Rockwell Automation WebPak 3000 DC Drive Application Workbook Version 1.1 User Manual
Page 65
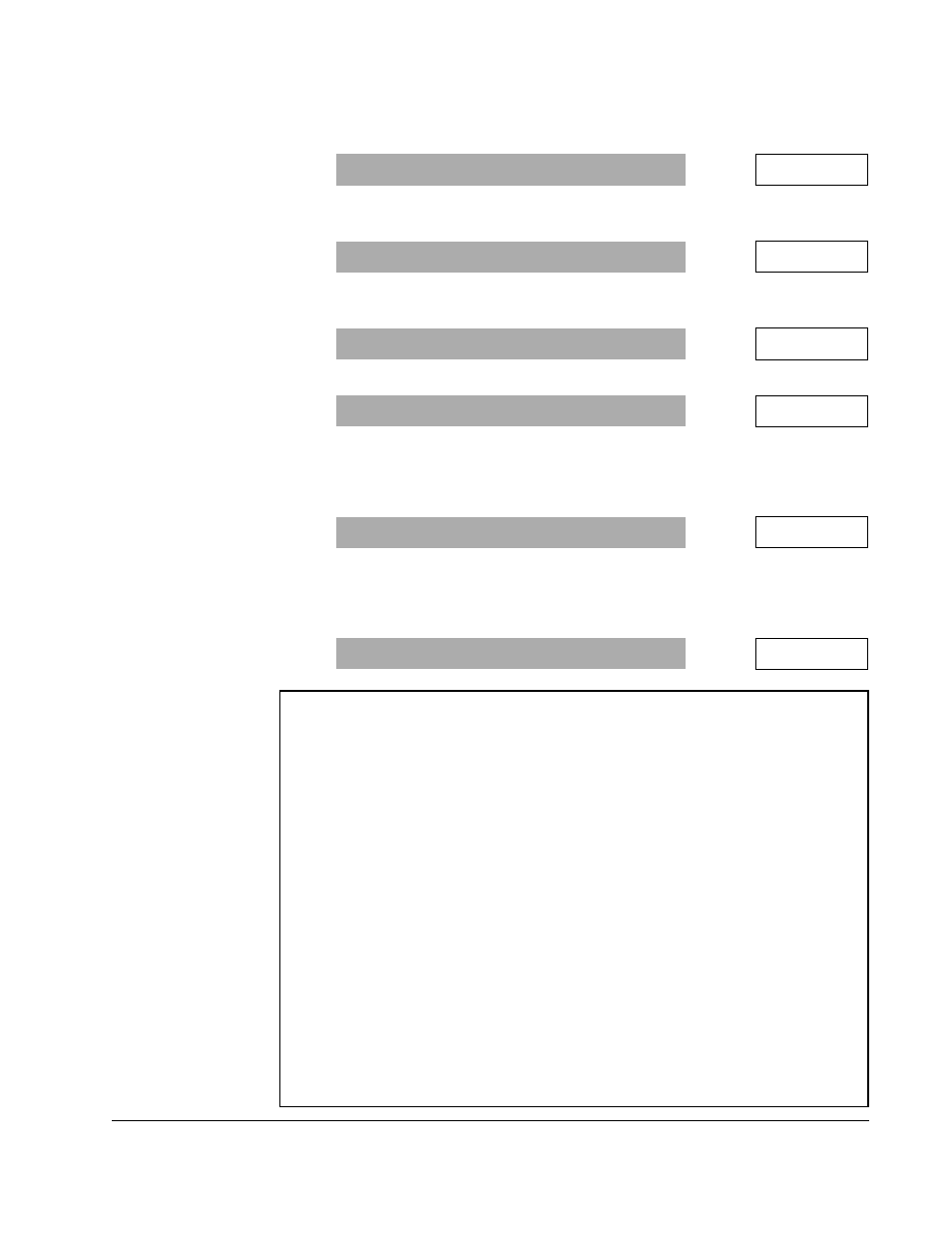
Configuring the Position Outer Loop
11-3
▲
Set
POS
PI
PROP
GAIN
(P.236) using the same test formula as for KP as shown
at the end of this section. P.236 becomes the value for P.248.
▲
Set
POS
PI
LEAD
FREQ
(P.234) to 0.2 radians/seconds. P.234 becomes the
value for P.249.
▲
Set
POS
LEADLAG
LOW
FREQ
(P.231) to the same value as
SPEED
CROSS
OVER
(P.133). P.231 becomes the value for P.246.
▲
Set
POS
LEADLAG
RATIO
(P.232) to 7.5. P.232 becomes the value for P.247.
▲
If required, tune the position loop performance by increasing
POS
PI
PROP
GAIN
(P.236). However, since raising the value of P.236 also increases
POSITION
CROSS
OVER
(P.239), the value of
POS
PI
LEAD
FREQ
(P.234) may also need to
be increased.
▲
Set
POS
LEADLAG
BYPASS
(P.255). The use of the lead/lag function for the
position feedback is recommended for applications with or without position
gain profiling. Bypass of this function can be accomplished using
POS
LEADLAG
BYPASS
(P.255).
Range: 0.10 to 128.00
P.236 =
Range: 0.00 to 141.37
RAD
/
S
P.234 =
5$'6
Range: 1.00 to 34.90
RAD
/
S
P.231 =
RAD
/
S
Range: 2 to 20
P.232 =
Range: 0.10 to 128.00
P.236 =
Range:
ON
,
OFF
P.255 =
Testing the Value of Position Cross Over (P.239)
Use the following formula if the value of P.239 exceeds 5 radians/second.
KP = (PCO x S) / (LS x (PV% / 100))
Where:
•
PCO
=
POSITION
CROSS
OVER
(P.239)
•
KP
=
POS
PI
PROP
GAIN
(P.236)
•
PV
% =
POS
VERNIER
PERCENT
(P.238)
•
S
=
STORAGE
(P.857)
•
LS
=
TOP
LINE
SPEED
(P.020)
Example:
If
POSITION
CROSS
OVER
(P.239) is nominally set to 5.0 radians/seconds:
•
PV
% (P.238) is set to 10
•
S
= 5 feet
•
LS
= 20 feet/second
Then:
KP
= (5 x 5) / (20 x (10 / 100)) = 12.5
In this example, since
KP
did not exceed 60,
PCO
could be increased to raise the
value of
KP
to maximize position loop performance.