Nanodac – Carbolite nanodac User Manual
Page 92
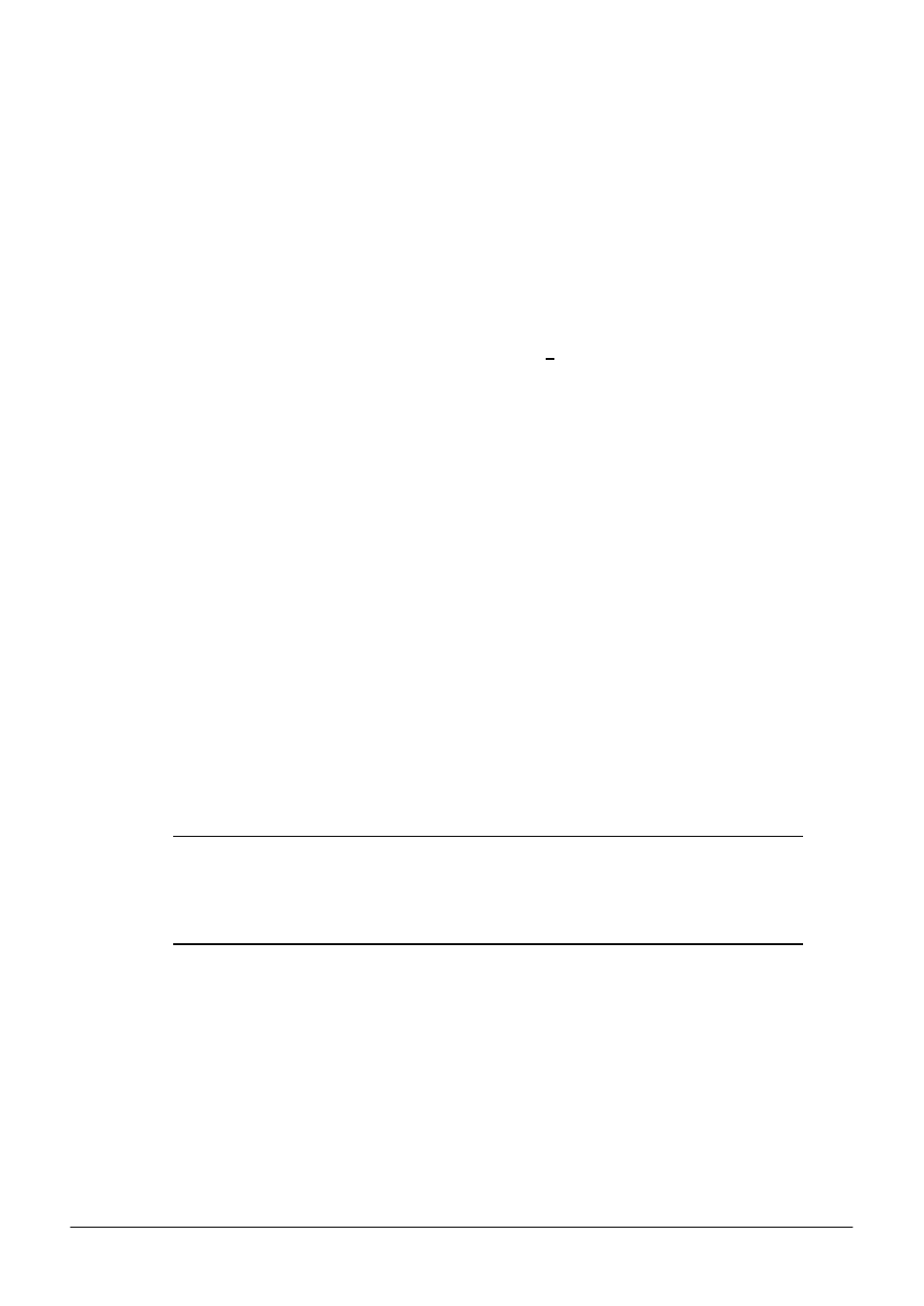
nanodac™
MC27 –EN– 1.04
90
AUTOTUNE (Cont.)
Autotune can be performed at any time, but normally it is performed only once, during the initial
commissioning of the process. However, if the process under control subsequently becomes
unsatisfactory (because its characteristics have changed), it may be necessary to tune again for the new
conditions.
The auto tune algorithm reacts in different ways depending on the initial conditions of the plant. The
explanations given later in this section are for the following example conditions:-
1.
Initial PV is below the setpoint and, therefore, approaches the setpoint from below for a heat/cool
control loop
2.
As above, but for a heat only control loop
3.
Initial PV is at the same value as the setpoint (tune at setpoint). That is, within 0.3% of the range of
the controller if ‘PB Units’ (Setup menu) is set to ‘Percent’, or +1 engineering unit (1 in 1000) if the ‘PB
Units’ is set to ‘Eng’. Range is defined as ‘Range High’ – ‘Range Low’ for process inputs or the
thermocouple or RTD range defined in section A3 for temperature inputs. If the PV is just outside the
range stated above the autotune will attempt a tune from above or below SP.
AUTOTUNE AND SENSOR BREAK
When the controller is autotuning and sensor break occurs, the autotune aborts and the controller outputs
the sensor break output power ‘Sbrk OP’ set up in the
Output menu
. Autotune must be re-started when
the sensor break condition is no longer present.
AUTOTUNE AND INHIBIT OR MANUAL
If the Loop Inhibit is asserted or the controller is put into Manual Mode, any tune in progress will be
aborted and will need to be restart once the condition has been removed. Note that it is not possible to
start an autotune sequence if the loop is inhibited or in Manual control.
AUTOTUNE AND GAIN SCHEDULING
When gain scheduling is enabled and an autotune is performed, the calculated PID values are written into
the PID set that is active, on completion of the tune. Therefore, the user may tune within the boundaries
of a set and the values will be written into the appropriate PID set. However, if the boundaries are close
(because the range of the loop is not large), then, at the completion of the tune, it cannot be guaranteed
that the PID values will be written to the correct set particularly if the schedule type is PV or OP. In this
situation the scheduler (‘Sched Type’) should be switched to ‘Set’ and the ‘active set’ chosen manually.
INITIAL CONDITIONS
Configure the parameters described in sections
B2.4.3
and
, above.
Notes:
1. The ‘tighter’ power limit applies. For example, if ‘High Output’ is set to 80% and ‘Output High’
is set to 70% then the output power will be limited to 70%
2. The PV must oscillate to some degree to allow the tuner to calculate the relevant values. The
limits must be set so as to allow oscillation about the setpoint.
INITIATING THE AUTOTUNE
In the Loop
Tune menu
for the relevant loop, set ‘TuneEn’ to ‘On’.