Rockwell Automation SA500 Drive Configuration and Programming User Manual
Page 2
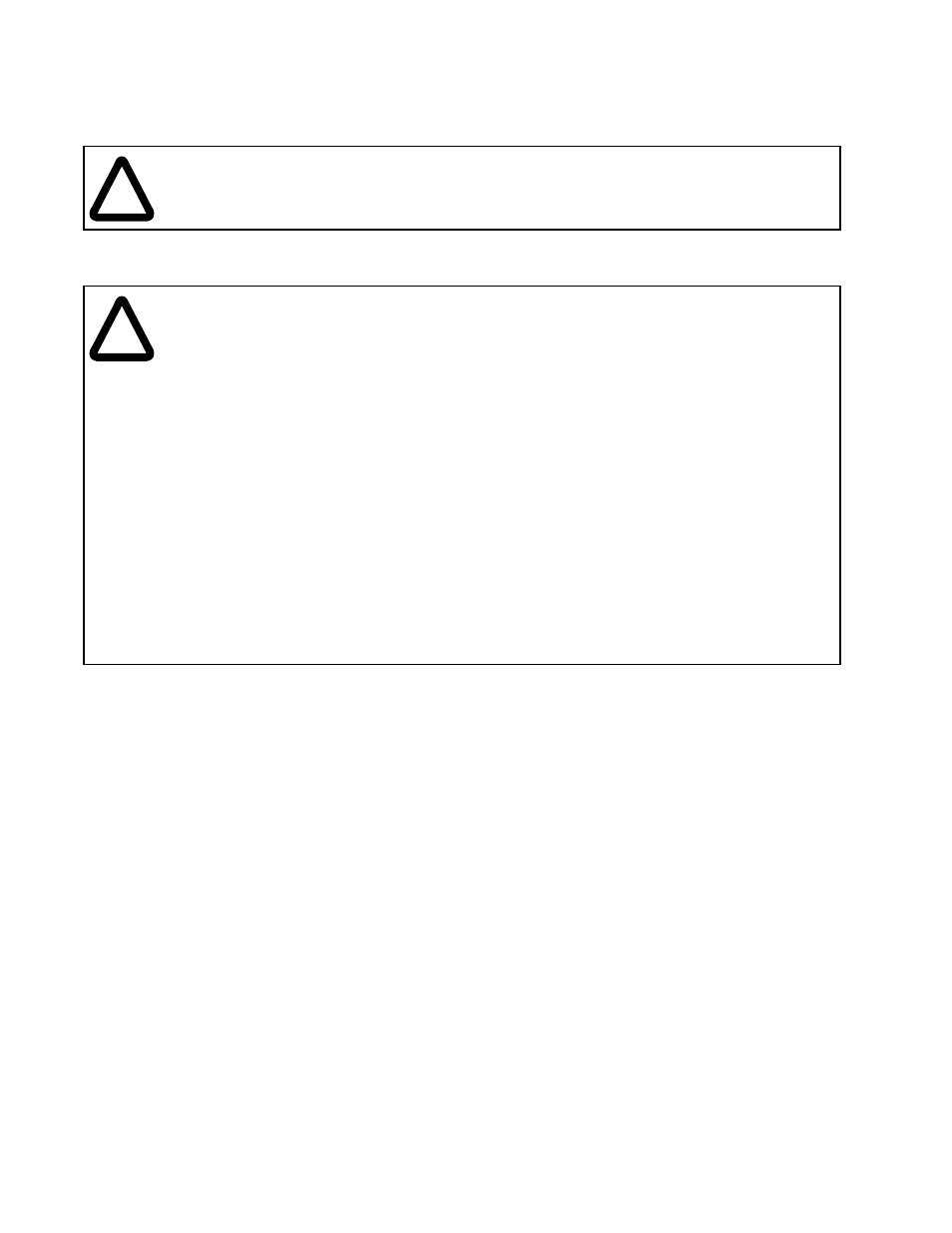
The information in this user’s manual is subject to change without notice.
Ethernet™ is a trademark of Xerox Corporation.
AutoMax™ is a trademark of Rockwell Automation.
©1998 Rockwell International Corporation
Throughout this manual, the following notes are used to alert you to safety considerations:
Important: Identifies information that is critical for successful application and understanding of the product.
!
ATTENTION: Identifies information about practices or circumstances that can lead to personal
injury or death, property damage, or economic loss.
!
ATTENTION: Only qualified electrical personnel familiar with the construction and operation of
this equipment and the hazards involved should install, adjust, operate, or service this equipment.
Read and understand this manual and other applicable manuals in their entirety before
proceeding. Failure to observe this precaution could result in severe bodily injury or loss of life.
ATTENTION: For brushless motor applications, changing any resolver wiring, breaking the
resolver coupling, replacing the resolver, or replacing the motor and resolver for any reason
requires that the shaft alignment test be performed again. Resolver wiring changes always affect
shaft alignment. A resolver change and/or a new motor/resolver combination will affect the shaft
alignment. Improper shaft alignment can cause motor overspeed when the motor is started. Failure
to observe this precaution could result in bodily injury.
ATTENTION: Registers and bits in the UDC module that are described as “read only” or for “system
use only” must not be written to by the user. Writing to these registers and bits may result in
improper system operation. Failure to observe this precaution could result in bodily injury.
ATTENTION: Electronic motor overload protection must be provided for each motor in an
AutoMax™ drive application to protect the motor against excessive heat caused by high currents.
This protection can be provided by either the THERMAL OVERLOAD software block or an external
hardware device. Applications in which a single power module is controlling multiple motors cannot
use the THERMAL OVERLOAD software block and must use an external hardware device or
devices to provide this protection. Failure to observe this precaution could result in damage to, or
destruction of, the equipment.