2 sensors and the modular tuning system – Innovate Motorsports LogWorks 3 User Manual
Page 14
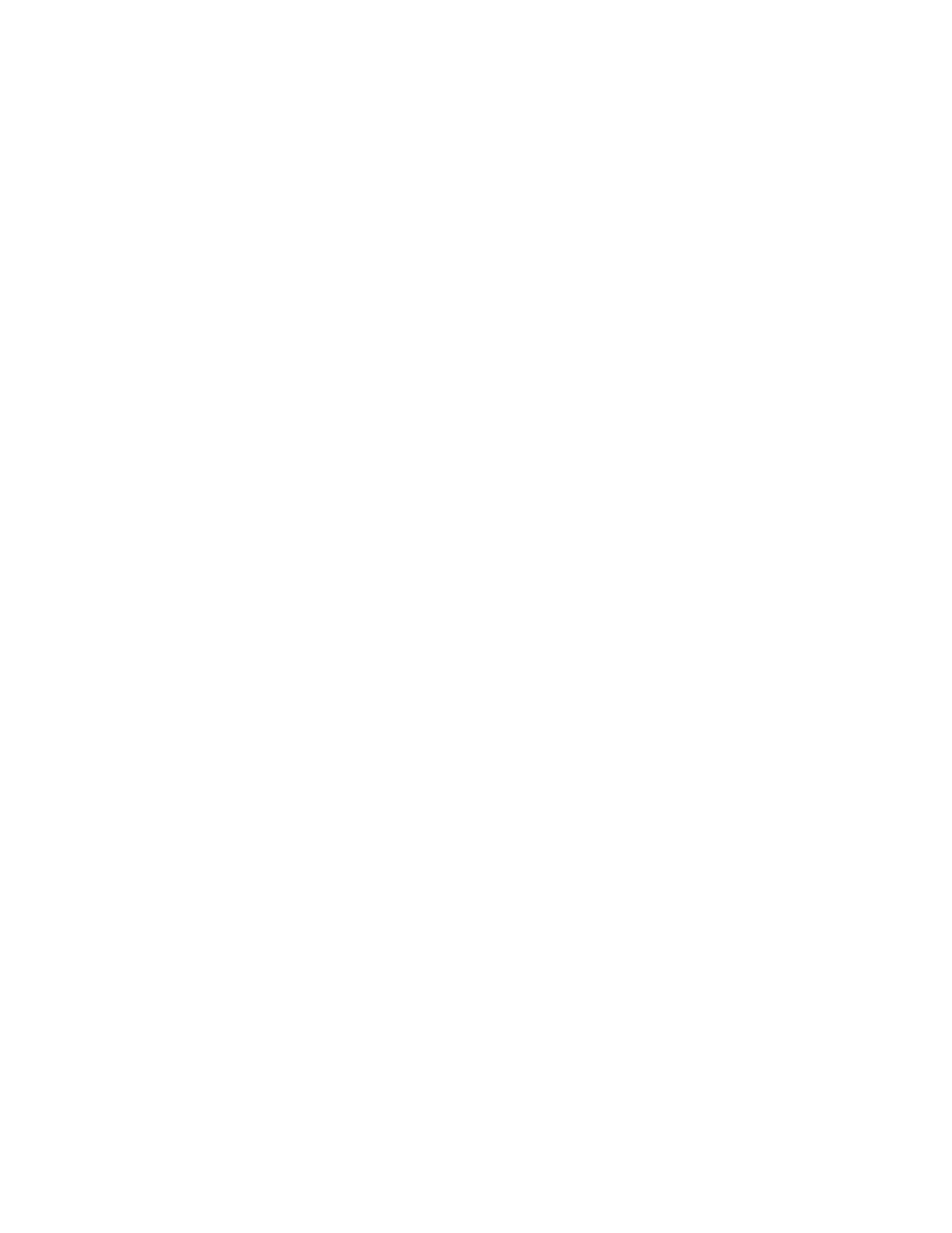
LogWorks3_Manual_1.01.doc
- 14 -
2.2 Sensors and the Modular Tuning System
The Innovate modular tuning system (MTS) consists of various devices to measure, digitize and
record various engine parameters. Typically these parameters are sensed by different sensors
built either into the engine itself or into MTS components. These sensors measure for example
temperatures, pressures, air-flow, air-fuel ratio and so on. Sensors convert the measured quantity
into an electrical signal, typically a voltage between 0 and 5V, which can be logged or displayed
by the MTS components. The sensors can be categorized generally into four different groups,
depending on the output they produce:
a. Voltage output sensors with external supply
These sensors have mostly 3 pins. One for the supply voltage (typically 5V), one for the
output signal, and one ground. Sometimes the ground pin is omitted and the sensor is
grounded through its metallic body to the engine. Typical examples are Throttle Position
sensors (TPS), Manifold Absolute Pressure sensors (MAP), and Mass Air Flow Sensors
(MAF). The output voltage has a typical range of 0..5V and varies for most sensors linearly
with the measured quantity.
b. Voltage generating sensors
These sensors generate a (small) voltage more or less proportional to the measured quantity.
Typical examples are Thermocouples and (Narrow-Band) O2 sensors. Thermocouples output
a very small voltage (in the microvolt range) that requires a special amplifier to make the
signal readable and loggable. The LMA-3 Auxbox has such an amplifier built in.
Narrow-Band O2 sensors output a voltage in the milliVolt range (up to 1000mV). Their
voltage output has a jump from low (~100mV) to high (700mV to 1000mV) when the AFR of
the exhaust gas changes from lean of stoichiometric to rich of stoichiometric. They act more
like switches than actual sensors. Basically they can indicate lean, rich and stoichiometric.
c. Resistive sensors
These sensors change their electrical resistance with the measured quantity. Very often the
relationship between resistance change and the measured parameter is non-linear. Typical
examples are Intake Air Temperature Sensors (IAT), coolant temperature sensors (CT) and
some oil-pressure/fuel pressure sensors. Typically these sensors have 2 pins. One is ground,
the other is connected to a load resistor. Often the ground pin is omitted and the sensor is
grounded through its body to the engine. The other end of the load resistor is connected to a
voltage supply (typically 5V). The purpose of the load resistor is to form a voltage divider with
the sensor. At the connection between load resistor and sensor a voltage is formed that is
dependent on the resistance change of the sensor according to this formula:
Vout = Vsupply * Rs / (Rs + RL)
Were Vout is the output voltage, Vsupply is the supply voltage, Rs is the sensor resistance
and RL is the load resistor. For maximum sensitivity, RL is typically chosen to be equal to Rs
at the typical operating point.
A sensor that falls between resistive sensors and voltage output sensors with external supply
is the throttle position sensor. Although it is a resistor with a movable tap, it behaves looks
and interfaces exactly like a voltage output sensors with external supply.
d. Frequency sensors
These sensors output a signal that varies in frequency (oscillating voltage) with the measured
quantity. Examples are some MAF sensors, the tach signal that measures engine RPMs and
the vehicle speed signal generated by drive-shaft or wheel sensors.
The LMA-3 (Auxbox) has the capability to convert these frequencies into a digital or analog
signal that can be interpreted and logged.