7 and finally, a weird one – Innovate Motorsports LogWorks 3 User Manual
Page 144
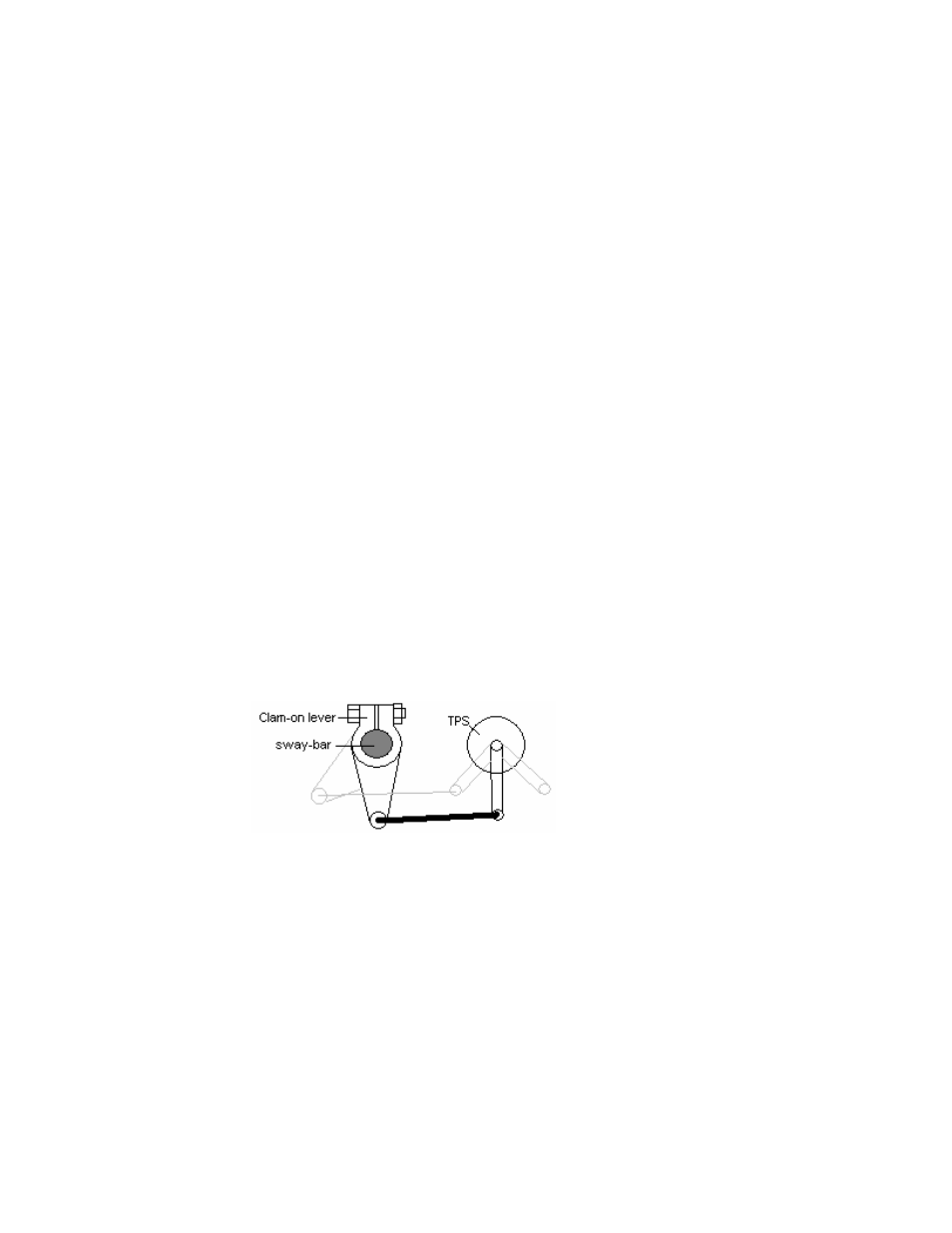
LogWorks3_Manual_1.01.doc
- 144 -
15.7 And finally, a weird one
Very often one can see small front-wheel-drive cars on the road with huge wings mounted on the
trunk lid. But there’s no corresponding aerodynamic down-force device in the front. Of course, in
the majority of cases the wing is there for the ‘cool factor’ because many race-cars have wings
(birds do too, but birds also have no penis).
In a race car the wing creates aerodynamic down-force. The down force allows increasing
cornering speed because more force is put vertically on the tires without increasing the mass of
the car (which would create more side force proportionally). The aerodynamic forces created by
wings and under-car aerodynamics can be very large. For example in a Formula 1 car at speed
the down-force is twice the car’s weight (car could drive upside down on the underside of a road
and would still stick with a force equal to its own weight).
In the above case one can only hope that these people never drive their car at speed. The down-
force of that wing, extending past the end of the car, will lift the front of the car up and make it
unstable and dangerous, especially in cross-wind situations.
But there is a legitimate need to measure down-force in a race car. Here’s how it can be done
with the MTS:
Any performance car has front- and rear sway-bars (also called anti-roll bar). These are typically
pieces of round spring steel (sometimes hollow tubes) that transfer the deflection force from the
outer wheel in a corner to the inner wheel. During that deflection the center of the sway-bar stays
pretty stationary because the bar is twisted. During normal suspension deflection on both wheels
on the axle the bar rotates with the suspension movement.
To measure down-force, one can use the car’s suspension springs a spring-scale. To do that,
fabricate a clamp-on lever that clamps to the center of the sway-bar. Use this lever to actuate a
throttle position sensor (TPS) as in the following drawing:
Dimension the relationship between the clamp-on lever and the TPS’s lever such that the TPS
goes through its movement range of about 90 degrees for the full suspension travel.
Then hook up the TPS sensor to 5V and measure its output voltage. Load the car up with 25 lb or
50lb sand-bags (over the axle) and record the sensor voltage for each load to calibrate your
‘spring scale’ for each axle.
Enter that table as custom lookup table in LogWorks (voltage vs. load).
Hook the TPS sensor to the LMA-2 or LMA-3 with the following circuit: