4 control parameters – NORD Drivesystems BU0700 User Manual
Page 73
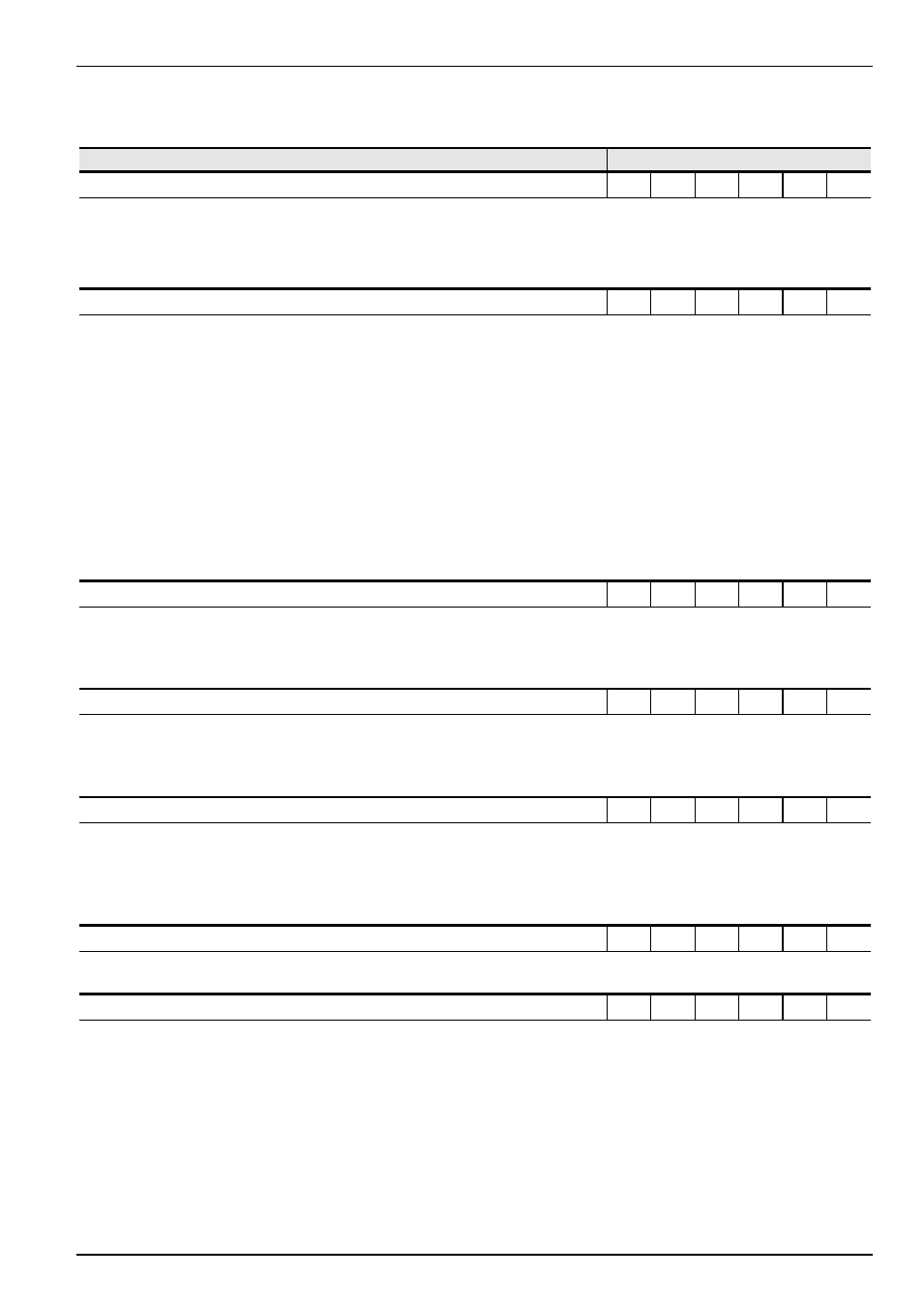
5.1.3 Motor data
BU 0700 GB-1411
Subject to technical alterations
73
5.1.4 Control parameters
Parameter
Setting value / Description / Note
Available with option
P300 (P)
Servo mode
ENC POS
0...1
[ 0 ]
Activates the speed control with speed measurement via the incremental encoder with the special
extension units PosiCon or Encoder (SK XU1-ENC, ...-POS).
Note:
For correct function, the encoder must be connected to the special extension unit (see
Encoder connection, Chap. 3.3 or 3.5) and the increment number entered in parameter
P301.
P301
Incremental encoder
ENC POS
0...17
[ 6 ]
Input of the pulse-count per rotation of the connected encoder.
If the encoder rotation direction is not the same as the FI, (depending on installation and wiring), it can
be compensated for by selecting the corresponding negative increment numbers 8....15.
0 = 500 pulses
1 = 512 pulses
2 = 1000 pulses
3 = 1024 pulses
4 = 2000 pulses
5 = 2048 pulses
6 = 4096 pulses
7 = 5000 pulses
8 = - 500 pulses
9 = - 512 pulses
10 = - 1000 pulses
11 = - 1024 pulses
12 = - 2000 pulses
13 = - 2048 pulses
14 = - 4096 pulses
15 = - 5000 pulses
16 = - 8192 pulses
17 = + 8192 pulses
P310 (P)
Speed controller P
ENC POS
0...3200 %
[ 100 ]
P-component of the encoder (proportional amplification).
Amplification factor, with which the speed difference is multiplied from the setpoint and actual
frequency. A value of 100% means that a speed difference of 10% produces a setpoint of 10%. Values
that are too high can cause the output speed to oscillate.
P311 (P)
Speed controller I
ENC POS
0...800 % / ms
[ 20 ]
I-component of the encoder (Integration component).
The integration component of the controller completely eliminates any control deviation. The value
indicates how large the setpoint change is per ms. Values that are too small cause the controller to
slow down (reset time is too long).
P312 (P)
Torque current controller P
ENC POS
0...800 %
[ 200 ]
Current controller for the torque current. The higher the current controller parameters are set, the more
precisely the current setpoint is maintained. Excessively high values in P312 generally lead to high-
frequency vibrations at low speeds, on the other hand, excessively high values in P313 generally
produce low frequency vibrations across the whole speed range. If the value "Zero" is entered in P312
and P313, then the torque current control is switched off. In this case, only the motor model precontrol
is used.
P313 (P)
Torque current controller I
ENC POS
0...800 % / ms
[ 125 ]
I-component of the torque current controller. (See also P312 >Torque current controller P<)
P314 (P)
Torque current controller limit
ENC POS
0...400 V
[ 400 ]
Determines the maximum voltage increase of the torque current controller. The higher the value, the
greater the maximum effect that can be exercised by the torque current controller. Excessive values in
P314 can specifically lead to instability during transition to the field weakening zone (see P320). The
values for P314 and P317 should always be set roughly the same, so that the field and torque current
controllers are balanced.