Rockwell Automation WebPak 3000 DC Drive Application Workbook Version 1.1 User Manual
Page 83
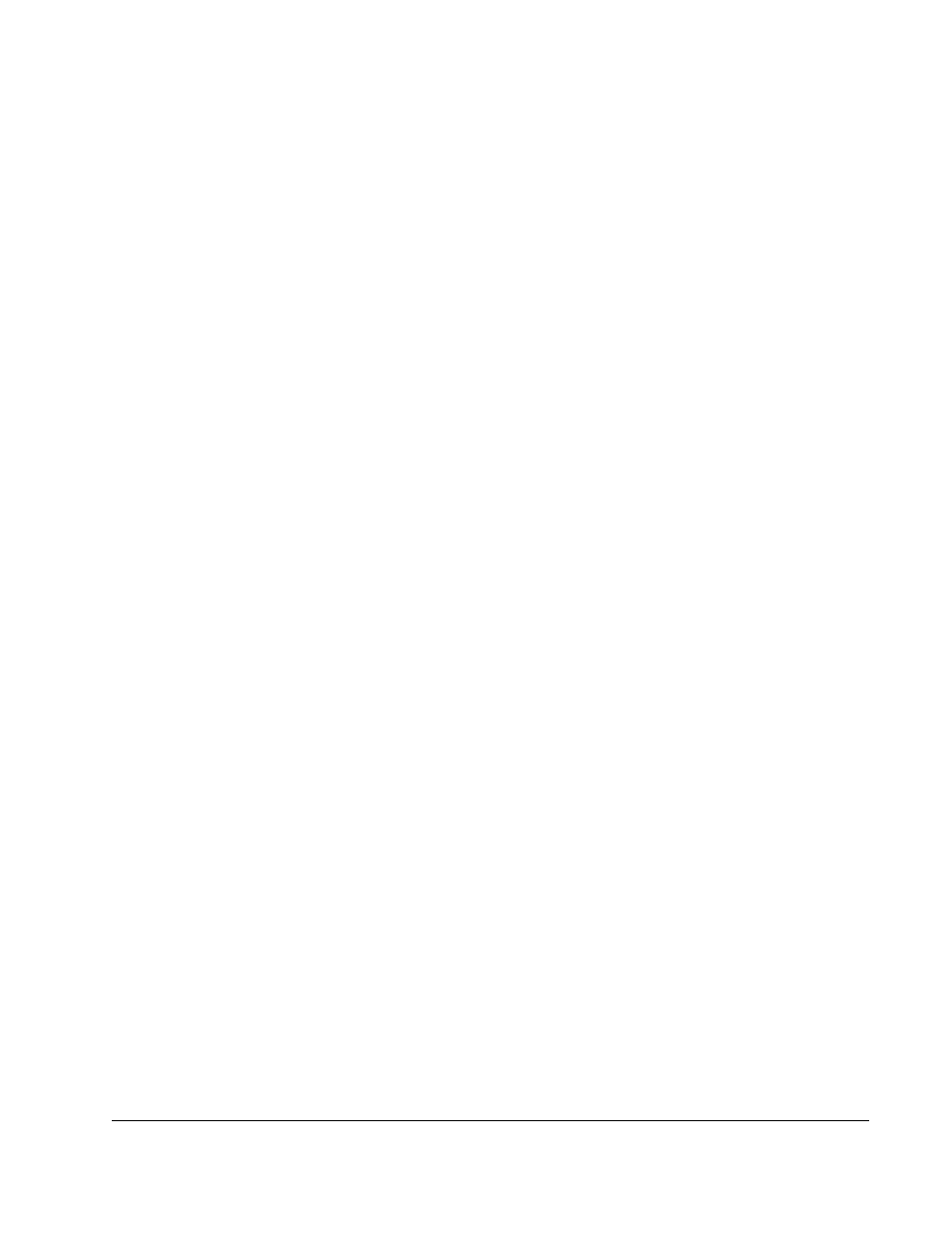
Using the WebPak 3000 Drive for Web Applications: The Basics
A-5
Changing the load by mechanically adjusting the air supply to the pneumatic cylinder
will change web tension. However, a voltage-to-pneumatic (E-to-P) controller applied
to the pneumatic cylinder air supply will allow web tension to be set remotely by an
operator’s device.
This electrical setpoint can be programmed to provide a tension profile, such as taper
tension for a center winder. Under position regulation, the operating tension range is
not limited by the electrical drive system. The mechanical characteristics of the dancer
roll structure will establish both the high and low tension boundaries.
Variable position loop control assumes that the dancer roll assembly tracks the web
during all normal steady-state and dynamic machine conditions. Thus, the high
tension limit is set by the mechanical maximum load of the dancer assembly, and the
low tension limit is set by the friction and the mass of the dancer assembly.
The mass effect can be compensated for by counter-loading the assembly. Friction
can be minimized but not realistically to zero. Since the dancer must move to regulate
loop position, the differential tension developed across the dancer assembly to move it
establishes the minimum web tension value.
The position loop is configured to operate in cascade with an inner speed loop with a
20 ms update rate. By calibrating the speed loop to follow the master line speed, the
output of the position loop can be programmed to operate as a percent trim of the
speed loop. The amount of trim used is based upon machine requirements, but is
typically set at
±
10%.
For variable diameter sections, the inner speed loop is programmed to be
compensated as the roll diameter changes. The diameter calculator provides this
speed loop compensation, which dynamically adjusts the speed loop to operate as an
accurate surface speed regulator at all diameters.
The position loop includes a gain profiling function to maximize both steady state and
dynamic performance.
A.2.4 Tension Regulators
The WebPak 3000 tension regulator operates as a direct web tension control system.
The tension loop feedback voltage signal is derived from a load cell on the web line.
The load cell couples the drive directly to the web line parameters of modulus of
elasticity, cross-sectional area, and length of material in the control zone span. The
dynamics of these parameters impact the tuning of the tension loop stability and
dynamic response.
Web lines that are designed to run products that exhibit wide ranges of moduli of
elasticity and cross-sectional areas may not support maximized drive performance
with one set of tuning values. Multiple product web lines may further complicate
tension loop tuning if alternate web paths are used and the web length in the tension
control zone changes.
Tension operating ranges recommended for fixed and variable diameter systems are
listed in section A.5.2.
The tension regulator supports both parallel and cascade loop design with separate
gain profiling for each. Tension setpoint generation includes roll diameter profiled
taper function. The profile is selectable for linear or hyperbolic taper.