Ruled surface (cycle 231) – HEIDENHAIN TNC 320 (340 551-01) User Manual
Page 270
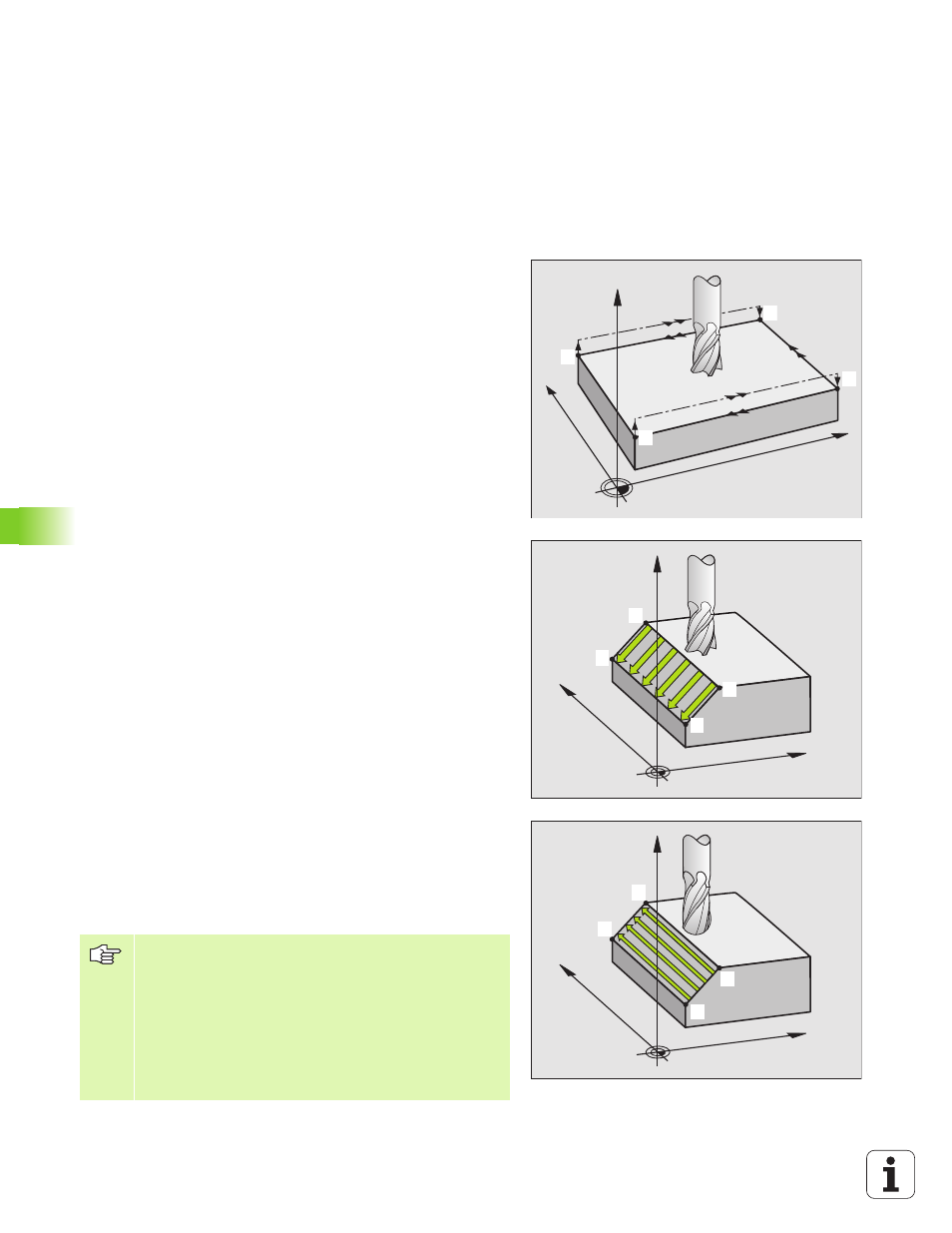
270
8 Programming: Cycles
8.6 Cy
cles f
o
r Multipass Milling
RULED SURFACE (Cycle 231)
1
From the current position, the TNC positions the tool in a linear 3-D
movement to the starting point
1
.
2
The tool subsequently advances to the stopping point
2
at the feed
rate for milling.
3
From this point, the tool moves at rapid traverse FMAX by the tool
diameter in the positive tool axis direction, and then back to
starting point
1
.
4
At the starting point
1
the TNC moves the tool back to the last
traversed Z value.
5
Then the TNC moves the tool in all three axes from point
1
in the
direction of point
4
to the next line.
6
From this point, the tool moves to the stopping point on this pass.
The TNC calculates the end point from point
2
and a movement in
the direction of point
3
.
7
Multipass milling is repeated until the programmed surface has
been completed.
8
At the end of the cycle, the tool is positioned above the highest
programmed point in the tool axis, offset by the tool diameter.
Cutting motion
The starting point, and therefore the milling direction, is selectable
because the TNC always moves from point
1
to point
2
and in the total
movement from point
1
/
2
to point
3
/
4
. You can program point
1
at
any corner of the surface to be machined.
If you are using an end mill for the machining operation, you can
optimize the surface finish in the following ways:
A shaping cut (spindle axis coordinate of point
1
greater than
spindle-axis coordinate of point
2
) for slightly inclined surfaces.
A drawing cut (spindle axis coordinate of point
1
smaller than
spindle-axis coordinate of point
2
) for steep surfaces.
When milling twisted surfaces, program the main cutting direction
(from point
1
to point
2
) parallel to the direction of the steeper
inclination.
If you are using a spherical cutter for the machining operation, you can
optimize the surface finish in the following way:
When milling twisted surfaces, program the main cutting direction
(from point
1
to point
2
) perpendicular to the direction of the
steepest inclination.
X
Y
Z
1
1
1
4
1
3
1
2
X
Y
Z
1
1
1
2
1
3
1
4
X
Y
Z
1
1
1
4
1
2
1
3
Before programming, note the following:
The TNC positions the tool from the current position
in a linear 3-D movement to the starting point
1
. Pre-
position the tool in such a way that no collision between
tool and clamping devices can occur.
The TNC moves the tool with radius compensation R0 to
the programmed positions.
If required, use a center-cut end mill (ISO 1641).