Rockwell Automation WebPak 3000 DC Drive Application Workbook Version 1.1 User Manual
Page 82
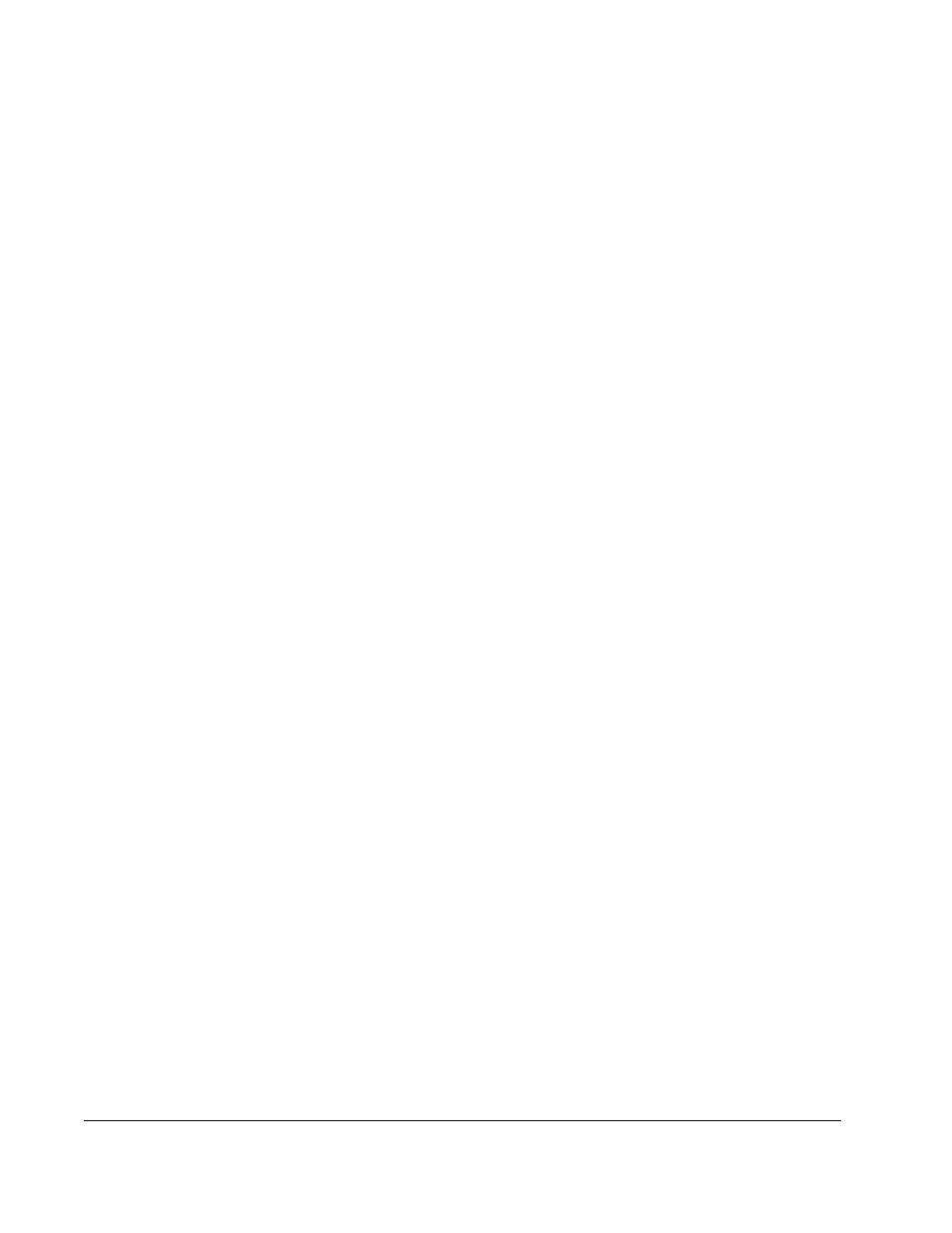
A-4
WebPak 3000 Drive Application Workbook, Version 1.1
The WebPak 3000 drive operating in open loop tension control provides an update
rate of 20 ms and compensates for other machine conditions, such as friction,
windage, and inertia. Motor torque demand includes these loads, as well as, the
torque demand required to establish the tension reference set point.
Profiling these load conditions in the current regulator design improves the accuracy
of the open loop tension control system. Friction and windage values are part of the
start-up process. Inertia compensation is based upon drive calculated values. A
variable diameter section has its values updated by the diameter calculator function.
An unwind or winder using current regulation to control web tension will operate with
an inherent taper tension if the current reference is held constant as the diameter
changes. This means that the tension decrease is directly proportional to roll buildup
on a winder, and the tension increase is directly proportional to roll builddown on an
unwind.
This taper pattern may be unacceptable in certain winding applications, but unwinding
typically requires constant tension over builddown. When inherent taper is not
acceptable, taper profiling with diameter can be used. Because the characteristics of
machine load profiles can impact the range of open loop tension control,
recommended limits for both fixed and variable diameter systems are listed in section
A.5.2.
A second use for the current regulator is a helper or load share drive section. A typical
web process line application is a two-roll laminator with each roll powered by a
separate drive. One roll is the lead section and could be speed, tension, or position
controlled. The second roll would be current-regulated using the load current of the
lead roll as the reference for its load share profile. All of the current regulator functions
described in the open loop tension mode can be applied as required to the load share
mode.
Under the current regulator design, the current loop, acting as the primary control
loop, is cascaded with an inner speed loop. This control scheme provides a more
stable design as well as an inherent speed limit function.
The current major loop includes a gain profiling function to maximize both steady state
and dynamic performance.
A.2.3 Position Regulators
In web processing machines, position regulation assumes that a dancer roll, float roll,
or “Z” roll is used to provide a loop of storage in the web line. A linear or rotary
transducer is coupled to the roll assembly, and the transducer DC voltage signal is
used as position feedback to the drive position loop.
Although, from a drive system perspective, this machine design is true position
feedback, it is applied as a web tension controller. By applying a load (typically via a
pneumatic cylinder), which is opposite to the force developed by web tension, the
drive position regulator will maintain the desired web tension as long as the position
loop stays within its active storage limits, both in dynamic and steady-state line
operation.
The amount of web in the loop, maximum line speed, and maximum line speed rate of
change are machine operating parameters that will impact viable position regulator
design. Design limits for these parameters, for both fixed and variable diameter
systems are listed in section A.5.2.