Payload inertia vs. acceleration, 7 robot mounting frame, quattro s650h robot – Adept s650HS Quattro User Manual
Page 124
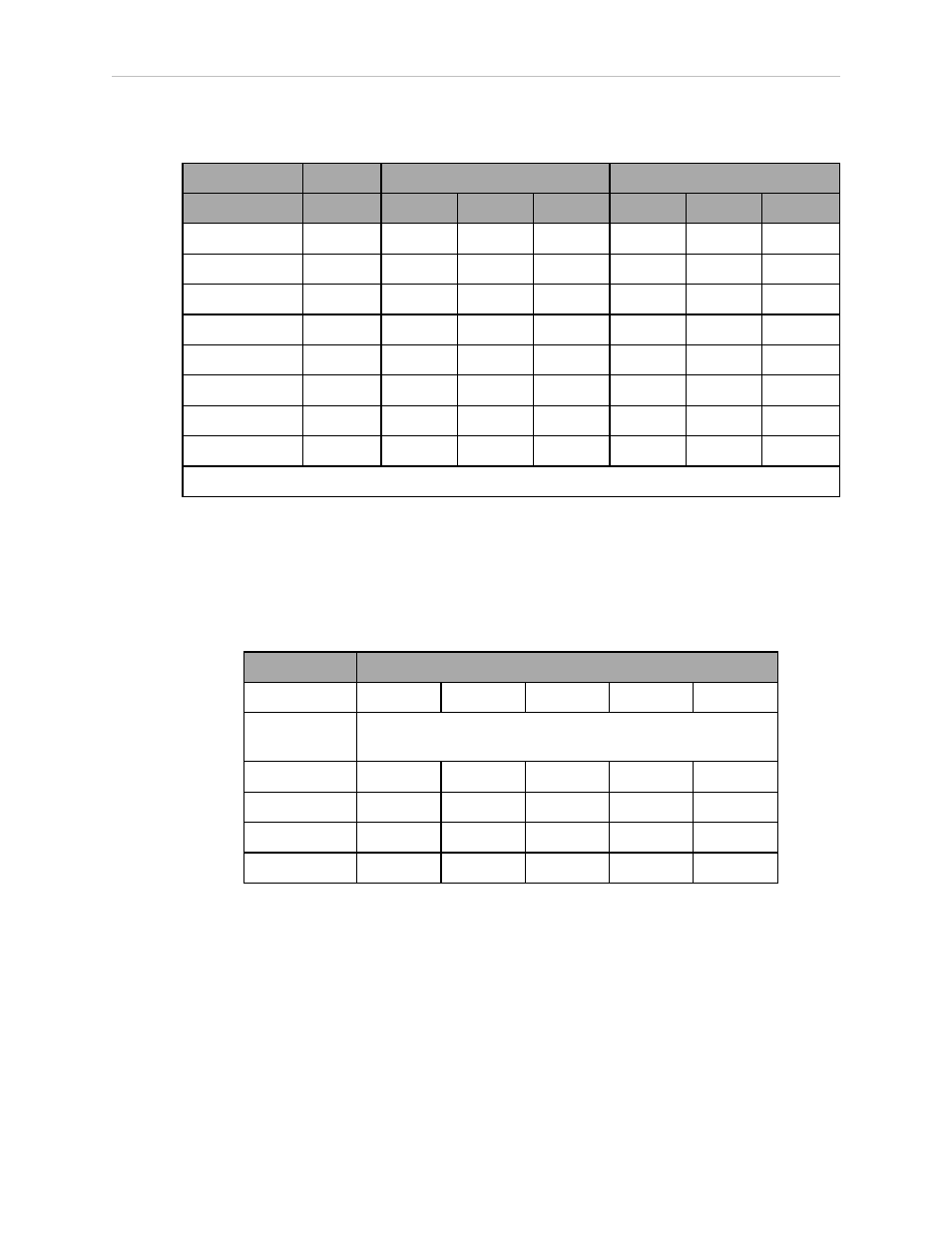
Chapter 7: Technical Specifications
Table 7-9. Payload Mass vs. Acceleration - s800 Quattro
Platform
Payload
Maximum Acceleration
Preferred Acceleration
Type
kg
%
a
m/s
2
g
%
a
m/s
2
g
P30
10.0
90
17.6
1.8
45
8.8
0.9
P30
8.0
120
23.5
2.4
60
11.8
1.2
P30
6.0
200
39.2
4.0
80
15.7
1.6
ALL
4.0
300
58.8
6.0
120
23.5
2.4
ALL
2.0
560
109.8
11.2
240
47.0
4.8
ALL
1.5
580
113.7
11.6
320
62.7
6.4
ALL
1.0
600
117.6
12.0
320
62.7
6.4
ALL
0.1
612
120.0
12.2
320
62.7
6.4
a
% is the V+ Accel/Decel setting, which, for the Quattro, can be set as high as 1000%.
Payload Inertia vs. Acceleration
The following table provides a general guideline based on typical high-performance use. The
practical inertia for any application will vary depending on the performance requirements.
Table 7-10. Payload Inertia vs. Acceleration
Platform
60 deg.
185 deg.
P31
P32
P34
Acceleration
Value
Allowable Tool Inertia (kg-cm
2
)
100
672
75
750
188
47
250
269
30
300
75
19
500
134
15
150
37
9
750
90
10
100
25
6
NOTE: The P30 platform is not listed in this table because this platform does not
rotate. Payloads for the P30 platform should be designed with their center-of-mass
in line with the center axis of the tool flange. This will minimize induced torque
during XYZ motions.
7.7 Robot Mounting Frame, Quattro s650H Robot
NOTE: The example frame provided here was not designed to meet USDA
standards. While most mechanical specifications are the same, you will have to
Adept Quattro User's Guide, Rev F
Page 124 of 196