Tool data 5.2 – HEIDENHAIN TNC 320 (34055x-06) User Manual
Page 159
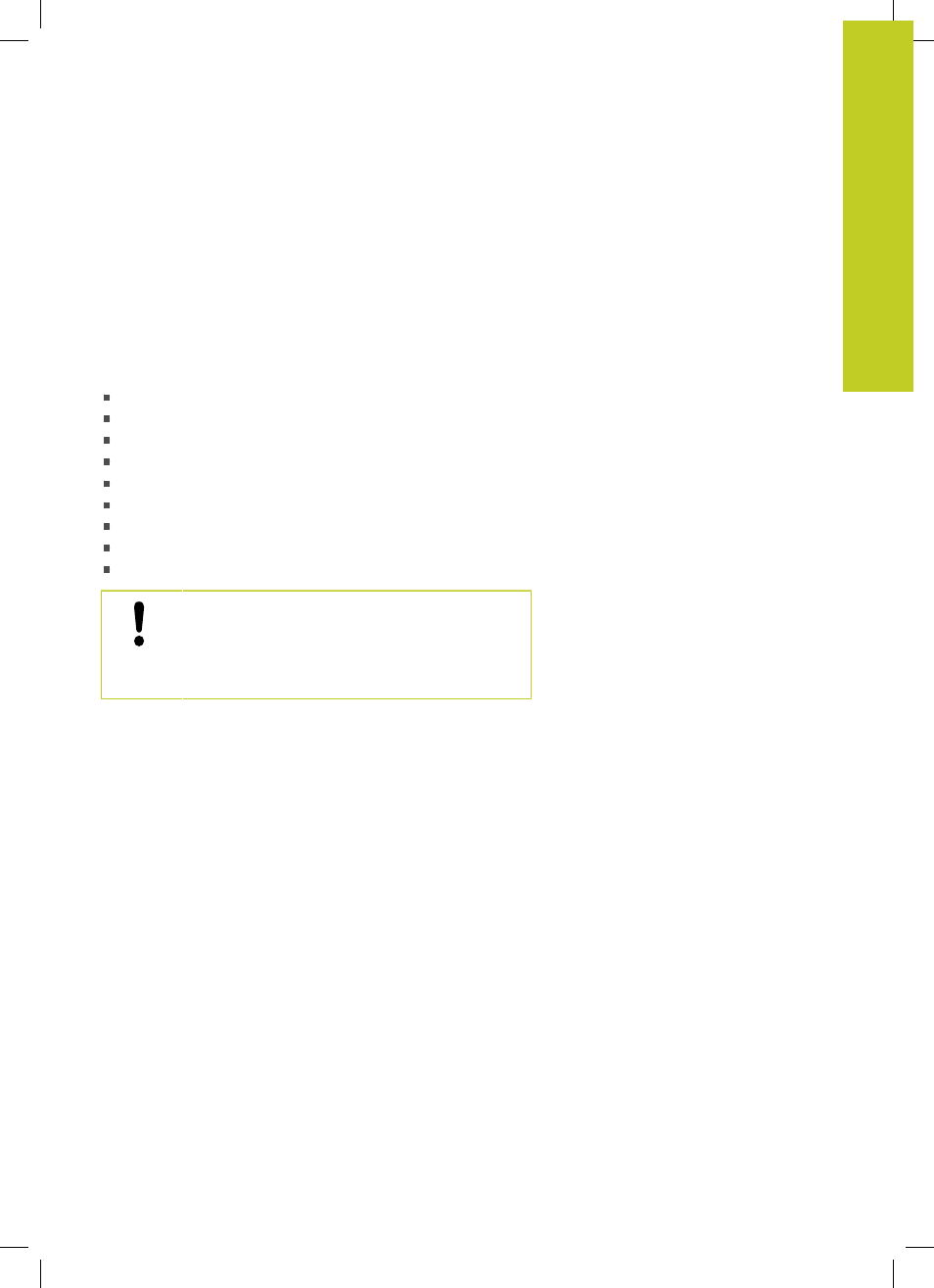
Tool data
5.2
5
TNC 320 | User's Manual HEIDENHAIN Conversational Programming | 5/2013
159
Enter the respective tool life after which machining is to be
continued with a replacement tool in the
TIME2 column of the tool
table. In the
CUR_TIME column the TNC enters the current tool life.
If the current tool life is higher than the value entered in the
TIME2
column, a replacement tool will be inserted at the next possible
point in the program no later than one minute after expiration of
the tool life. The change is made only after the NC block has been
completed.
The TNC performs the automatic tool change at a suitable point in
the program. The automatic tool change is not performed:
During execution of machining cycles
While radius compensation is active (
RR/RL)
Directly after an approach function
APPR
Directly before a departure function
DEP
Directly before and after
CHF and RND
During execution of macros
During execution of a tool change
Directly after a
TOOL CALL or TOOL DEF
During execution of SL cycles
Caution: Danger to the workpiece and tool!
Switch off the automatic tool change with
M102 if
you are working with special tools (e.g. side mill
cutter) because the TNC at first always moves the
tool away from the workpiece in tool axis direction.
Depending on the NC program, the machining time can increase as
a result of the tool life verification and calculation of the automatic
tool change. You can influence this with the optional input element
BT (block tolerance)
If you enter the
M101 function, the TNC continues the dialog by
requesting the
BT. Here you define the number of NC blocks (1
- 100) by which the automatic tool change may be delayed. The
resulting time period by which the tool change is delayed depends
on the content of the NC blocks (e.g. feed rate, path). If you do not
define
BT, the TNC uses the value 1 or, if applicable, a default value
defined by the machine manufacturer.