Verify operation – Rockwell Automation 25B PowerFlex 520-Series Adjustable Frequency AC Drive User Manual User Manual
Page 228
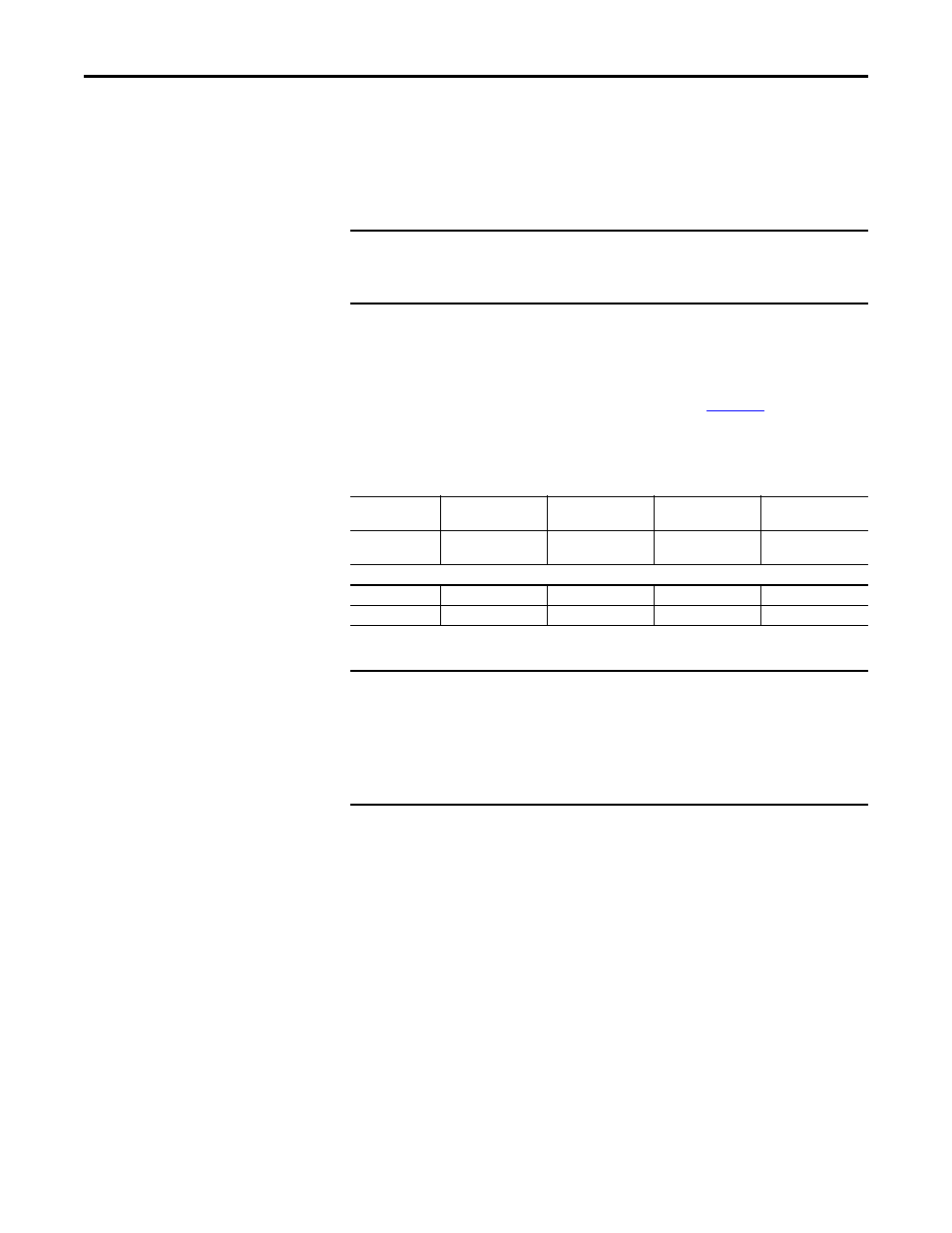
228
Rockwell Automation Publication 520-UM001G-EN-E - September 2014
Appendix G
Safe-Torque-Off Function
Under normal drive operation, both safety inputs (Safety 1 and Safety 2) are
energized, and the drive is able to run. If either input is de-energized, the gate
control circuit becomes disabled. To meet EN ISO 13849 operation, both safety
channels must be de-energized. Refer to the following examples for more
information.
Verify Operation
Test the safety function for proper operation after the initial setup of the
PowerFlex 525 Safe-Torque-Off function. Retest the safety function at the
intervals determined by the safety analysis described on
.
Verify that both safety channels are functioning according to the table below.
IMPORTANT
By itself, the Safe-Torque-Off function initiates a coast to stop action.
Additional protective measures will need to be applied when an application
requires a change to the stop action.
Channel Operation and Verification
Safety Function
Status
Drive In
Safe State
Drive In
Safe State
Drive In
Safe State
Drive
Able To Run
Drive Status
Configured by t105
[Safety Open En]
Fault F111
(Safety Hardware)
Fault F111
(Safety Hardware)
Ready/Run
Safety Channel Operation
Safety Input S1
No Power Applied
Power Applied
No Power Applied
Power Applied
Safety Input S2
No Power Applied
No Power Applied
Power Applied
Power Applied
IMPORTANT
If an external fault is present on the wiring or circuitry controlling the Safety 1
or Safety 2 inputs for a period of time, the Safe-Torque-Off function may not
detect this condition. When the external fault condition is removed the Safe-
Torque-Off function will allow an enable condition. Fault in the external wiring
shall either be detected by external logic, or excluded (wiring must be
protected by cable ducting or armoring), according to EN ISO 13849-2.