Rockwell Automation SA500 Drive Configuration and Programming User Manual
Page 109
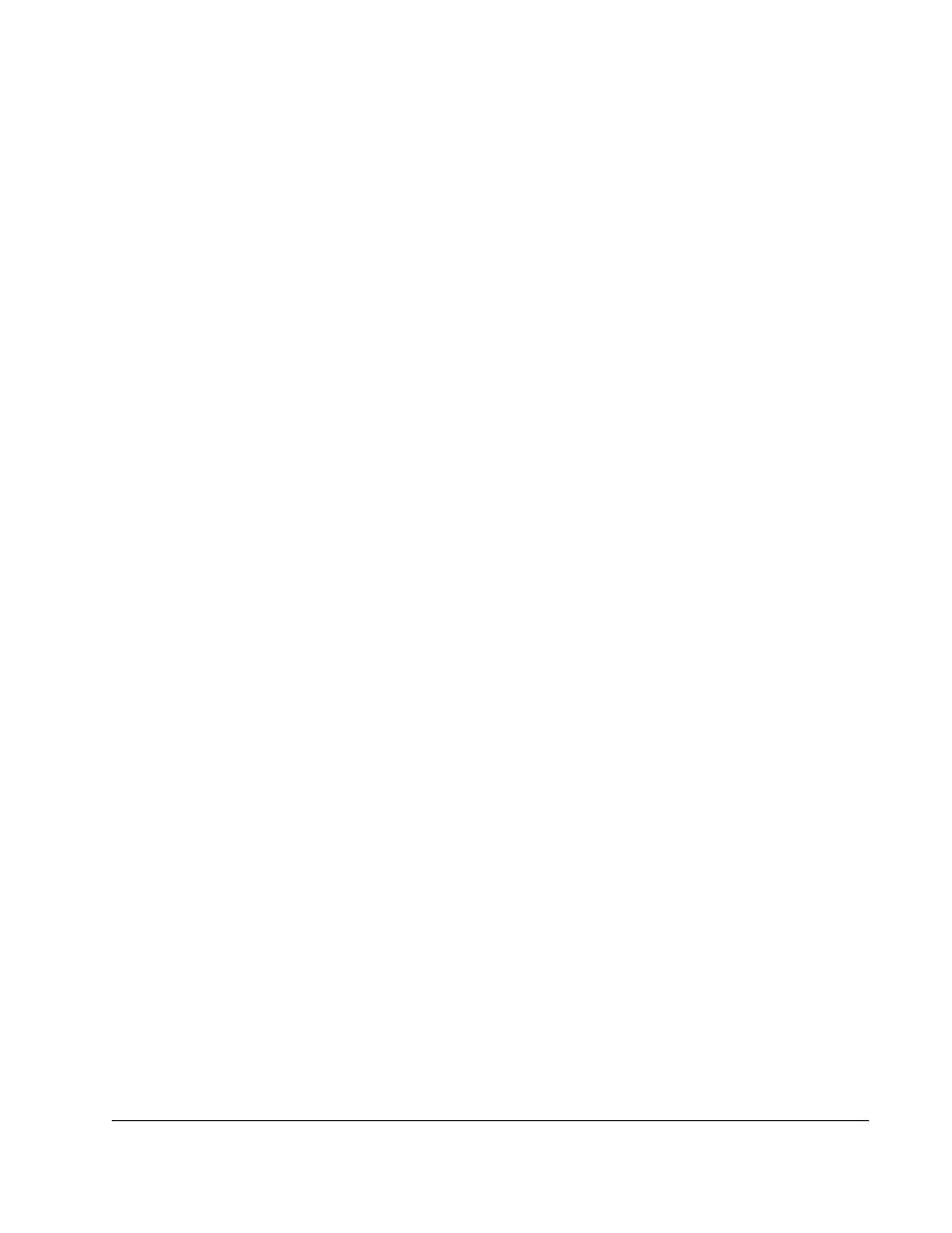
SA500 Control Algorithms
C-3
Input position reference values are received from UDC tasks. These position
reference values are then converted into position data which is scaled and compared
with position feedback values to calculate the amount of position error (POS_ERR%,
register 218/1218). The source of position feedback is selectable: resolver, analog, or
register. Register feedback position data is sent from the UDC module through
SPD_REF% (register 107/1107)
The position error is then fed into a PI block where its output value is added to a
feedforward value to provide a velocity output (POS_REG_OUT%, register 209/1209)
for the speed loop. PI block gain values can be adjusted through the crossover
frequency (WCOP%, register 160/1160) and the damping factor (ZETAP%, register
161/1161).
Position loop velocity output values are limited by the variables limit plus (POS_LP%,
register 164/1164) and limit minus (POS_LM%, register 165/1165). If the positive limit
is reached, TRQ_SP@ (bit 4 of register 200/1200) is set. If the negative limit is
reached, TRQ_SM@ (bit 5 of register 200/1200) is set. The integral value in the PI
block is clamped whenever the positive or negative limits are reached.
See the block diagrams that follow for further information.