Nanodac – Carbolite nanodac User Manual
Page 96
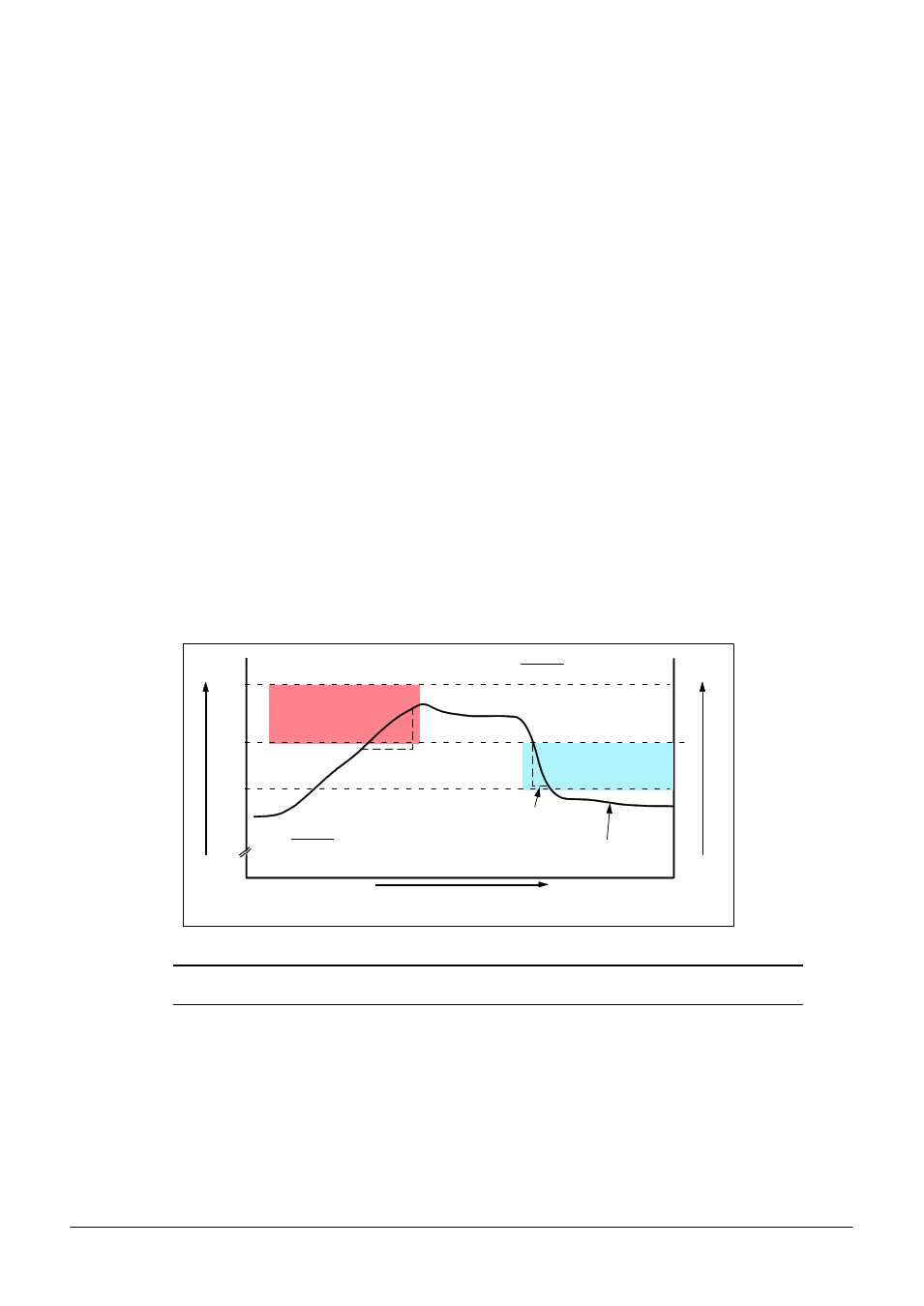
nanodac™
MC27 –EN– 1.04
94
AUTOTUNE (Cont.)
AT.R2G
Some load types and process conditions can cause autotune to set an incorrect value for R2G resulting in
an instability in the system after an autotune has completed, In such circumstances, the value of R2G
should be checked, and if it is low (approaching 0.1) a manual entry should be made as follows:
1.
In the Tune menu, set the AT.R2G parameter to ‘No’.
2.
In the PID menu, enter the new R2G value (calculated as described below)
3.
In the Tune menu, enter a value for Low Output, calculated from: Low Output = -High Output x R2G
4.
In the Tune menu, set ‘TuneEn’ On.
R2G CALCULATION
1.
In the Main menu, set the controller to Manual mode
2.
Turn heating on (limited by the value of ‘Output High’ in the
Output menu
) and measure the heating
rate (‘H’ °C/minute).
3.
Allow the process to heat to, say, 10% above the setpoint value then turn the heating off and allow
the temperature to settle.
4.
Turn cooling power on (limited by the value of ‘Output Low’ in the Output menu) and measure the
cooling rate (‘C’ °C/minute) whilst allowing the temperature to fall below the setpoint value.
5.
Calculate the value of R2G from the equation R2G = (H/C) x (Output Low/output High)
Example:
For a measured heating rate (H) of 10°C per min and a measured cooling rate (C) of 25° per minute and
with, Output High = 80% and Output Low = 40%, then R2G = (10/25) x (40/80) = 0.4 x 0.5 = 0.2.
Figure 6.4.5d R2G calculation
Note: This is not a very accurate method as it does not take natural cooling into account. Its main
advantage is that it is simple to achieve.
Heating on
Cooling on
Output Hi
ΔHTemp
Output Lo
ΔCTemp
PV
ΔCTemp = Cooling rate
ΔCTime
ΔCTemp = Heating rate
ΔCTime
ΔCTime
T
empe
ratu
re
O
P
P
ow
er
Time
ΔHTime