Operation – IAI America PSEP User Manual
Page 79
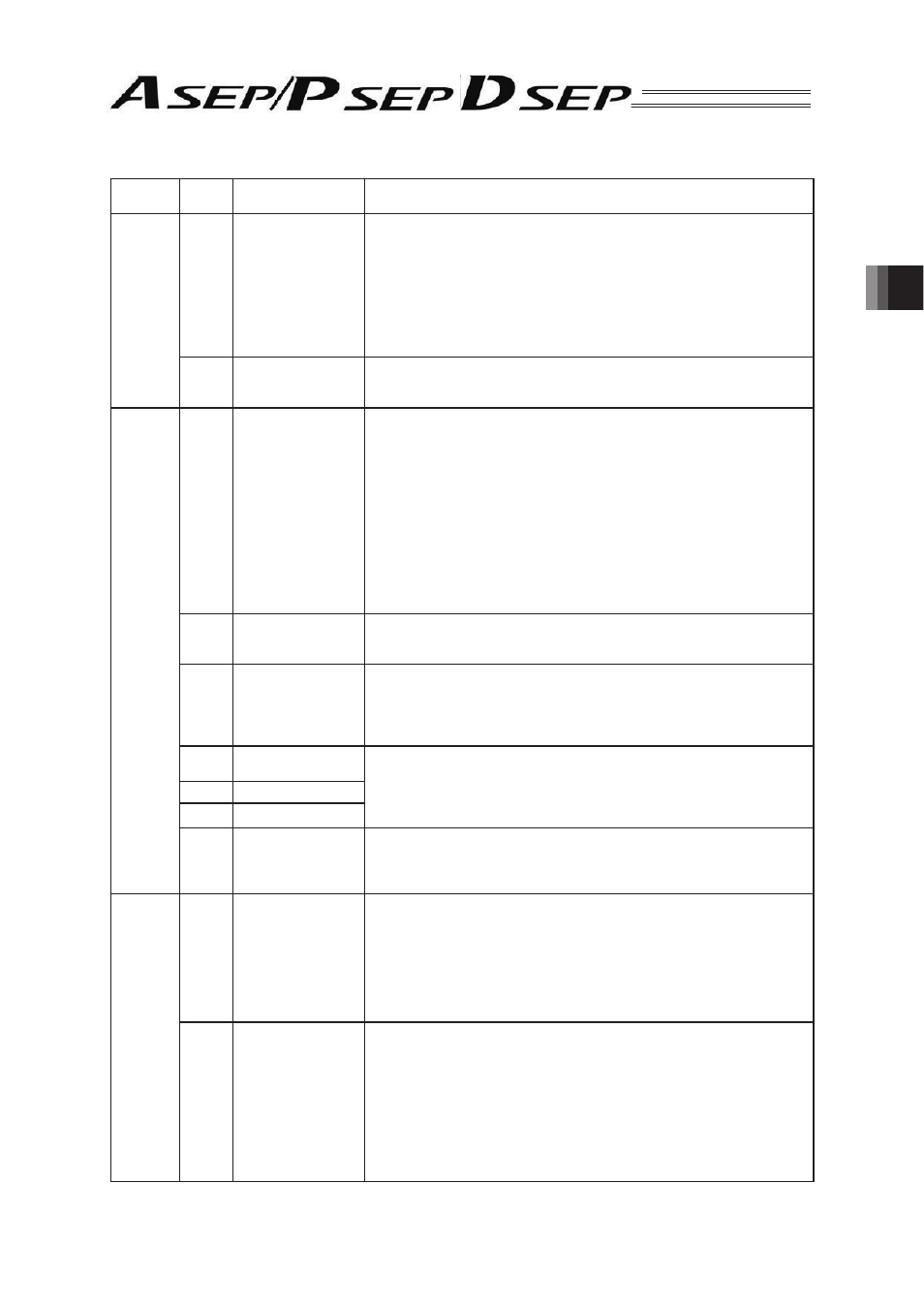
73
/
3.
