Rockwell Automation WebPak 3000 DC Drive Application Workbook Version 1.1 User Manual
Page 84
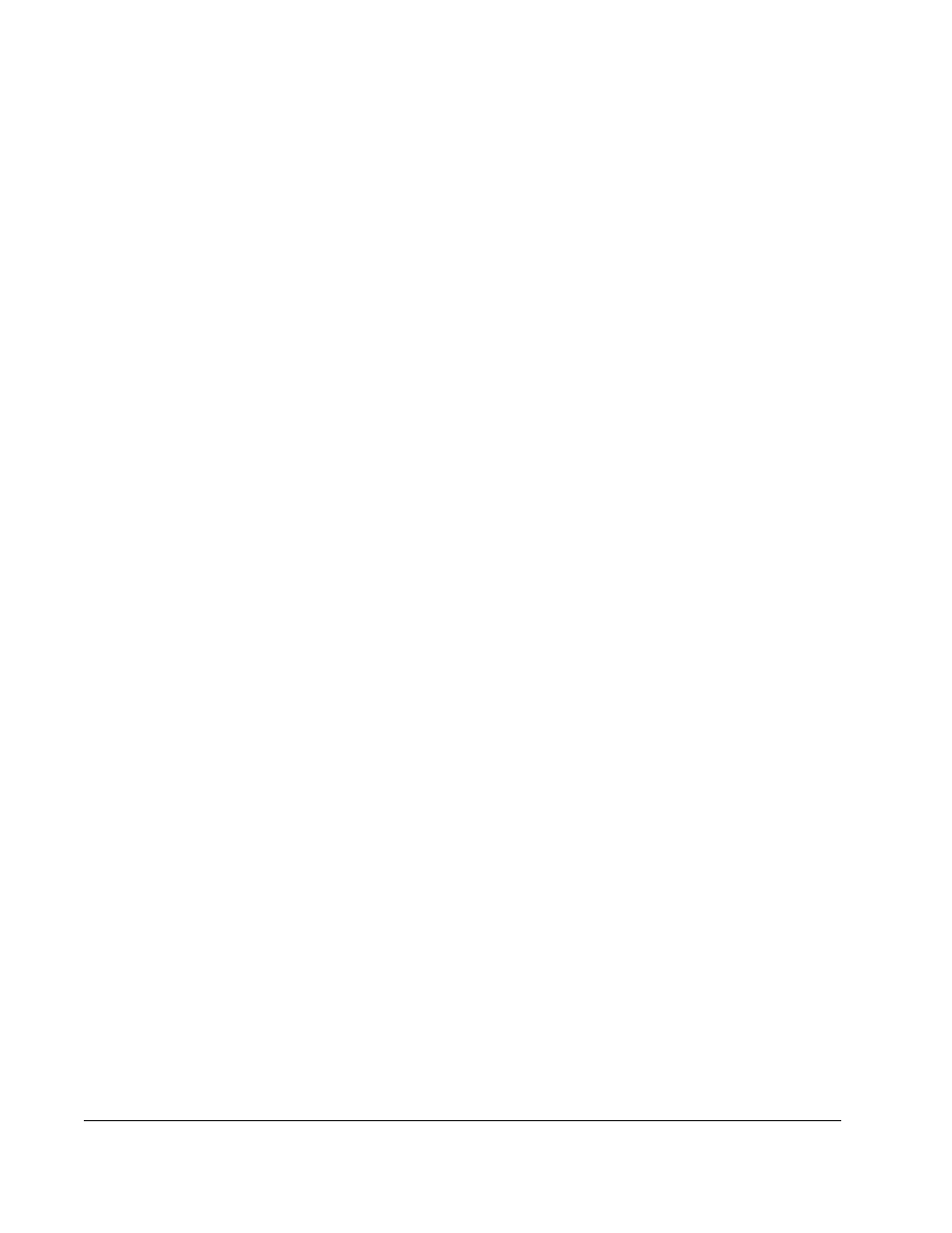
A-6
WebPak 3000 Drive Application Workbook, Version 1.1
A.2.5 Voltage and Field Control
A DC drive that can operate in both the constant torque and constant horsepower
range of its associated DC motor can provide performance and economic advantages
over a voltage-only drive.
Once the motor shaft torque requirements of a driven load have been determined, the
motor design parameters are based on the mechanical requirements of the load and
the performance requirements of the application.
Driven load profiles that exhibit a need for high torque at low speeds and less torque
at higher speeds are usually optimized in both cost and performance by using a drive
with both armature voltage and field voltage control capabilities. Extruders and center
driven unwinds and winders are prime examples of this type of load profile.
The physical size (frame size) of a motor is directly related to the maximum shaft
torque it must deliver. The base speed at which the torque is developed determines
the motor nameplate horsepower.
For example, a 10 HP 500/2000 RPM motor will deliver approximately the same
maximum relative shaft torque as a 40 HP 1750 RPM. Both designs will use the same
frame size and cost basis. Although the motor cost is similar, power module size and
cost would favor the 10 HP design. Cost savings may be reason enough to justify the
choice of a voltage and field system, but drive performance enhancement may be
even more of a justification.
Center-driven unwinds and winders are often performance limited by diameter change
and tension range requirements. The judicious use of a voltage and field design can
expand drive system operating capabilities. System design criteria are listed in section
A.5.2.
A drive with voltage and field control requires a field current regulator. The field current
regulator requires two types of field reference shaping:
•
Type 1 supports a spillover design which maintains full field current from zero to
base speed until the motor approaches its maximum armature voltage. Then, as the
motor speed demand increases, the field current is regulated to a lower value
proportional to the new speed. This is the type often used for an extruder.
•
Type 2 supports a reference determined by a field shaping table generated by a
diameter calculator. The input to the table is a field current reference value
proportional to the instantaneous diameter or motor RPM. See figure A.1 for a
typical curve generated by the field reference function. This is the type used for
unwind and winders.
The WebPak 3000 drive is designed to support a motor field regulator with both
Type 1 and Type 2 capabilities. The WebPak 3000 motor field regulator provides a 6:1
maximum field control range.