6 planning the canopen network, Planning the canopen network, 6planning the canopen network – Lenze CANopen Controller-based Automation User Manual
Page 25
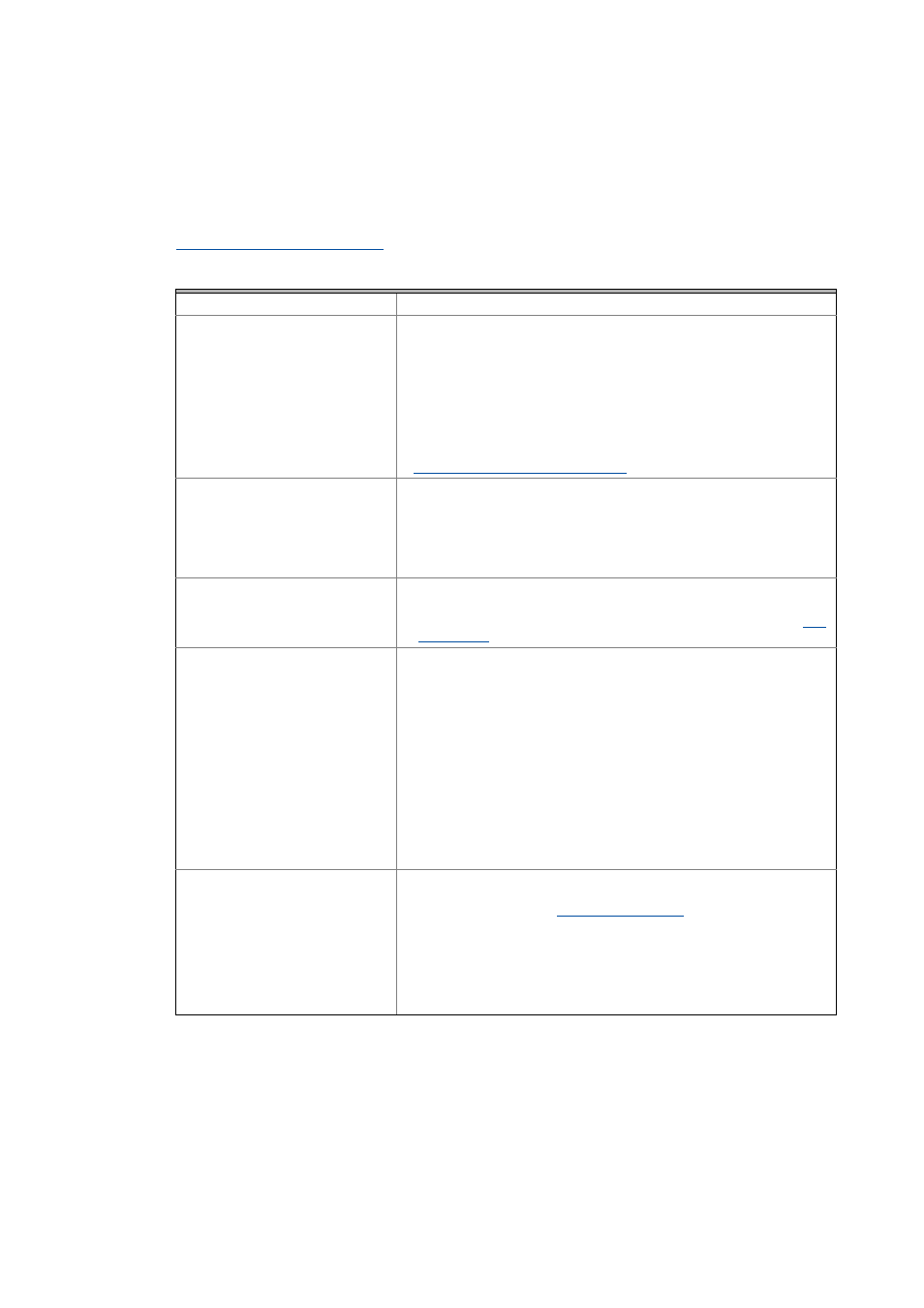
6
Planning the CANopen network
25
Lenze · Controller-based Automation · CANopen® Communication Manual · DMS 6.3 EN · 04/2014 · TD17
_ _ _ _ _ _ _ _ _ _ _ _ _ _ _ _ _ _ _ _ _ _ _ _ _ _ _ _ _ _ _ _ _ _ _ _ _ _ _ _ _ _ _ _ _ _ _ _ _ _ _ _ _ _ _ _ _ _ _ _ _ _ _ _
6
Planning the CANopen network
Create an overview screen of the planned CANopen network with all field devices to be
implemented. Start with the Lenze Controller and arrange the other field devices below it (see
Provide the following data for each device:
Type
Type designation of the field device
Used CAN interface of the device
• The functionality of the two available CAN interfaces is identical. Both
Logic and Motion devices can be connected. The combination of Logic and
Motion on an interface is possible as well.
• If possible, the Logic and Motion devices should be installed on different
CAN lines:
• The requirements of the Motion devices regarding the synchronicity of
the bus are higher.
• Shorter cycle times are needed.
• The data volume to be transferred is larger.
CANopen (Logic) / CANopen (Motion) ( 16)
Unambiguous CAN node address
• If system bus (CAN) devices are used, max. 63 nodes/node addresses are
possible.
• With CANopen-compliant devices, up to 127 nodes/node addresses are
possible.
Note: Do not use the node address 1, in order to avoid unintentional
mistakes and conflicts with a device containing the factory adjustment.
Baud rate
• The baud rate applies to all nodes of the CANopen network.
• 50, 125, 250 and 500 kbps are supported by all device types of the system.
• Observe the connection between bus cable length and baud rate.
Master task of the device
(NMT master/Sync master)
• An NMT master sets itself and then the NMT slaves to the "Operational"
state. In this state, process data can be communicated. Generally, there
can be an optional number of NMT masters on one CANopen bus.
• A Sync master cyclically sends a sync telegram providing for an exactly
simultaneous processing of process data and/or a simultaneous task
start in all sync receivers.
• Via CAN synchronisation, the Lenze Controller can influence the exact
time of the following events in the field device:
• Acceptance and transmission of sync-controlled PDOs
• Starting time of the task of the application (only possible in 9400)
• You only need to use CAN synchronisation on the Logic bus if an exact
simultaneity in the range of milliseconds is of importance. A mere
operating periphery (operator button, control lamps, etc.) does not
require CAN synchronisation.
CAN objects and COB-IDs
• Plan your COB-IDs according to the CANopen DS301 communication
profile. This convention is optimised for the communication with a
central master device.
• Up to 4 PDOs per device can be identified with this scheme. If you require
more, e.g. for a modular I/O system with more than 8 modules, you can
add them later.
• You can easily assign the node during the bus diagnostics by means of the
COB-IDs.
• COB-ID = basic identifier + node address