Operation
Error
Level
Code
Alarm Name
Cause/Treatment
Operation
Cancellation
0D9
Software Stroke Limit-
Over Error
Cause :
(1)
In the case that the actuator is vertically installed and the target position is close
to the soft limit, because the load is too high, or the deceleration setting is too
high, an over-chute might occur and the actuator might exceed the soft limit.
(2)
The actuator is moved out of the soft limit range when the servo-motor is turned
OFF, and then the servo-motor turning ON operation is performed.
Treatment :
(1)
Set the deceleration curve so that an over-chute is not caused when the actuator
is stopped.
(2)
Return the actuator within the soft limit range and perform the servo-motor
turning ON operation.
0DC
Pressing Motion Range
Over Error
This alarm is generated when the reaction force after the pressing operation complete is too high
and the actuator is pushed back to the start point of pressing operation. Revise the construction
of the whole system.
Cold Start
0E0
Overload
Cause :
(1) The load is increased too much due to a external force.
(2) In the case of the unit with the brake, the brake is not released.
(3) The actuator’s sliding resistance might be partly too large.
Treatment :
(1) In the case that an abnormal external force is impressed, remove it.
(2)
Check that the brake is released when the servo-motor is turned ON. If not, a
breakdown of the brake, cable breakage, or defective part inside the controller,
etc., is considered.
(3)
In the case that the work can be moved by hand, move it. Then, check that there
is no location where a sliding resistant is too large.
If the error is caused by the above item (2) or (3), contact our company.
Note :
Restart the operation after making sure to remove the cause. Also, in the case that
the power is turned OFF, turn ON the power again after 30 minutes or to prevent
motor coil burning.
0E5
Encoder Signal Receipt
Error
Cause :
The missing connector inside the controller is considered.
Treatment :
In the case that the same error is caused after the power to the controller is re-input,
contact our company.
0E7
A, B or Z-phase Wire
Breakage
The encoder signal is not detected normally.
Cause :
A looseness or wire breakage in the connector section of the actuator connecting
cable is considered.
Treatment :
Check for the connection condition of the actuator connecting cable and perform the
continuity test. If normal, contact our company.
0E8
A or B-phase Wire
Breakage
The encoder signal is not detected normally.
Cause :
A looseness or wire breakage in the connector section of the actuator connecting
cable is considered.
Treatment :
Check for the connection condition of the actuator connecting cable and perform the
continuity test. If normal, contact our company.
0E9
A -phase Wire Breakage
0EA
B-phase Wire Breakage
0EC
PS-phase Wire Breakage
Cause :
A looseness or wire breakage in the connector section of the actuator connecting
cable is considered.
Treatment :
Check for the connection condition of the actuator connecting cable and perform the
continuity test. If normal, contact our company.
Operation
Cancellation
0ED
Absolute Encoder Error
Detection 1
Cause :
(1)
When the absolute unit reset is completed and the power is re-input, the current
position might be changed due to an external force.
(2)
When the absolute unit is reset, the current position might be changed due to an
external force.
Treatment :
(1)
Turn OFF the power and arrange so that a vibration is not added to the actuator
and turn ON the power again.
(2)
Arrange so that a vibration is not added to the actuator and perform the home
return operation again.
0EE
Absolute Encoder Error
Detection 2
&DXVH
,WPLJKWEHFDXVHGLQWKHVLPSOL¿HGDEVROXWHW\SHZKHQWKHSRZHULVWXUQHG21
IRUWKH¿UVWWLPHDIWHUWKHEDWWHU\LVFRQQHFWHG
(2) The battery voltage is too much decreased to keep the encoder counter operation.
(3)
The encoder cable is disconnected during the power failure, or a wire breakage
occurs in the encoder cable.
(4) The parameter is changed.
Treatment :
In the case of (1), (2) or (4), perform the Absolute Reset operation according to the
procedure.
6XSSO\WKHSRZHUIRUKRXUVRUPRUHWRFKDUJHWKHEDWWHU\VXI¿FLHQWO\DQGWKHQ
perform the Absolute Reset operation.