Adept s650HS Quattro User Manual
Page 100
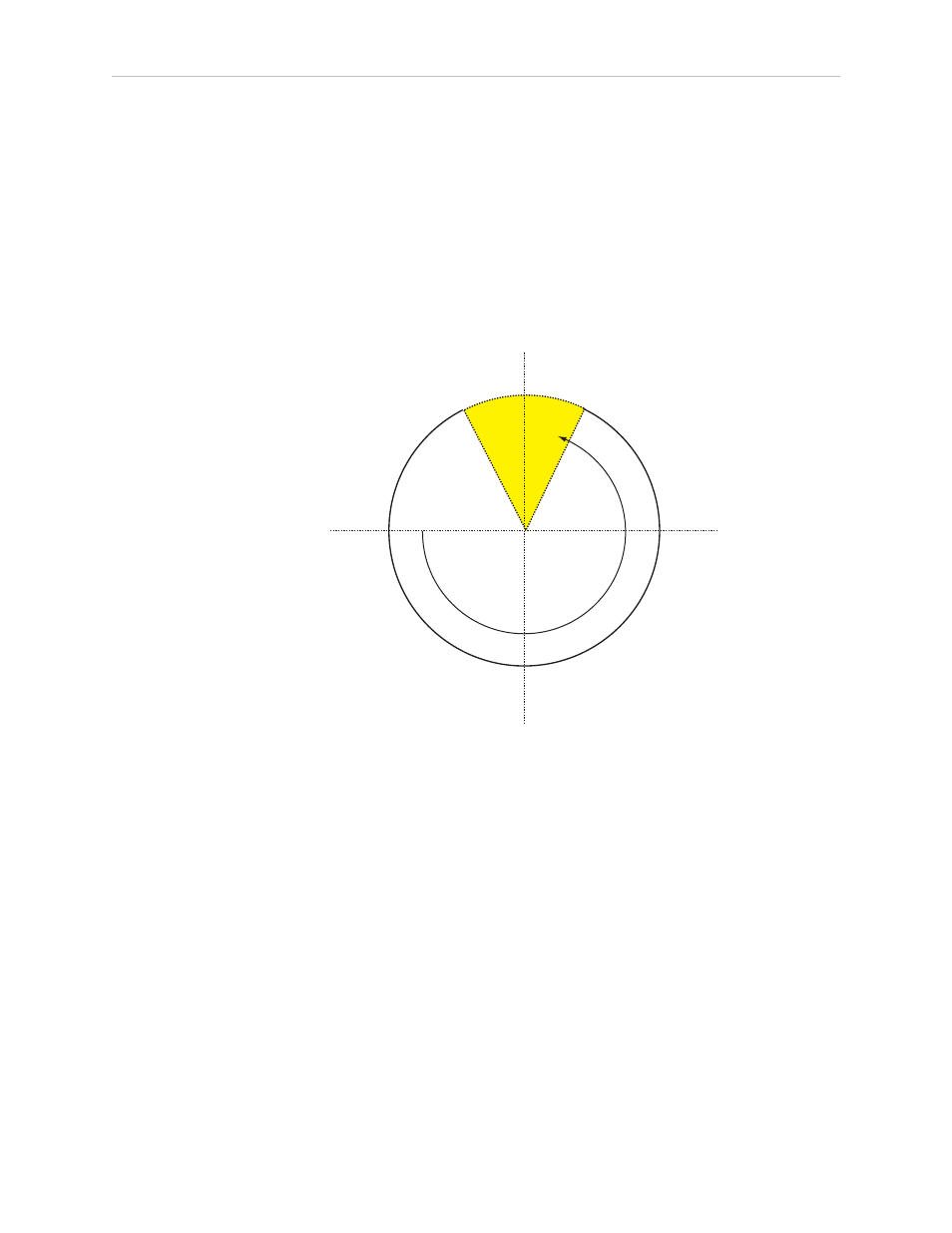
Chapter 5: System Operation
The roll value of location A is -90 degrees and the roll value for location B is 2 degrees. One
way to think of this motion is that the tool flange will not “cross over” the zero-roll position as
the robot moves from location A to location B when SINGLE is asserted. This type of motion
can prevent the end-effector air lines from being stretched, and ensures that a part is always
accessed from the same direction. This motion can also be used to position the tool flange in
preparation for the next motion.
NOTE: When SINGLE is asserted, the tool flange will always rotate in the direction
that does not cross the zero-roll position, even if that means a very large rotation.
roll = -90
roll = +90
(A)
(B)
-180 +180
(B) Roll = 2 degrees
(A) Roll = -90 degrees
0
Figure 5-7. Motion with SINGLE Asserted
MULTIPLE Program Instruction
In Figure 5-8, the arrow indicates the clockwise rotation that the tool flange will take as the
robot moves from location A to location B with the program instruction MULTIPLE asserted.
That is, when the following code is executed:
MOVE A
BREAK
MULTIPLE
MOVE B
As in Figure 5-7, the roll value of location A is -90 degrees and the roll value for location B is 2
degrees. With MULTIPLE asserted, however, the tool flange will “cross over” the zero-roll
position as the robot moves from location A to location B.
NOTE: MULTIPLE always is automatically asserted every time program execution
is initiated with an EXECUTE command or instruction.
Adept Quattro User's Guide, Rev F
Page 100 of 196