Common cutting faults -47, Common cutting faults – Hypertherm HPR260 Manual Gas Preventive Maintenance Program Rev.5 User Manual
Page 141
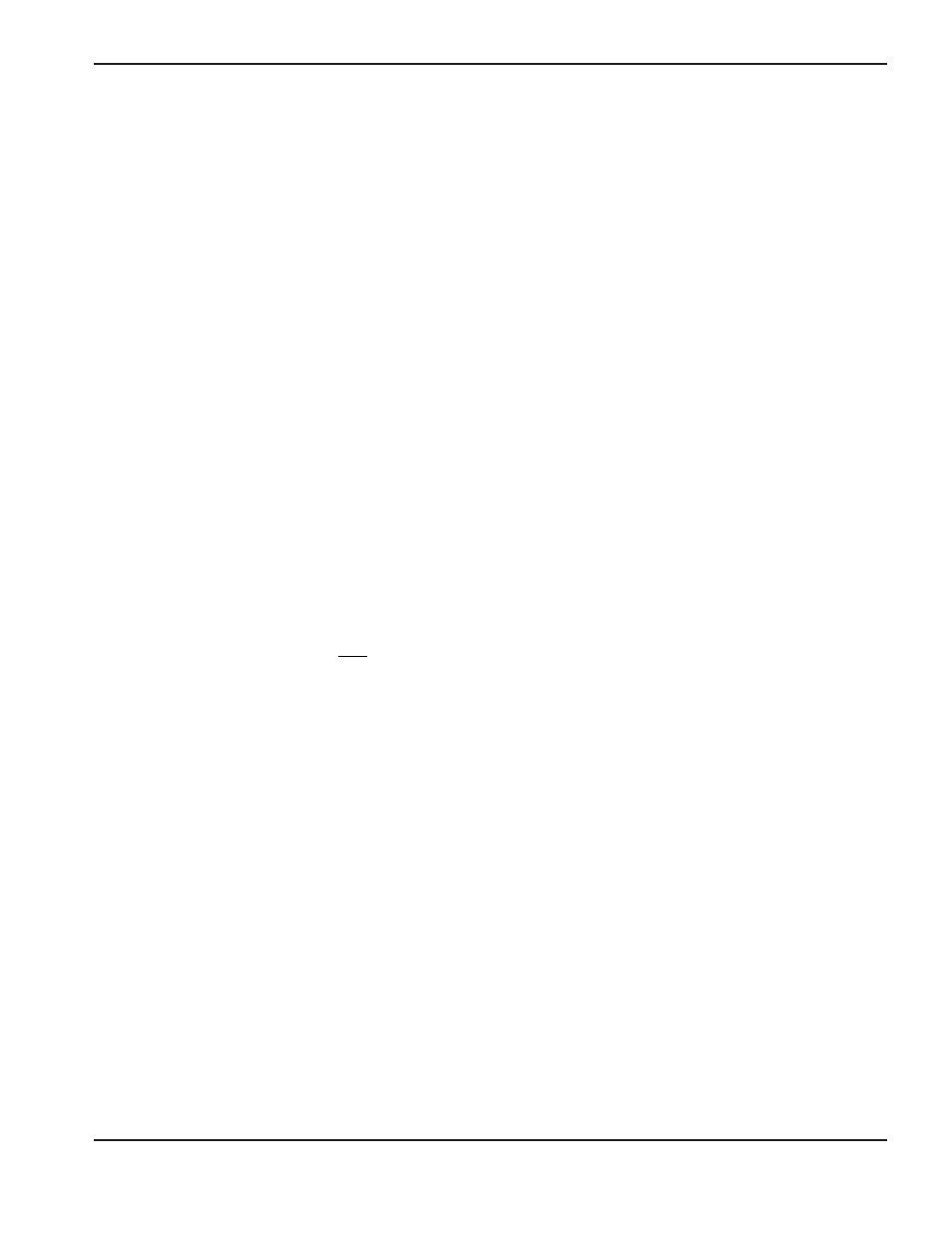
OPERATION
HPR260 Auto Gas
Instruction Manual
4-47
Common cutting faults
•
Torch pilot arc will initiate, but will not transfer. Causes can be:
1.
Work cable connection on the cutting table is not making good contact.
2.
Malfunction in the system. See Section 5.
.
3.
Torch-to-work distance is too high.
•
The workpiece is not totally penetrated, and there is excessive sparking on top of the workpiece.
Causes can be:
1.
Current is set too low (check Cut chart information).
2.
Cut speed is too high (check Cut chart information).
3.
Torch parts are worn (see Changing consumable parts).
4.
Metal being cut is too thick.
•
Dross forms on the bottom of the cut. Causes can be:
1.
Cutting speed is not correct (check Cut chart information).
2.
Arc current is set too low (check Cut chart information).
3.
Torch parts are worn (see Changing consumable parts).
•
Cut angle is not square. Causes can be:
1.
Wrong direction of machine travel.
High-quality side is on the right with respect to the forward motion of the torch.
2.
Torch-to-work distance is not correct (check Cut chart information).
3.
Cutting speed is not correct (check Cut chart information).
4.
Arc current is not correct (check Cut chart information).
5.
Damaged consumable parts (see Changing consumable parts ).
•
Short consumable life. Causes can be:
1.
Arc current, arc voltage, travel speed, motion delay, gas flow rates, or initial torch height not set as specified
in the Cut charts.
2.
Attempting to cut highly magnetic metal plate, such as armor plate with a high nickel content, will shorten
consumable life. Long consumable life is difficult to achieve when cutting plate that is magnetized or
becomes magnetized easily.
3. Beginning or ending the cut off the plate surface. To achieve consumable long life, all cuts must begin
and end on the plate surface
.