2 multi-encoder connection, Multi-encoder connection, Technical data – Lenze 8400 User Manual
Page 85
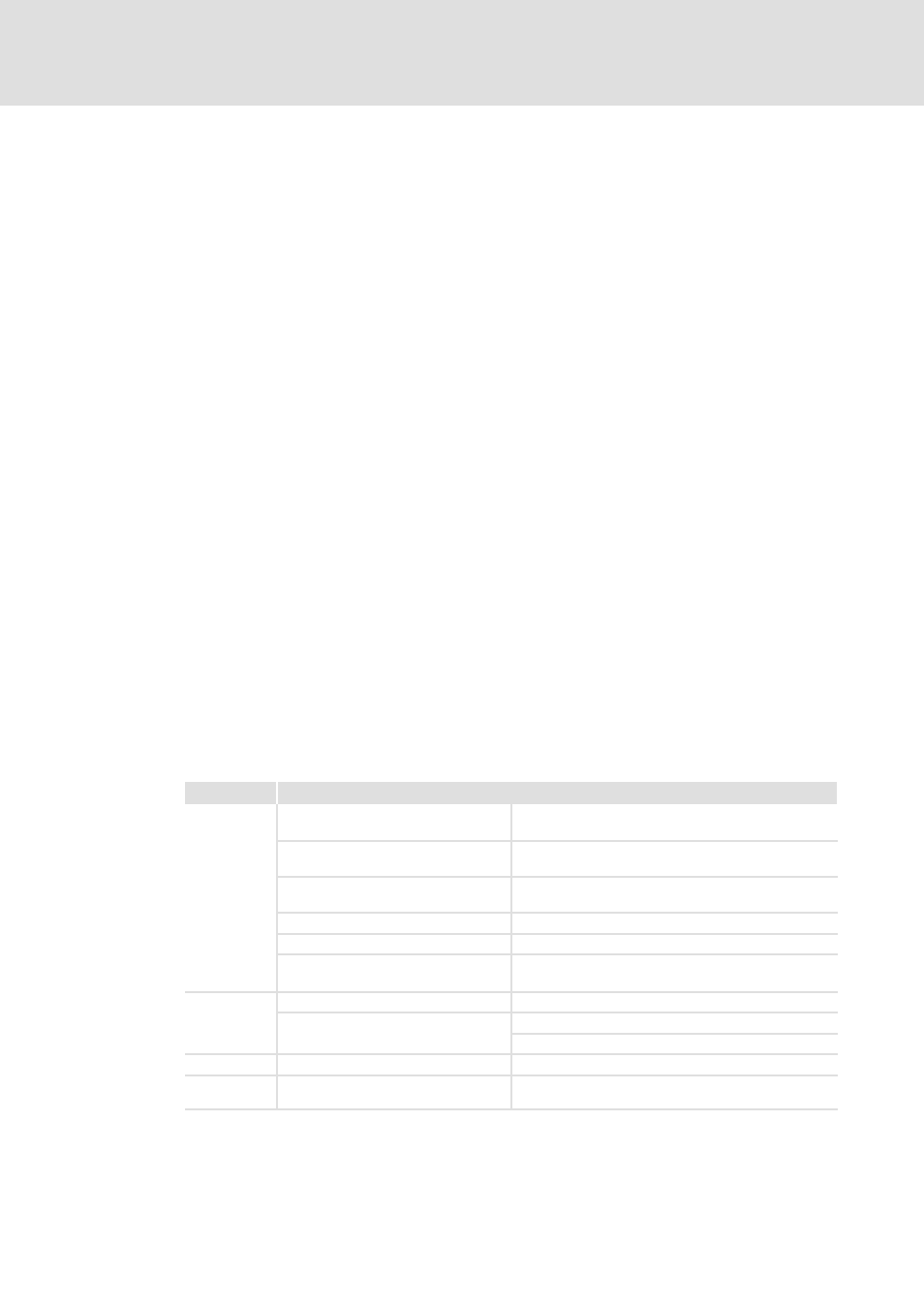
Technical data
TopLine C control terminals
Multi-encoder connection
4
85
EDS84ASC552 EN 9.1
4.8.2
Multi-encoder connection
Encoders are connected at X8 (15-pole Sub-D socket).
In order to avoid interference injections, only use shielded motor and encoder cables when
using an encoder.
ƒ
Absolute and incremental encoders are supported:
– TTL encoders 5 V (incremental)
– SinCos encoders 1 V
ss
(incremental)
– SinCos absolute value encoders 1 V
ss
with Hiperface protocol
– SSI absolute value encoders with Stegmann protocol
ƒ
Improved detection of low speeds with TTL encoders by additional time measuring
technique.
ƒ
SinCos absolute value encoders are read out serially during initialisation (connection
of the supply voltage). Then the SinCos signals are evaluated.
ƒ
Open-circuit monitoring:
– In the case of SinCos encoders by comparison of the SinCos signals with the
sine-wave form (radius monitoring)
– In the case of TTL encoders by monitoring of the mean value and the amplitudes
– Not with SSI encoders
ƒ
The following is not supported:
– HTL encoders -
they are not connected via the multi-encoder input, but via the digital inputs of
the controller.
– Motors with an installed ENP and KTY -
for these motors, correct temperature evaluation and motor protection are not
possible with 8400.
Labelling
Feature
Rated value
X8/
General
Cable length (system cable is
recommended)
Max. 150 m
Encoder types
TTL
SinCos 1V
SS
Protocols
Hiperface
SSI
Number of increments
1 ... 16384
Input frequency
max. 500 kHz
Scanning speed/position
TTL: 4 kHz (250 s cycle)
SSI: max. 4 kHz (250 s cycle)
X8/4, 2
Supply voltage V
CC
/GND for encoder
5 ... 12 V
max . output/current
up to 45 °C: 3 W/600 mA
45 ... 55 °C: 1.6 W/320 mA
X8/12, 10
n. c.
-
X8/14, 7
+KTY, -KTY
Type K: TY 83-110, TY84
Freely defined characteristic