G - encoder use and torque capabilities, When to use an encoder, Appendix g – Rockwell Automation 7000 PowerFlex Medium Voltage AC Drive (B Frame) - ForGe Control User Manual
Page 201: Encoder use and torque capabilities, Appendix
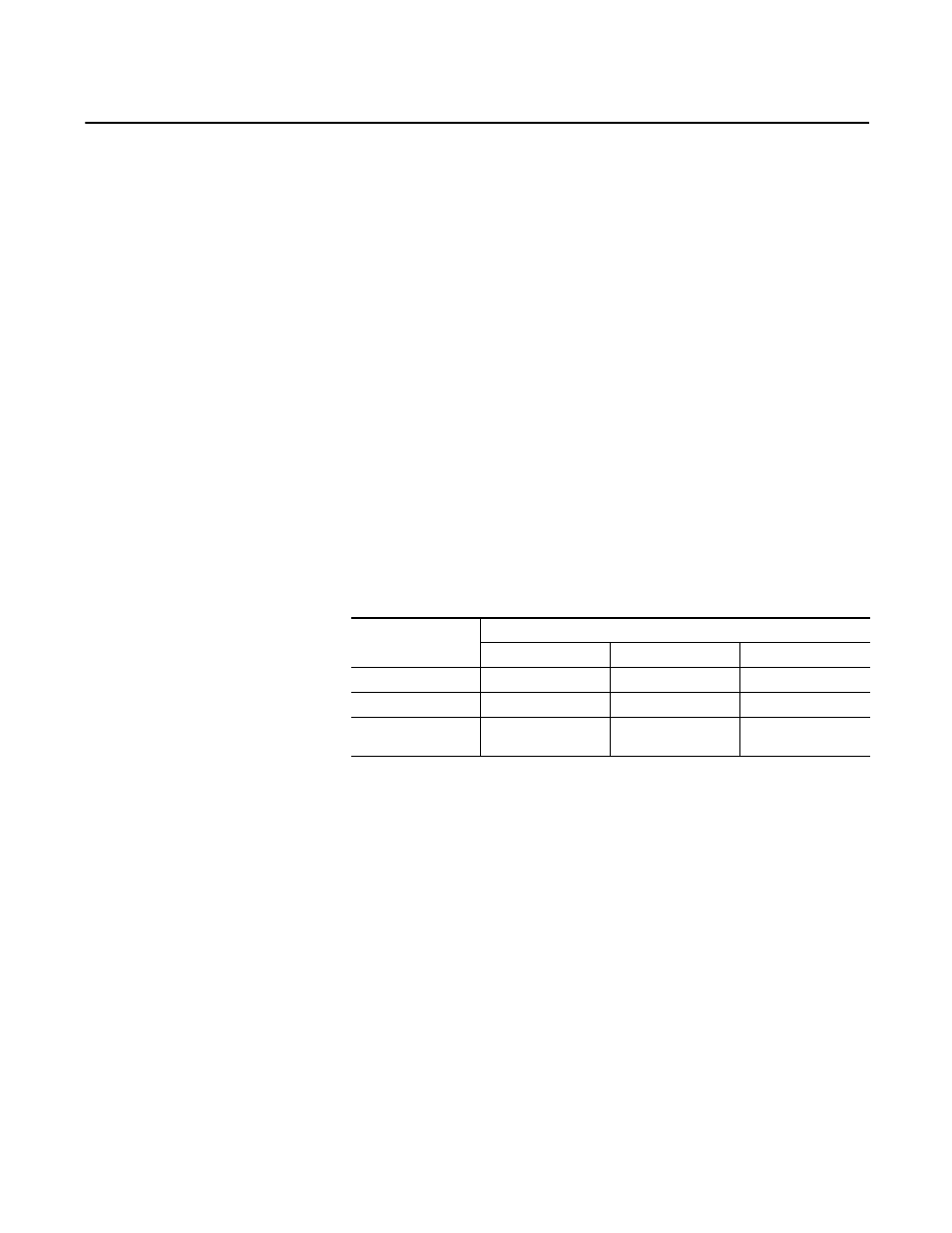
Rockwell Automation Publication 7000-UM202B-EN-P - June 2014
201
Appendix
G
Encoder Use and Torque Capabilities
When to use an Encoder?
An Encoder is required under the following conditions:
1.
When speed regulation accuracy must be between 0.01...0.02% of nominal
speed.
2.
When the zero speed breakaway torque needed is greater than 90% of
continuous running torque.
3.
When continuous running speed is greater than or equal to 0.1 Hz, but less
than 6 Hz.
4.
For minimizing restart times using the flying start capability in forward or
reverse direction.
5.
At any time when high performance torque or speed control mode
(HPTC) is enabled.
Table 13 - PowerFlex Speed Regulation
Notes:
•
Speed regulation is based on a percentage of motor synchronous speed.
•
Encoder to be mounted on the AC machine
•
Operational 15V DC Power Supply mounted in drive to power the
Encoder as a standard option with the Encoder feed back card.
•
Customer is responsible for providing and mounting of Encoder
•
Sleeve bearing motors require the Encoder to have an axial movement
tolerance.
•
Recommended Encoders are shaft mounting type, examples are the Avtron
585 and 685 models or the Northstar (Lakeshore) RIM Tach HS85,
12...15V models or equivalent. Magneto resistive models are more
adaptable to harsh environments.
•
When installing, the Encoder body and electronics must be isolated from
ground (options available from the Encoder manufacturer to accomplish
this).
Encoder
Frequency Output
<6 Hz
6...15 Hz
>15 Hz
Without Encoder
Not applicable
0.1%
0.1%
With Encoder
0.02%
0.01%
0.01%
With Encoder and HPTC
mode enabled
0.01%
0.01%
0.01%