6 install the motor, 7 general wiring practices – Rockwell Automation FlexPak 3000 Power Module Version 4.2 User Manual
Page 33
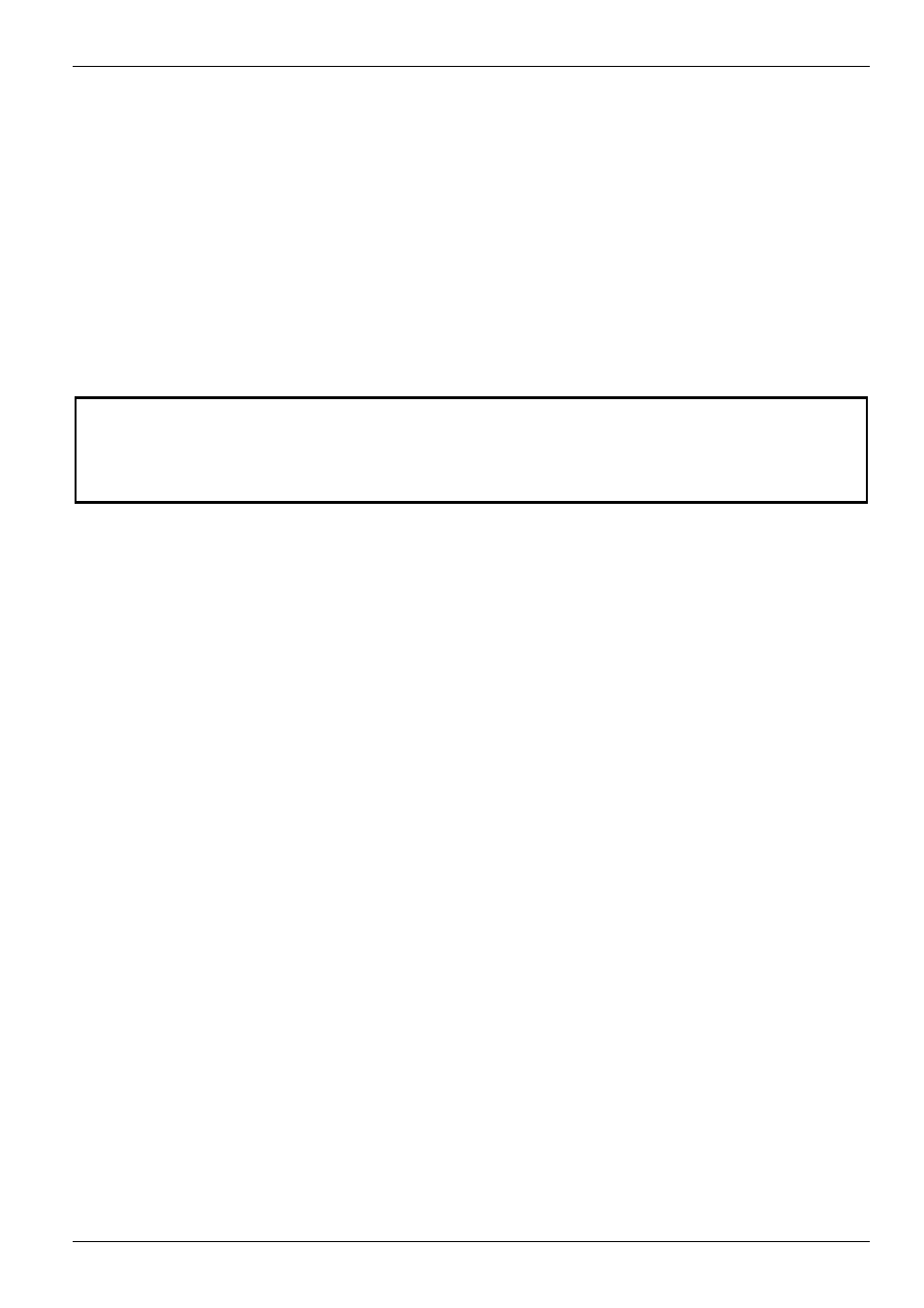
INSTALLATION AND WIRING
49’1340 e
FlexPak 3000
3-9
3.6
Install the Motor
1. Verify that the motor is the appropriate rating to use with the drive.
2. Install the DC motor in accordance with its installation instructions.
3. Make sure that coupled applications have proper shaft alignment with the driven machine or
that belted applications have proper sheave/belt alignment to minimize unnecessary motor
loading.
4. If the motor is accessible while it is running, install a protective guard around all exposed
rotating parts.
5. Wire the motor to the drive. Refer to "Wire the DC-Motor to the Drive".
3.7
General Wiring Practices
DANGER
The user is responsible for conforming to all applicable standards. Wiring, grounding, disconnects and
overcurrent protection are of particular importance.
Size and install all wiring in conformance with all other applicable standards.
Failure to observe this precaution could result in severe bodily injury or loss of life.
The Drive is designed for AC entry and DC power exiting at the top and control and signal
wiring entering from the bottom.
Reference signal wiring should be run in a separate conduit isolated from all AC and DC power
and control. Signal wires should not be run in parallel with high voltage or electrically noisy
conductors. Always cross such conductors at 90
°
.
All reference signals should be wired with either twisted double or twisted triple conductor wire,
40 twists per meter, stranded copper, 1.5 mm
2
, or screened 4-stranded (3, PE) 0.5 mm
2
(PN
380.35.01), 600 VAC rated insulation, with a temperature range of 40 - 105
°
C.
Analog tachometer feedback should be run in a separate conduit isolated from all AC and DC
power and logic control. Wiring should be the same as for the reference signals but screened
per pair if stranded cable 0.5 mm
2
(PN 380.33.00) is used.
Digital tachometer feedback (Encoder) wiring should be twisted per pair, not screened and be
run in a separate conduit isolated from all AC and DC power and logic control.
For mounting with external contacts and solenoids, coils should be suppressed
to reduce noise.
NOTE: The maximum recommended wire length from the drive to the motor is 300 meter.