Shielding, Electrical installation – Lenze i700 Manual User Manual
Page 91
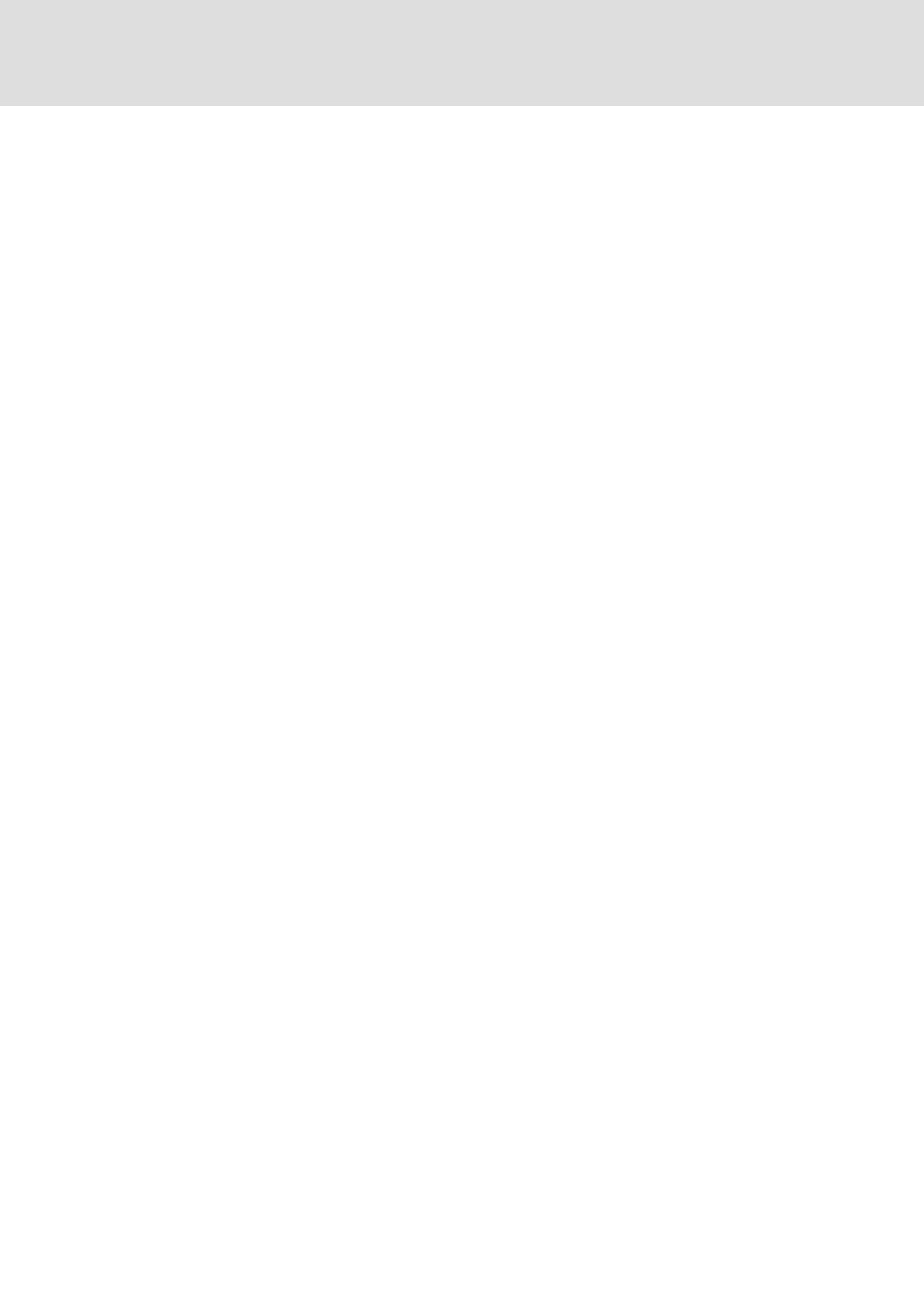
Electrical installation
Installation according to EMC (installation of a CE−typical drive system)
Shielding
l
91
EDS700ACBA EN 4.0
6.3
Installation according to EMC (installation of a CE−typical drive system)
Design of the cables
ƒ
It is imperative to comply with the regulations concerning minimum cross−sections
of PE conductors. The cross−section of the PE conductor must be at least as large as
the cross−section of the power connections.
ƒ
The cables used must comply with the approvals required for the location (e.g. UL).
6.3.1
Shielding
Requirements
ƒ
The effectiveness of a shielded cable is reached by:
– Providing a good shield connection through large−surface shield contact.
– Using only braided shields with low shield resistance made of tin−plated or
nickel−plated copper braid.
– Using braided shields with an overlap rate > 70 % and an overlap angle of 90 °.
– Keeping unshielded cable ends as short as possible.
Use system cables or shielded cables for these connections:
ƒ
Motor
ƒ
Feedback systems
ƒ
Motor holding brake (shielding is required when being integrated into the motor
cable; connection to optional motor brake control)
The following connections need not be shielded:
ƒ
24 V supply
ƒ
Digital signals (inputs and outputs)
Connection system
ƒ
Connect the shield with a large surface and fix it with metal cable binders or a
conductive clamp.
ƒ
Connect the shield directly to the corresponding device shield sheet.
– If required, additionally connect the shield to the conductive and earthed
mounting plate in the control cabinet.
– If required, additionally connect the shield to the cable clamp rail.