HEIDENHAIN TNC 320 (340 551-01) User Manual
Page 239
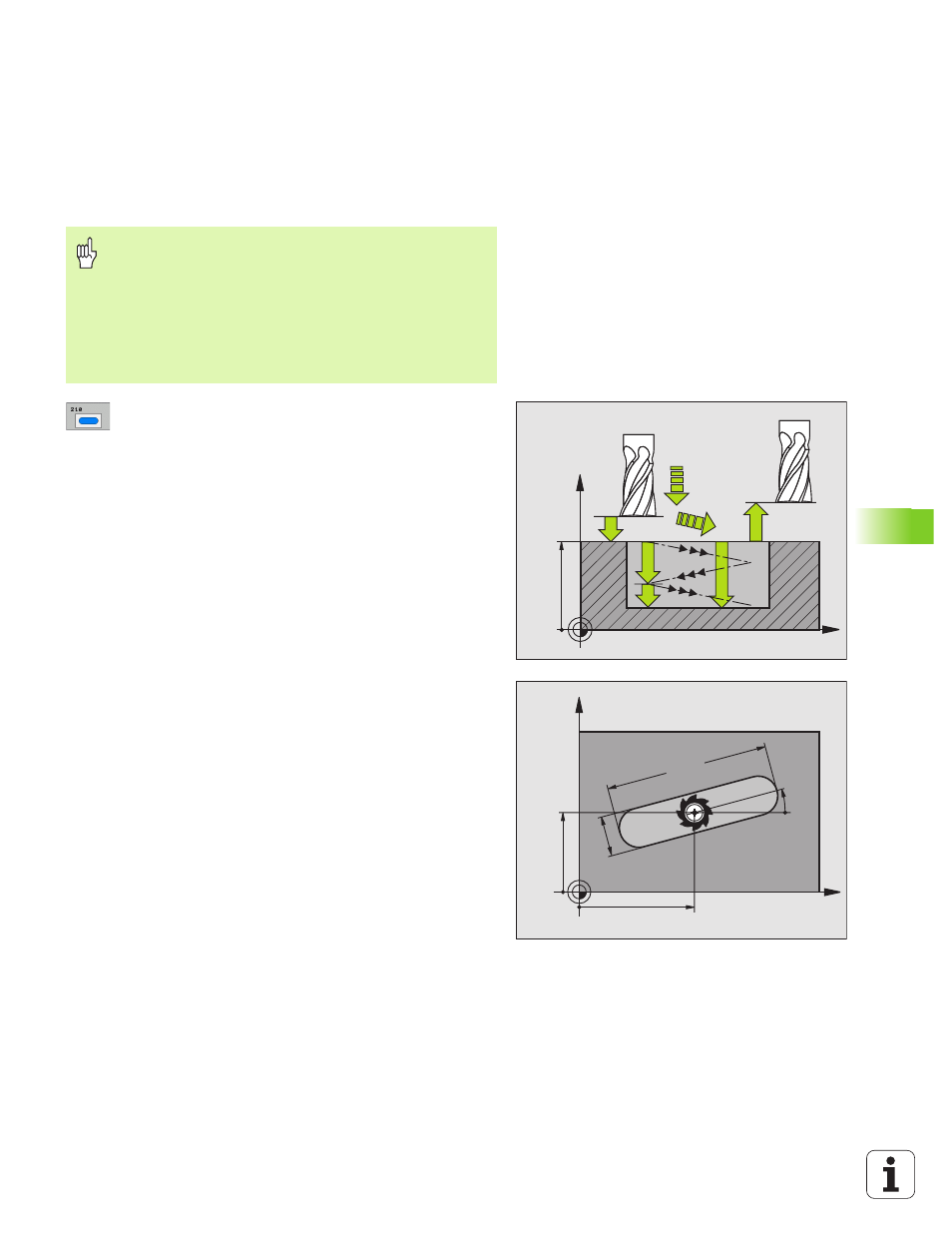
HEIDENHAIN TNC 320
239
8.3 Cy
cles f
o
r Milling P
o
c
k
ets, St
uds and Slots
8
Set-up clearance
Q200 (incremental value): Distance
between tool tip and workpiece surface.
8
Depth
Q201 (incremental value): Distance between
workpiece surface and bottom of slot.
8
Feed rate for milling
Q207: Traversing speed of the
tool in mm/min while milling.
8
Plunging depth
Q202 (incremental value): Total
extent by which the tool is fed in the tool axis during
a reciprocating movement.
8
Machining operation (0/1/2)
Q215: Define the
machining operation:
0: Roughing and finishing
1: Only roughing
2: Only finishing
8
Workpiece surface coordinate
Q203 (absolute
value): Coordinate of the workpiece surface.
8
2nd set-up clearance
Q204 (incremental value):
Z coordinate at which no collision between tool and
workpiece (clamping devices) can occur.
8
Center in 1st axis
Q216 (absolute value): Center of
the slot in the reference axis of the working plane.
8
Center in 2nd axis
Q217 (absolute value): Center of
the slot in the minor axis of the working plane.
8
First side length
Q218 (value parallel to the
reference axis of the working plane): Enter the length
of the slot.
8
Second side length
Q219 (value parallel to the
secondary axis of the working plane): Enter the slot
width. If you enter a slot width that equals the tool
diameter, the TNC will carry out the roughing process
only (slot milling).
Danger of collision!
Use the machine parameter suppressDepthErr to define
whether, if a positive depth is entered, the TNC should
output an error message (on) or not (off).
Keep in mind that the TNC reverses the calculation for pre-
positioning when a positive depth is entered. This
means that the tool moves at rapid traverse in the tool axis
at safety clearance below the workpiece surface!
X
Z
Q200
Q201
Q207
Q202
Q203
Q204
X
Y
Q219
Q218
Q217
Q216
Q224