10 system connections, 2 communication with the safety system – Pilz PSENvip RL D P User Manual
Page 125
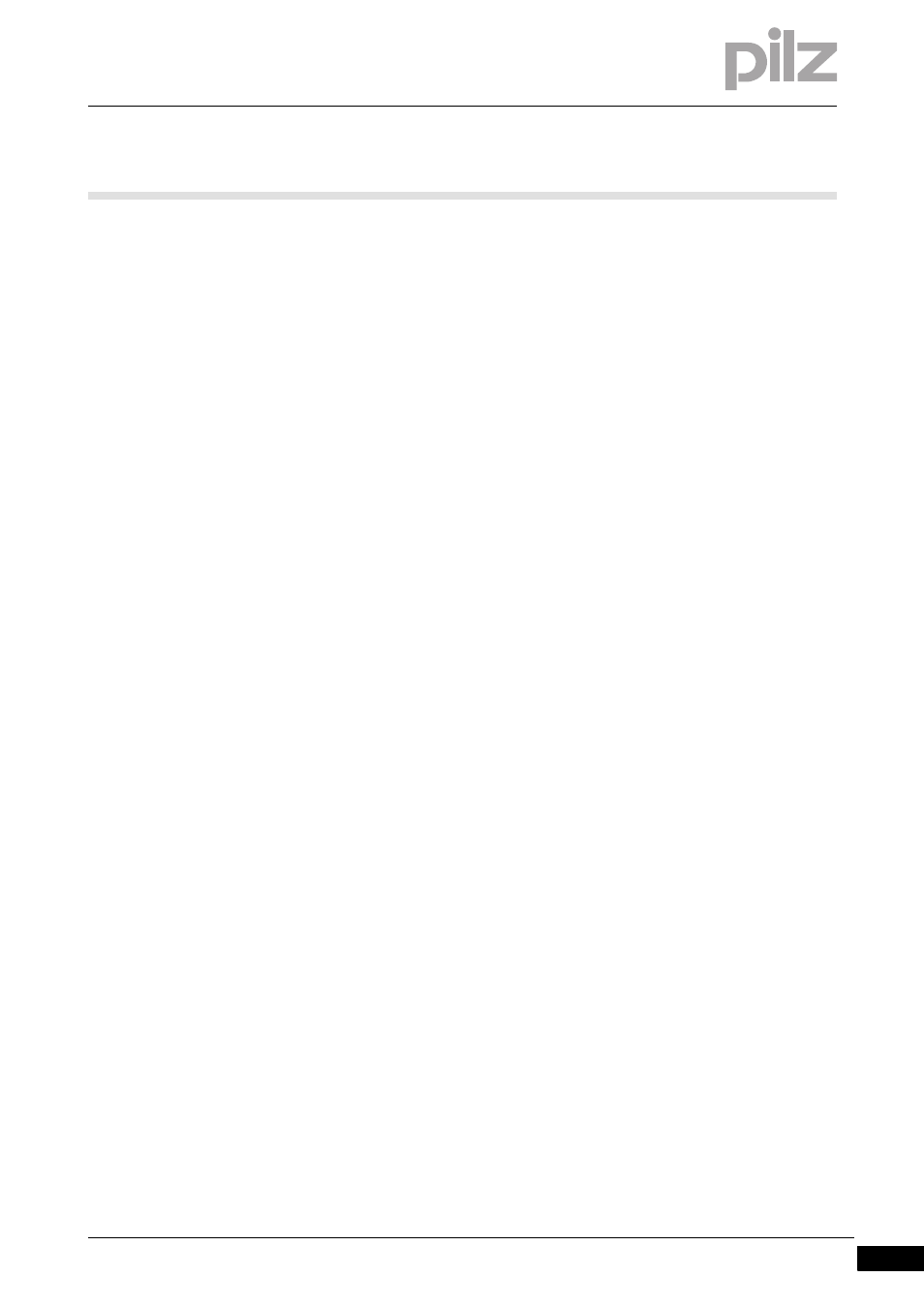
Pilz GmbH & Co. KG, Felix-Wankel-Straße 2, 73760 Ostfildern, Germany
Telephone: +49 711 3409-0, Telefax: +49 711 3409-133, E-Mail: [email protected]
10-3
10.2
Communication with the safety system
10
System Connections
Tool class 2
The user program confirms tool class 2. The PSENvip switches to a
RUN state.
The PSENvip switches to a HOLD state if
– No communication is established (within 30 s on power-up, other-
wise within 200 ms).
– The tool class sent by the PSENvip and reflected by the user pro-
gram do not match.
– Errors occur in the communications protocol.
– Overall communication takes longer than 600 ms.
– A single communication phase takes longer than 200 ms (see
Chapter 4-4, section entitled "Communication sequence").
The switchover point must be raised in comparison with the regular
switchover point. The switchover to lower speed must take place ear-
lier.
The user program must convey a higher switchover point to the CNC
controller and then monitor this.
Tool class 3
The user program confirms tool class 3. The PSENvip switches to a
RUN state.
The PSENvip switches to a HOLD state if
– No communication is established (within 30 s on power-up, other-
wise within 200 ms).
– The tool class sent by the PSENvip and reflected by the user pro-
gram do not match.
– Errors occur in the communications protocol.
– Overall communication takes longer than 600 ms.
– A single communication phase takes longer than 200 ms (see
Chapter 4-4, section entitled "Communication sequence").
The switchover point must be raised in comparison with the switcho-
ver point for tool class 3. The switchover to lower speed must take
place even earlier.
The user program must convey a higher switchover point to the CNC
controller and then monitor this.
If the press is at top dead centre (TDC), each press stroke must be
acknowledged before it is initiated. Only after this acknowledgement
are the OSSDs switched on, enabling rapid traverse for the press.
Systemanbindung_PSS4000_Beispiel_Einl