temperature
rise for a MAPS
®
gas heat section is 100°F.
Follow the variable frequency controller manufacturer’s instructions to program the
variable frequency drive settings.
The formula for motor speed is N = 120 x f/p where N is speed; f is frequency;
and p is number of poles (3600 RPM motor has 2 poles; an 1800 RPM motor
has 4 poles).
Example: 1800 RPM motor on 60Hz; N = 120 x 60/4 = 1800
1800 is synchronous speed; assume 2% slip. Motor will run
between 1750 and 1790 RPM at full load depending on design.
Run the same motor at 45Hz (120 x 45/4 = 1350). 1350 RPM
less 2% slip equals about 1300 RPM.
6.6.4 Blower Bearings
The blower on systems with less than a 10 HP motor are permanently lubricated car-
tridge ball bearings and do not require greasing. The bearings on systems with a 10HP
motor are pillow block ball bearings and are equipped with a grease fitting. Refer to
Form O-MAPS
®
Cabinet ABC or O-MAPS
®
Cabinet D for maintenance instructions.
All electrical wiring and connections, including electrical grounding MUST be made
in accordance with the National Electric Code ANSI/NFPA No. 70 (latest edition). In
addition, the installer should be aware of any local ordinances or electric company
requirements that might apply.
7.1 General
Check the rating plate for the supply voltage and current requirements. Run a separate
line voltage supply directly from the main electrical panel, making connection at the
disconnect switch.
7.2 Supply Wiring
7.0 Electrical and
Wiring
6.6.5 Blower Rotation
- Cabinets A, B, C
Each blower housing is marked for proper rotation. Check blower rotation with the
arrow on the housing. If actual rotation is not correct, interchange the two wires on
the 3-phase supply connections at the terminal block. Do not change load side wiring.
7.2.1 Disconnect
Switch
The system may be factory equipped with a built-in non-fusible, lockable disconnect
switch. The built-in disconnect switch (Option BA6) requires copper wiring with ampac-
ity based on 75°C maximum temperature rating at the line side terminals.
If the system does not have a built-in disconnect switch, a field-provided or optional
shipped-separate, wall-mounted disconnect switch is required. It is recommended
that there is at least four feet (1.2M) of service room between the switch and system
access panels. All external wiring must be within approved conduit and have a mini-
mum temperature rise rating of 60°C. Run conduit so that it does not interfere with the
system access panels. See
FIGURE 3A or 3B on pages 7-8, for location of supply
wiring entrance. When providing or replacing fuses in a fusible disconnect, use dual
element time delay fuses and size according to the rating plate.
WARNING
To prevent injury or death due to electrocution or contact with
moving parts, lock disconnect switch open.
- REDB Unit Installation Manual RECB Unit Installation Manual RDDC Unit Installation Manual RDCC Unit Installation Manual RDDB Unit Installation Manual RDCB Unit Installation Manual RDC Unit Installation Manual RCC Unit Installation Manual RDB Unit Installation Manual RCB Unit Installation Manual REDC Unit Installation Manual MAPSIV Unit Installation Manual MAPSIII Unit Installation Manual