Back boring (cycle 204) – HEIDENHAIN TNC 320 (340 551-01) User Manual
Page 190
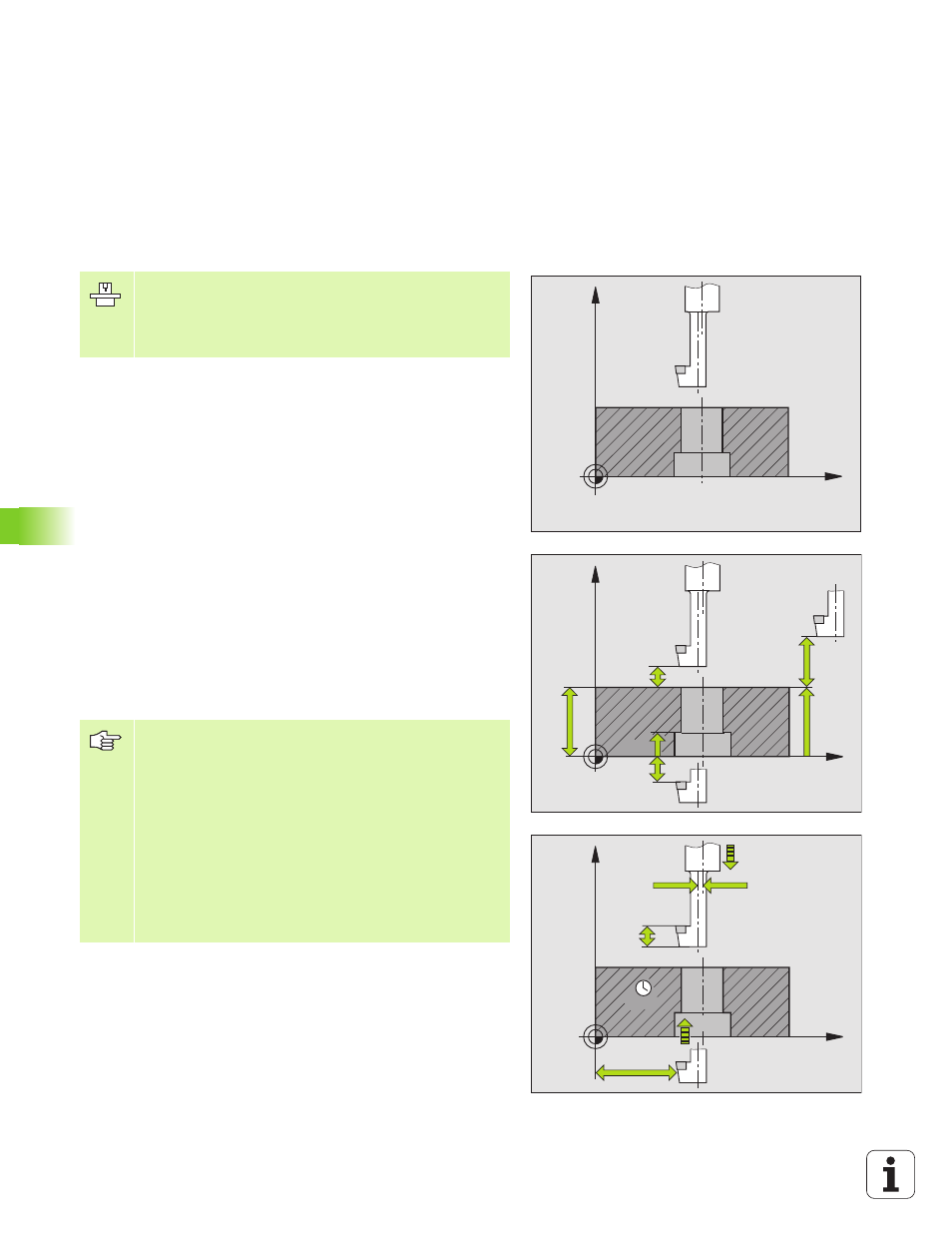
190
8 Programming: Cycles
8.2 Cy
cles f
o
r Dr
illing,
T
apping and Thr
ead Milling
BACK BORING (Cycle 204)
This cycle allows holes to be bored from the underside of the
workpiece.
1
The TNC positions the tool in the tool axis at rapid traverse FMAX
to the set-up clearance above the workpiece surface.
2
The TNC then orients the spindle to the 0° position with an
oriented spindle stop, and displaces the tool by the off-center
distance.
3
The tool is then plunged into the already bored hole at the feed rate
for pre-positioning until the tooth has reached the set-up clearance
on the underside of the workpiece.
4
The TNC then centers the tool again over the bore hole, switches
on the spindle and the coolant and moves at the feed rate for
boring to the depth of bore.
5
If a dwell time is entered, the tool will pause at the top of the bore
hole and will then be retracted from the hole again. Another
oriented spindle stop is carried out and the tool is once again
displaced by the off-center distance.
6
The TNC moves the tool at the pre-positioning feed rate to the set-
up clearance and then, if entered, to the 2nd set-up clearance at
FMAX.
X
Z
X
Z
Q250
Q203
Q204
Q249
Q200
Q200
X
Z
Q255
Q254
Q214
Q252
Q253
Q251
Machine and control must be specially prepared by the
machine tool builder for use of this cycle.
Special boring bars for upward cutting are required for this
cycle.
Before programming, note the following:
Program a positioning block for the starting point (hole
center) in the working plane with radius compensation R0.
The algebraic sign for the cycle parameter depth
determines the working direction. Note: A positive sign
bores in the direction of the positive spindle axis.
The entered tool length is the total length to the underside
of the boring bar and not just to the tooth.
When calculating the starting point for boring, the TNC
considers the tooth length of the boring bar and the
thickness of the material.