IAI America ERC User Manual
Page 137
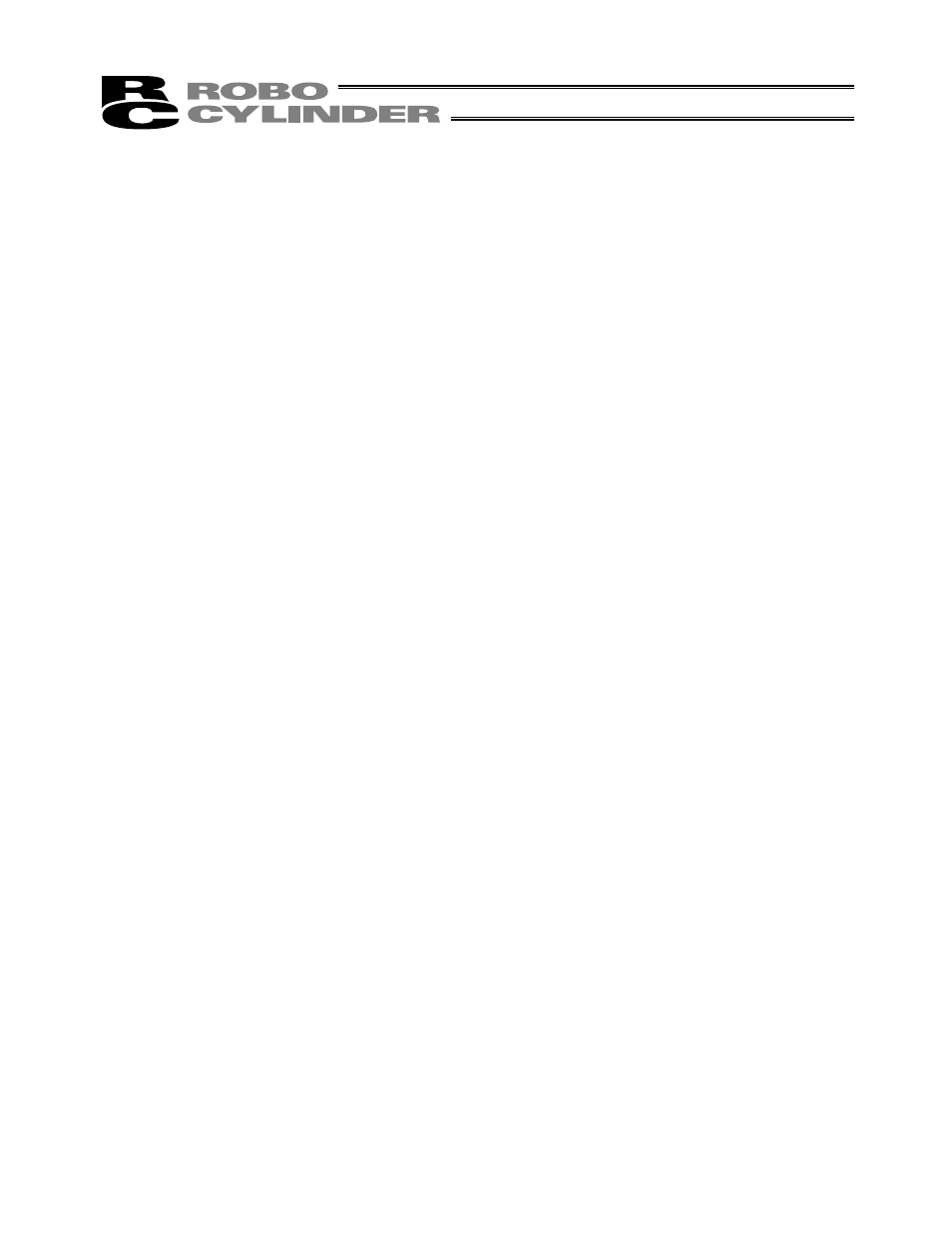
117
Vibration occurs when the actuator is stopped.
Cause: The slider is receiving an external force.
Action: If the external force cannot be removed, increase the value set in user parameter No. 12 (Current-
limiting value at standstill during positioning).
Increasing this value will cause the holding torque at standstill to increase, so do not increase the
parameter setting above 70%.
The actuator overshoots when decelerated to a stop.
Cause: High load inertia is generated due to the combination of load capacity and deceleration.
Action: Decrease the acceleration/deceleration setting.
The home and target positions sometimes shift on the rod-type actuator.
Cause: The current-limiting value is lower than what is required in view of the load capacity and slide
resistance.
Action: The actuator may have to be replaced in some cases. Please contact IAI.
The speed is slow during push & hold operation.
Cause: The set current-limiting value is low with respect to the load and slide resistance.
Action: Increase the current-limiting value for push & hold operation.
The actuator operates abnormally when the servo is turned on following the power on.
Cause: The excited phase is not detected correctly when the servo is turned on because of one of the
following conditions at the time of power on:
[1] The slider or rod is contacting the mechanical end.
[2] An excessive external force is exerted to the work.
Action: [1] Check if the slider or rod is contacting the mechanical end. If it is, move the slider/rod away from
the mechanical end. If the actuator is equipped with a brake, move the slider/rod after releasing
the brake by turning on the brake release switch. At this time, pay attention to prevent the work
from falling due to its dead weight and protect your hand, robot, and the work from
injuries/damages.
[2] Check if the work is in contact with an object in the surroundings. If so, move the work away
from the obstruction to provide a minimum clearance of 1 mm.
If neither of causes [1] and [2] is present, please contact IAI.