Face milling (cycle 232) – HEIDENHAIN TNC 320 (340 551-01) User Manual
Page 273
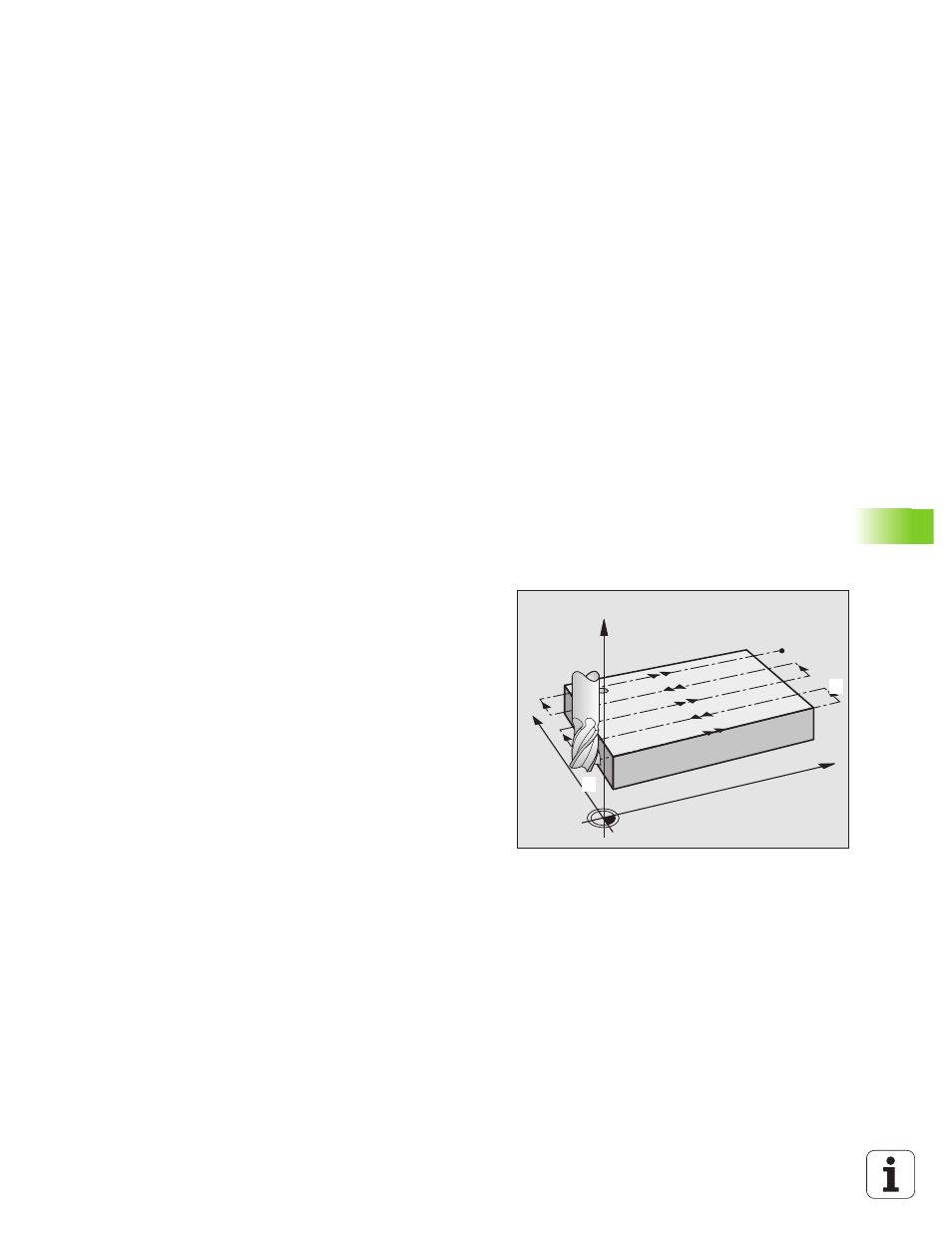
HEIDENHAIN TNC 320
273
8.6 Cy
cles f
o
r Multipass Milling
FACE MILLING (Cycle 232)
Cycle 232 is used to face mill a level surface in multiple infeeds while
taking the finishing allowance into account. Three machining
strategies are available:
Strategy Q389=0: Meander machining, stepover outside the
surface being machined
Strategy Q389=1: Meander machining, stepover within the surface
being machined
Strategy Q389=2: Line-by-line machining, retraction and stepover
at the positioning feed rate
1
From the current position, the TNC positions the tool at rapid
traverse (FMAX) to the starting position using positioning logic
1
.
If the current position in the spindle axis is greater than the 2nd set-
up clearance, the control positions the tool first in the machining
plane and then in the spindle axis. Otherwise it first moves to the
2nd set-up clearance and then in the machining plane. The starting
point in the machining plane is offset from the edge of the
workpiece by the tool radius and the safety clearance to the side.
2
The tool then moves in the spindle axis at the positioning feed rate
to the first plunging depth calculated by the control.
Strategy Q389=0
3
The tool then advances to the stopping point
2
at the feed rate for
milling. The end point lies outside the surface. The control
calculates the end point from the programmed starting point, the
programmed length, the programmed safety clearance to the side
and the tool radius.
4
The TNC offsets the tool to the starting point in the next pass at
the pre-positioning feed rate. The offset is calculated from the
programmed width, the tool radius and the maximum path overlap
factor.
5
The tool then moves back in the direction of the starting point
1
.
6
The process is repeated until the programmed surface has been
completed. At the end of the last pass, the next machining depth
is plunged to.
7
In order to avoid non-productive motions, the surface is then
machined in reverse direction.
8
The process is repeated until all infeeds have been machined. In
the last infeed, simply the finishing allowance entered is milled at
the finishing feed rate.
9
At the end of the cycle, the tool is retracted at FMAX to the 2nd
set-up clearance.
X
Y
Z
1
1
1
2