Mounting in "cold plate" technique, Mechanical installation – Lenze i700 Manual User Manual
Page 69
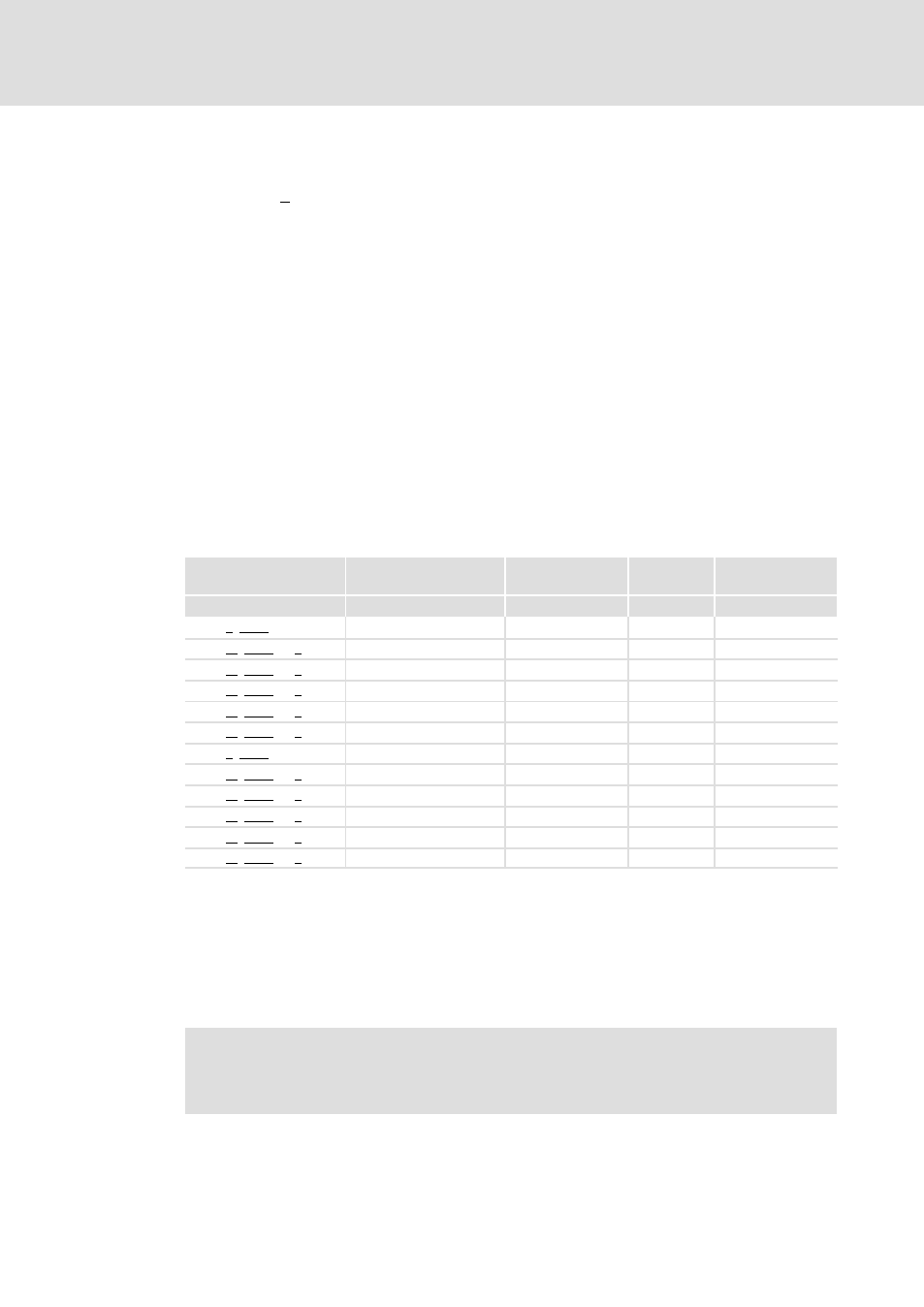
Mechanical installation
Dimensions
Mounting in "cold plate" technique
l
69
EDS700ACBA EN 4.0
5.3.4
Mounting in "cold plate" technique
The E70ACxSCxxx4x... devices are designed for assembly on coolers (e.g. collective coolers)
in "cold−plate" technique.
Requirements for collective coolers
A good thermal connection to the cooler is important for the trouble−free operation of
the controller:
ƒ
The contact area between the collective cooler and the controller
– must be at least as big as the cooling plate of the controller.
– must be smooth, the maximum deviation must not exceed 0.05 mm.
ƒ
The controller has to be connected to the collective cooler with all required screwed
joints.
ƒ
The thermal resistance R
th
must be observed, see table.
The values in the table apply to the operation of the controllers under rated
conditions.
The values already include the heat transmission between the cooler and the device
with a standard heat conducting paste at a film thickness of approx. 50
mm.
Power loss
Thermal resistance
T
max
Power loss
(control cabinet)
Type
P
V1
[W]
R
th
[K/W]
[°C]
P
V2
[W]
E70ACPSC0304x
45
£ 1.00
85
15
E70ACMSC0054xx1xxx
25
£ 1.80
85
25
E70ACMSC0104xx1xxx
50
£ 0.90
85
30
E70ACMSC0204xx1xxx
95
£ 0.45
85
35
E70ACMSC0054xx2xxx
50
£ 0.90
85
40
E70ACMSC0104xx2xxx
95
£ 0.45
85
55
E70ACPSC0604x
85
£ 0.35
70
25
E70ACMSC0324xx1xxx
140
£ 0.25
75
70
E70ACMSC0484xx1xxx
215
£ 0.16
75
85
E70ACMSC0644xx1xxx
290
£ 0.12
75
100
E70ACMSC0204xx2xxx
185
£ 0.20
75
75
E70ACMSC0324xx2xxx
275
£ 0.12
75
105
Tab. 5−1
Cold plate
P
V1
separated power loss, to be dissipated via heatsink
P
V2
Power loss remaining in the control cabinet
Ambient conditions
ƒ
The rated data and the derating factors at increased temperature also apply to the
ambient temperature of the drive controllers.
)
Note!
Apply standard heat−conducting paste or heat−conducting foil onto cooler and
cooling plate before you bolt the controller onto the cooler.