Speed mode select, 4 speed loop feedback – Rockwell Automation WebPak 3000 DC Drive Application Workbook Version 1.1 User Manual
Page 23
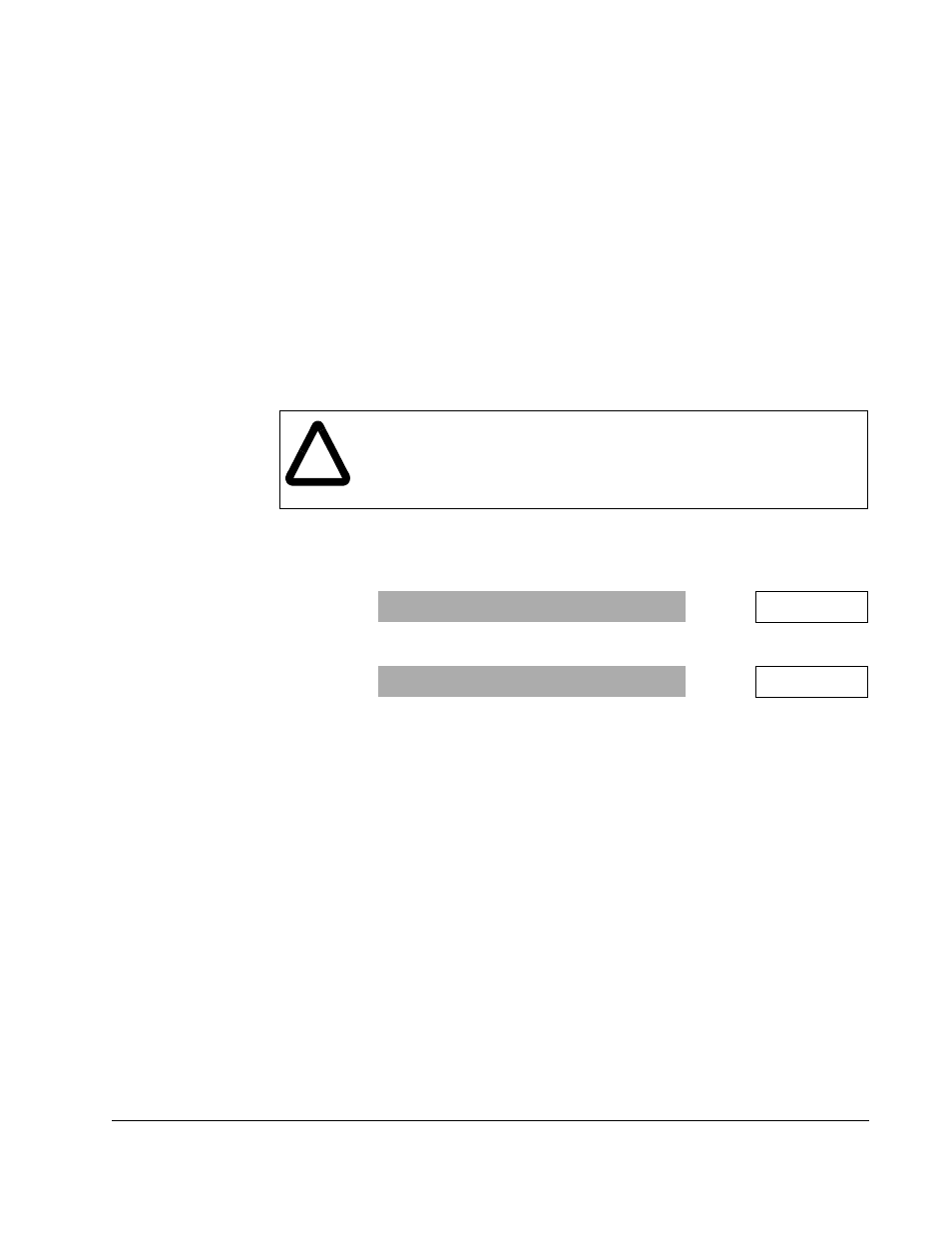
Configuring the Speed Loop
3-13
SPD
LOOP
REFERENCE
(P.295) is the composite signal configured by the various modes
listed in this section. The final value of P.295 is clamped at + or – 110% of
TOP
LINE
SPEED
(P.020). If
REVERSE
DISABLE
(P.015) =
ON
,
SPD
LOOP
REFERENCE
(P.295) is
prevented from setting a reverse reference by clamping this reference to zero.
3.4
Speed Loop Feedback
Refer to figure A.10 in Appendix A of the software manual (D2-3444) as you configure
the speed loop feedback.
þ
To configure the speed loop feedback:
▲
FEEDBACK
SELECT
(P.200) was set during Quick Start to select the type of
feedback signal to be used for the speed/voltage loop. Since the
WebPak 3000 drive standard design is a regenerative power bridge, a DC
tach or a dual-channel differential-output encoder is required.
þ
If
FEEDBACK
SELECT
(P.200) =
DC
TACH
:
▲
If required, set
ANALOG
TACH
ZERO
ADJ
(P.202) to remove any offset from
the analog tachometer feedback signal.
▲
If required, set
ANALOG
TACH
GAIN
ADJ
(P.201) to scale the analog
tachometer feedback signal.
J
11
ANLG
TACH
VLT
SCL
(P.792) displays the position in which to set the J11
hardware jumper based on the values of
GEAR
IN
SPEED
(P.011) and
ANLG
TACH
VOLTS
/1000 (P.203).
J
14
ANLG
TACH
VLT
RNG
(P.793) displays the position in which to set the
J14 hardware jumper based on the values of
GEAR
IN
SPEED
(P.011) and
ANLG
TACH
VOLTS
/1000 (P.203).
See the drive hardware manual (D2-3443) for information on setting the
J11 and J14 jumpers
ANALOG
TACH
FEEDBACK
(P.291) is the digital value of the analog
tachometer feedback input after all hardware and software scaling.
þ
If
FEEDBACK
SELECT
(P.200) =
ENCODER
:
The drive uses the values set during Quick Start for
ENCODER
PPR
(P.207)
and
GEAR
IN
SPEED
(P.011).
ENCODER
KIT
(P.798) indicates whether or not the Pulse Encoder
(Tachometer) kit is installed in the drive and if it has passed diagnostics.
ENCODER
FEEDBACK
(P.292) is the digital value of the encoder after
hardware and software scaling.
!
ATTENTION: The incorrect configuration of
FEEDBACK
SELECT
(P.200),
ANALOG
TACH
GAIN
ADJ
(P.201), and
ANALOG
TACH
ZERO
ADJ
(P.202) can
cause an overspeed condition. This parameter must be configured by a
qualified person who understands the significance of configuring it
accurately. Failure to observe this precaution could result in bodily injury.
Range:-200 to 200
COUNTS
P.202 =
COUNTS
Range: 0.750 to 1.250
P.201 =