11 preparing the restart, Preparing the restart ( 59), 8commissioning of the canopen logic bus – Lenze CANopen Controller-based Automation User Manual
Page 59
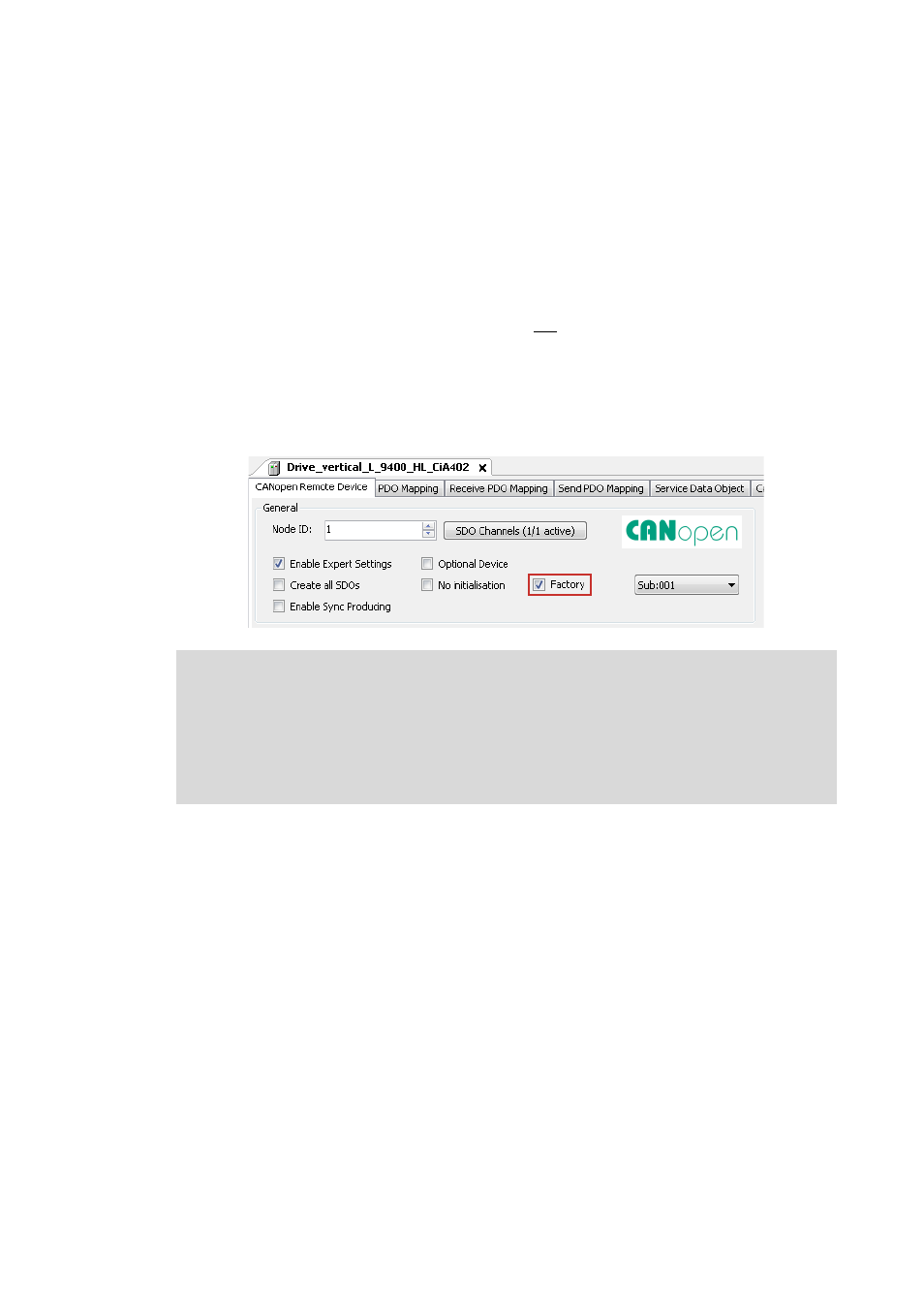
8
Commissioning of the CANopen Logic bus
8.11
Preparing the restart
59
Lenze · Controller-based Automation · CANopen® Communication Manual · DMS 6.3 EN · 04/2014 · TD17
_ _ _ _ _ _ _ _ _ _ _ _ _ _ _ _ _ _ _ _ _ _ _ _ _ _ _ _ _ _ _ _ _ _ _ _ _ _ _ _ _ _ _ _ _ _ _ _ _ _ _ _ _ _ _ _ _ _ _ _ _ _ _ _
8.11
Preparing the restart
In the control technology system you can use the Lenze Controller to transmit the complete
parameter setting via SDO initialisation to the field devices when the machine is switched on.
According to DS301, the Lenze Controller always initialises the CAN parameters of the field devices.
Additionally the controller can initialise further parameters. The values for this must be stored in
the Control configuration under the Service Data Objects tab.
Usually, the Lenze Controller only transmits the SDO objects for which you have stored another
value than the standard value. The controller does not compare these values with the existing
values in the field device. Thus, not all parameters changed there may be set correctly.
If you want a factory adjustment to be carried out in the field device before the SDO initialisation is
carried out, tick under the CANopen Remote Device tab ...
1. "Enable Expert Settings",
2. "Default Settings":
The Service Data Objects tab contains the codes which are written in the EDS file. The EDS file
contains all writable codes.
Note!
During a factory adjustment, the parameter setting in the field device, which you have
carried out with the »Engineer«, gets lost. In this case, you have to transmit all parameter
values manually to the Service Data Objects tab. This only makes sense when
commissioning is completed and all parameters are optimised. If you change something
afterwards via the »Engineer«, you have to maintain it in the PLC program.