Rockwell Automation WebPak 3000 DC Drive Application Workbook Version 1.1 User Manual
Page 64
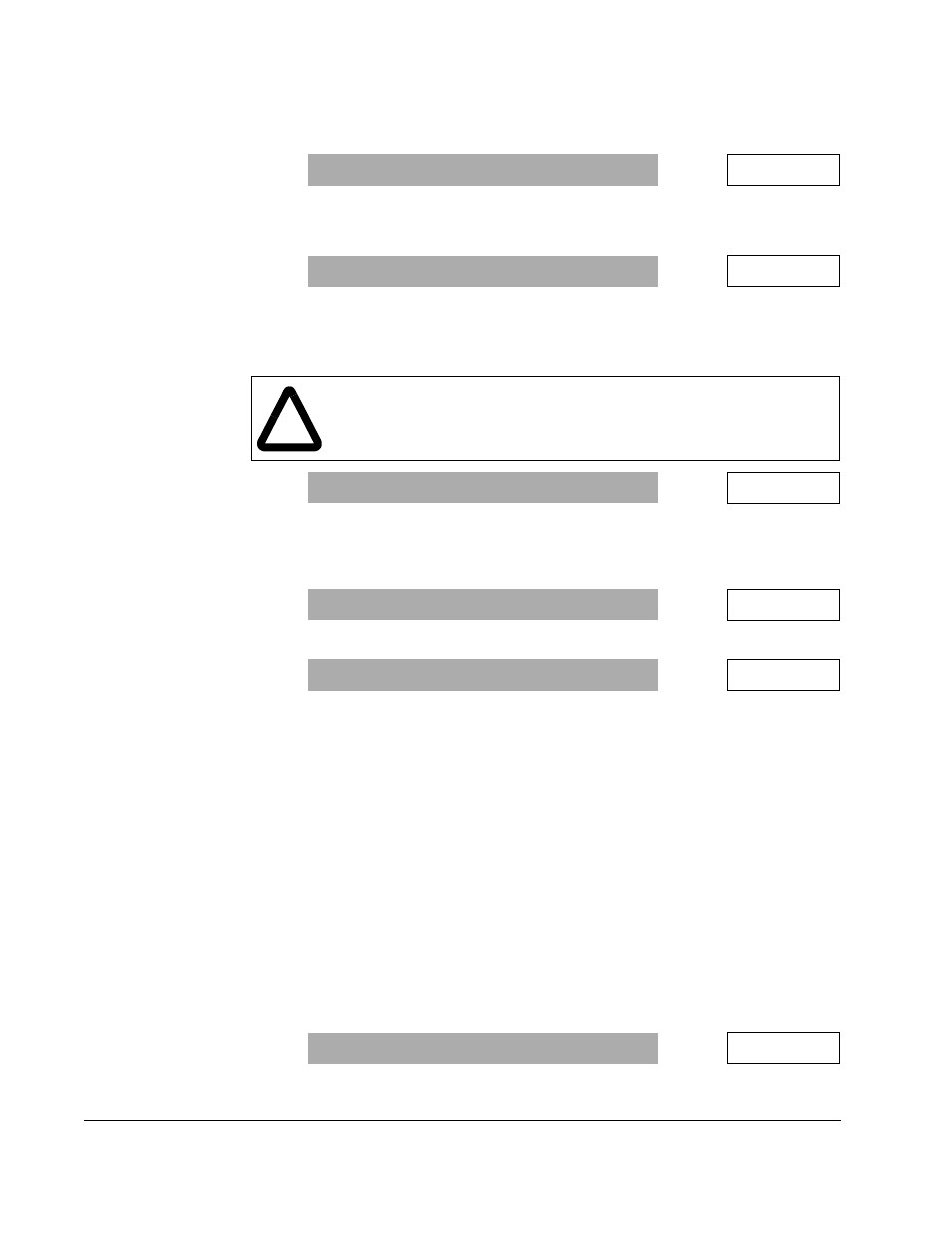
11-2
WebPak 3000 DC Drive Application Workbook, Version 1.1
▲
Set
STORAGE
(P.857) to equal the amount of material in feet that can be stored
in the dancer over which the position feedback varies from 0 to maximum.
▲
Set
TOP
LINE
SPEED
(P.020) to specify the maximum machine speed in feet per
minute. Note that the units of length must be the same as the units used for
STORAGE
(P.857).
▲
Set
POSITION
CROSS
OVER
(P.239) to specify the crossover frequency of the
position loop. This should be set to 5 radians/second. Any higher setting
should be tested so that the proportional gain of the position loop (KP) does
not exceed 60.
þ
If P.239 > 5 radians/second:
▲
See the formula and example at the end of section 11.1.
▲
Set
POSITION
ZETA
(P.242) to 1.0. This is the position loop damping coefficient.
▲
Set
OCL
TYPE
(P.818) to
CASCADE
.
The position gain profiling block outputs the calculated values of four parameters:
•
POS
PI
KP
OUT
(P.248) - the position loop
PI
block proportional gain.
•
POS
PI
WLD
OUT
(P.249) - the position loop
PI
block lead frequency.
•
POS
LL
WLO
OUT
(P.246) - the low frequency setting of the position feedback
LEAD
/
LAG
block.
•
POS
LL
RATIO
OUT
(P.247) - the ratio of the lag-to-lead frequencies of the position
feedback
LEAD
/
LAG
block.
Constant Diameter Applications
For constant diameter applications, the gain profiler is bypassed.
þ
To configure the drive for constant diameter applications:
▲
Set
POS
PROFILER
ENABLE
(P.253) to
DISABLE
.
Range: 0.0 to 10.0
FEET
P.857 =
FEET
Range: 0 to 5000
FPM
P.020 =
FPM
!
ATTENTION: If
POSITION
CROSS
OVER
(P.239) is set to a value higher than
5 radians/second, instability could occur. Failure to observe this
precaution could result in damage to, or destruction of, the equipment.
Range: 0.00 to 60.00
RAD
/
S
P.239 =
RAD
/
S
Range: 0.10 to 10.00
P.242 =
Range:
CASCADE
,
PARALLEL
P.818 =
&$6&$'(
Range:
DISABLE
,
ENABLE
P.253 =
',6$%/(