2 the, Block, 3 the tension loop – Rockwell Automation WebPak 3000 DC Drive Application Workbook Version 1.1 User Manual
Page 71
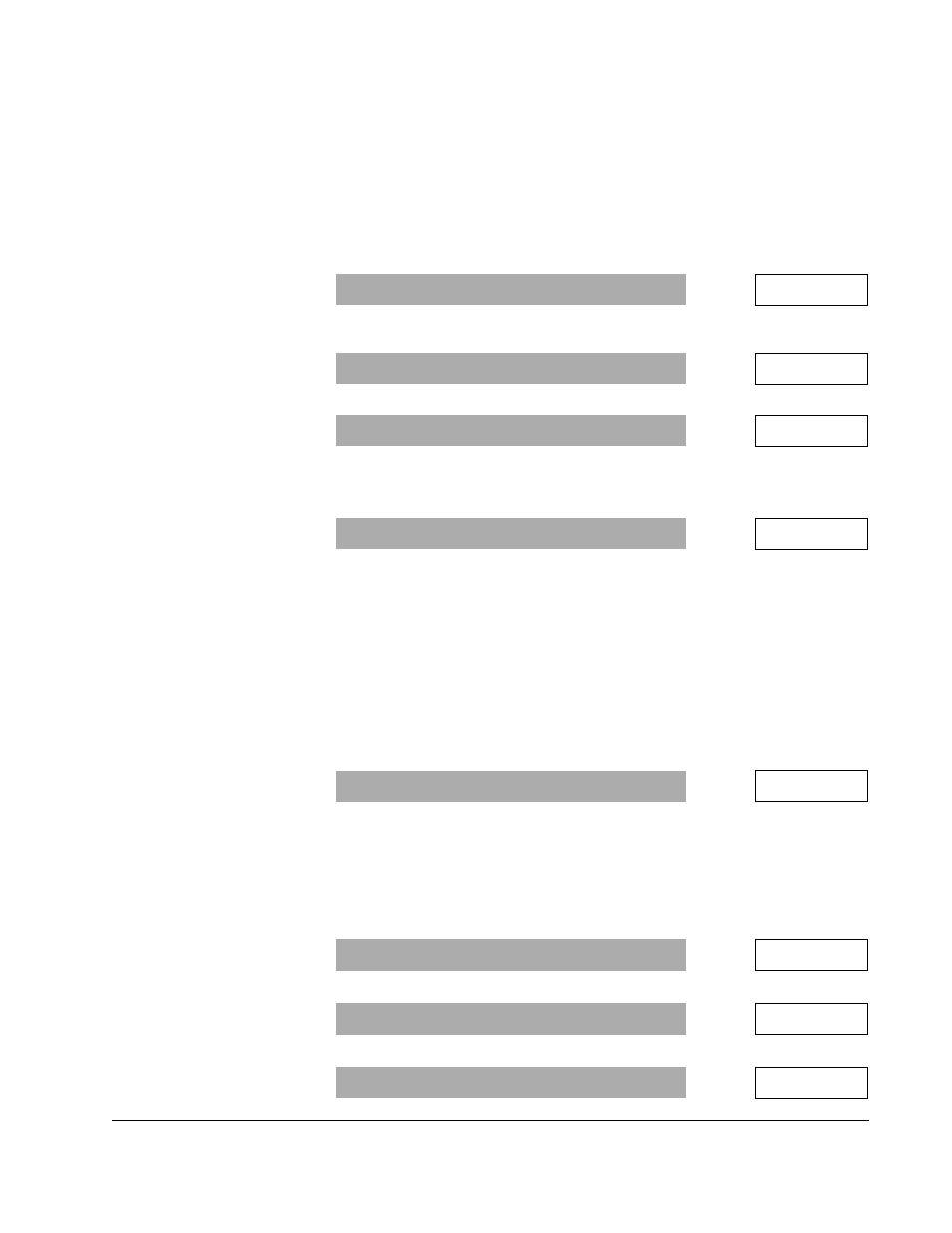
Configuring the Tension Outer Control Loop
12-3
12.1.2 The
LEAD
/
LAG
Block
The tension feedback signal is also conditioned by a
LEAD
/
LAG
block, which is set to
approximately cancel the lag attributable to the speed loop bandwidth. Refer to figure
A.18 in Appendix A of the software manual (D2-3444).
þ
To set up the
LEAD
/
LAG
block:
▲
Set
TEN
FDBK
LL
BYPASS
(P.845) to
OFF
.
▲
Set
TEN
FDBK
LL
LOW
FREQ
(P.835) to the same value as
SPEED
CROSS
OVER
(P.133).
▲
Set
TEN
FDBK
LL
RATIO
(P.836) to 7.5.
þ
To bypass the
LEAD
/
LAG
block:
▲
Set
TEN
FDBK
LL
BYPASS
(P.845) to
ON
.
12.1.3 The Tension Loop
PI
Block
Refer to figure A.19 in Appendix A of the software manual (D2-3444) as you configure
the tension loop
PI
block.
The input to the tension loop
PI
block is
TEN
LOOP
ERROR
(P.834), which is a read-only
parameter.
þ
To set the
PI
block integral gain:
▲
Set
TEN
PI
LEAD
FREQ
(P.840) to 0.2 radians/second.
þ
If the drive is a variable diameter section:
▲
Tune the proportional gain at empty core diameter.
þ
To set the
PI
block proportional gain,
TEN
PI
PROP
GAIN
(P.841):
▲
Set
TEN
PROFILER
ENABLE
(P.878) to
DISABLE
.
▲
Set
OCL
TYPE
(P.818) to
CASCADE
.
▲
Set
OCL
SELECT
(P.817) to
TENSION
.
Range:
OFF
,
ON
P.845 =
2))
Range: 0.01 to 34.90
RAD
/
S
P.835 =
RAD
/
S
Range: 2 to 20
P.836 =
Range:
OFF
,
ON
P.845 =
21
Range: 0.00 to 141.37
RAD
/
S
P.840 =
5$'6
Range:
ENABLE
,
DISABLE
P.878 =
',6$%/(
Range:
CASCADE
,
PARALLEL
P.818 =
&$6&$'(
Range:
NONE
,
TENSION
,
CURRENT
,
POSITION
P.817 =
7(16,21