Backlash compensation by dual-loop – Yaskawa LEGEND-MC User Manual
Page 351
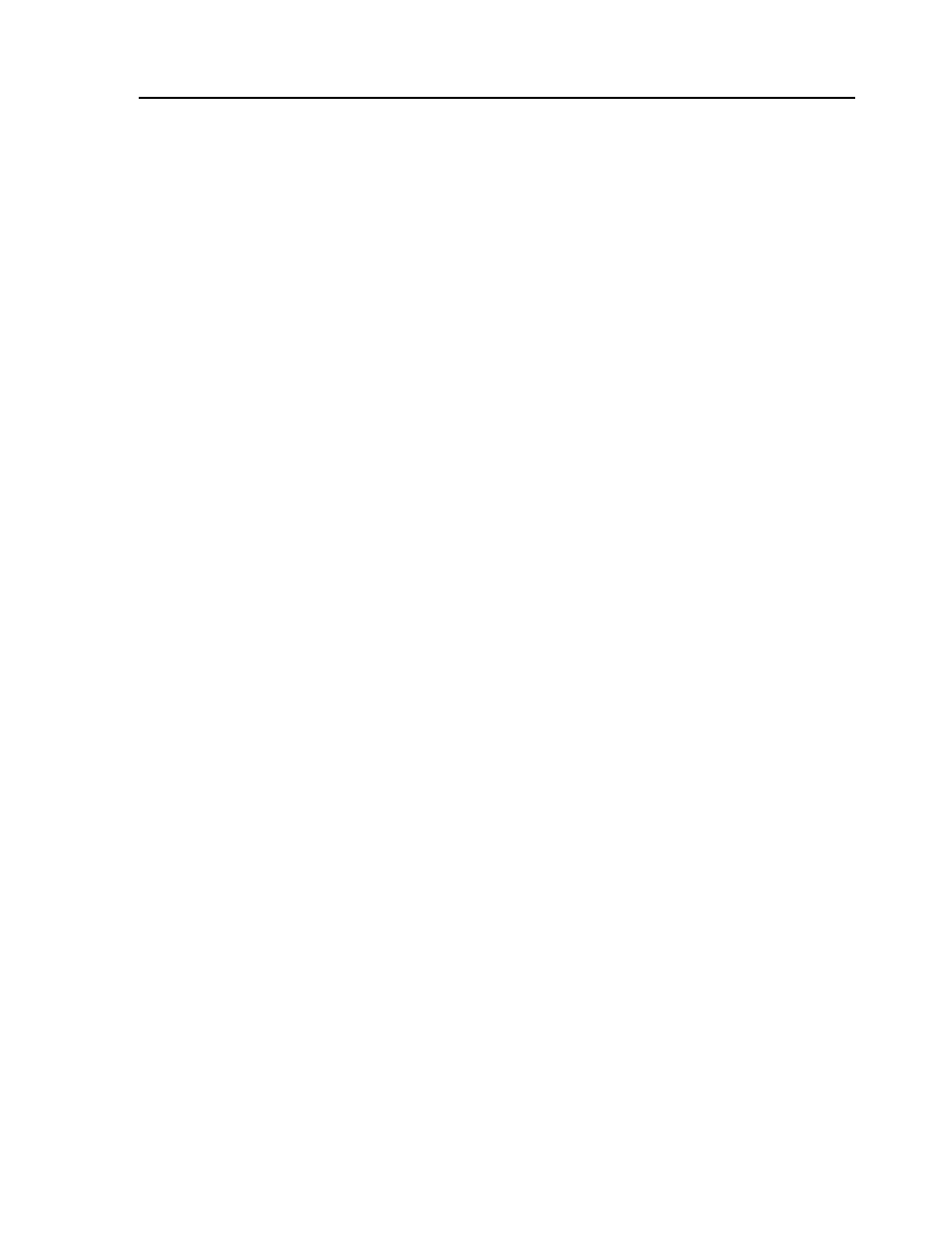
341
LEGEND-MC User’s Manual
Backlash Compensation by Dual-Loop
This design example addresses the basic problems of backlash in motion control systems. The objective
is to control the position of a linear slide precisely. The slide is to be controlled by a rotary motor, which
is coupled to the slide by a leadscrew. Such a leadscrew has a backlash of 4 micron, and the required
position accuracy is for 0.5 micron.
The dilemma is where to mount the sensor. A rotary sensor, gives a 4-micron backlash error. If a linear
encoder is used, the backlash in the feedback loop will cause oscillations due to instability.
An alternative approach is the dual-loop, using two sensors, rotary and linear. The rotary sensor assures
stability (because the position loop is closed before the backlash); the linear sensor provides accurate
load position information. The principle is to drive the motor to a given rotary position near the final
point. The load position is then read to find position error and the controller commands the motor to
move to a new rotary position which eliminates the position error.
Since the required accuracy is 0.5 micron, the resolution of the linear sensor should preferably be twice
finer. A linear sensor with a resolution of 0.25 micron allows a position error of +/-2 counts.
The dual-loop approach requires the resolution of the rotary sensor to be equal or better than that of the
linear system. Assuming that the pitch of the lead screw is 2.5mm (approximately 10 turns per inch), a
rotary encoder of 2500 lines per turn or 10,000 count per revolution results in a rotary resolution of 0.25
micron. This results in equal resolution on both linear and rotary sensors.
To illustrate the control method, assume that the rotary encoder is used as a feedback for the X-axis, and
that the linear sensor is read and stored in the variable LINPOS. Further assume that at the start, both the
position of X and the value of LINPOS are equal to zero. Now assume that the objective is to move the
linear load to the position of 1000.
The first step is to command the X motor to move to the rotary position of 1000. Once it arrives we check
the position of the load. If, for example, the load position is 980 counts, it implies that a correction of 20
counts must be made. However, when the X-axis is commanded to be at the position of 1000, suppose
that the actual position is only 995, implying that X has a position error of 5 counts, which will be
eliminated once the motor settles. This implies that the correction needs to be only 15 counts, since 5
counts out of the 20 would be corrected by the X-axis. Accordingly, the motion correction should be:
Correction = Load Position Error - Rotary Position Error
The correction can be performed a few times until the error drops below +/-2 counts. Often, this is
performed in one correction cycle.