3 sensor hookup – Innovate Motorsports LogWorks 3 User Manual
Page 15
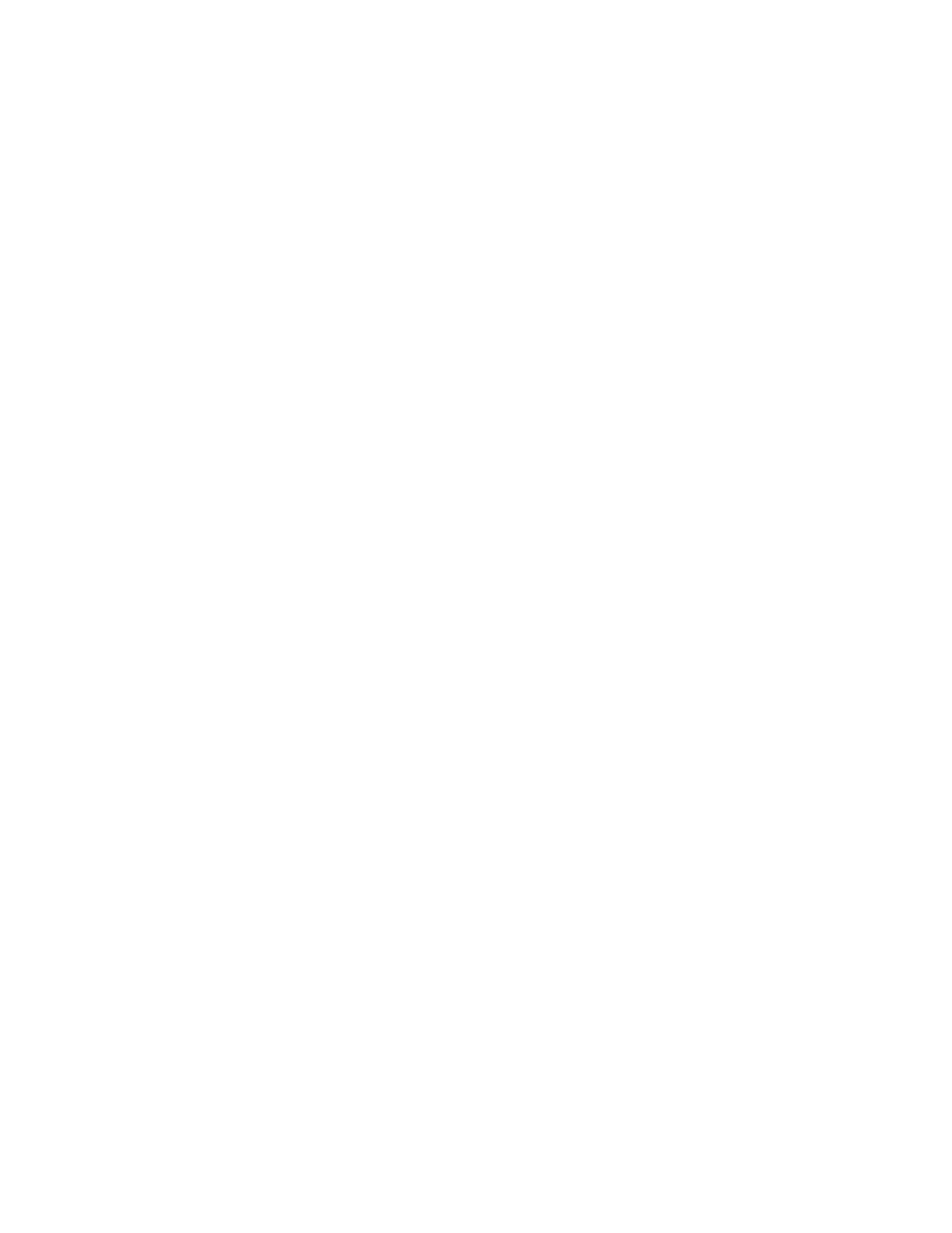
LogWorks3_Manual_1.01.doc
- 15 -
The MTS components convert the sensor data to a digital number between 0 and 1023 or a total
of 1024 steps incl. 0. This is equivalent of a 10 bit resolution (2
10
= 1024). The resulting
resolution for a 0..5V signal is therefore about 4.9 mV. Any signal variations smaller than that
cannot be resolved.
LogWorks has capabilities to convert the logged number back to the original quantity, provided
the characteristics of the original sensors are known. This means that LogWorks needs to know
how to convert the voltage output of the original sensor to the measured quantity equivalent.
The Air-Fuel-Ratio signal of the MTS components is not digitized from an external analog voltage.
Instead it is internally calculated. For logging purposes this signal is internally always stored as
Lambda with a resolution of 10 bits (1024 steps). To create the Air-Fuel-Ratio, the Lambda
value is multiplied with the stoichiometric ratio for the given fuel (like 14.7 for gasoline) by the
LogWorks software.
The data log range for Lambda is 0.5 to 1.523, equivalent to 1024 steps with a resolution of 0.001
Lambda (for gasoline this is equivalent to a 0.0147 AFR with a range of 7.4 to 22.4 AFR). This
range is more than sufficient for spark ignited internal combustion engines. AFR/Lambda ranges
outside of the logging range are pegged at the minimum or maximum point respectively.
See the manual for the MTS device you are using for details on how to connect various
sensors.
2.3 Sensor Hookup
Most sensors requires a ground connection. The voltage output of the sensor is referenced to that
ground. If the device measuring the sensor is connected to a different ground, the voltage
difference between the grounds can shift the sensor output voltage relative to the measuring
device. Some measuring devices, like the LMA-3, have differential inputs to compensate for that
offset. The negative side of a differential input is NOT a ground. It is intended to be connected to
the same ground as the sensor. A measuring device with a differential input measures the
difference between its own ground and the sensor’s ground on the negative input and subtracts
the difference from the measured voltage on the positive input to compensate for the ground
offsets. The hookup from a differential input requires two wires. One for the signal itself and one
for the ground reference. The ground reference input (typically named CHx-) goes to the
grounding point of the sensor.
Ground offsets are especially problematic for resistive and voltage output sensors. They are not
so important for frequency or duty cycle based sensors. For a measuring device with common
ground, like the LMA-2, it is best to ground all sensors at the same point where the measuring
device itself is grounded.
Ground offsets can also affect frequency or duty cycle based sensors. Typically when measuring
a frequency, the signal is measured as ‘high’ or ‘low’ depending on the measurement device’s
high-low threshold. In the LMA-2 or LMA-3 the threshold is 1V for the LMA-2 or 2.5V for the LMA-
3. Ground offsets of 1V or 2.5V will not allow the device to measure correctly.
Another problem can be ‘ground bounce’. If the signal generating device (for example an ignition
system) creates very high current pulses, it’s ground can momentarily ‘jump’ over the threshold of
the measuring device because of the high current. These ‘ground-bounce’ pulses are measured
as false frequencies and can interfere with the measurement.
Another problem in sensor hookup is called ‘induced noise’. In an engine compartment very high
current pulses are routed many different places. These current pulses can come from the