Positioning overview, Common guidelines for all applications – Rockwell Automation 25B PowerFlex 520-Series Adjustable Frequency AC Drive User Manual User Manual
Page 205
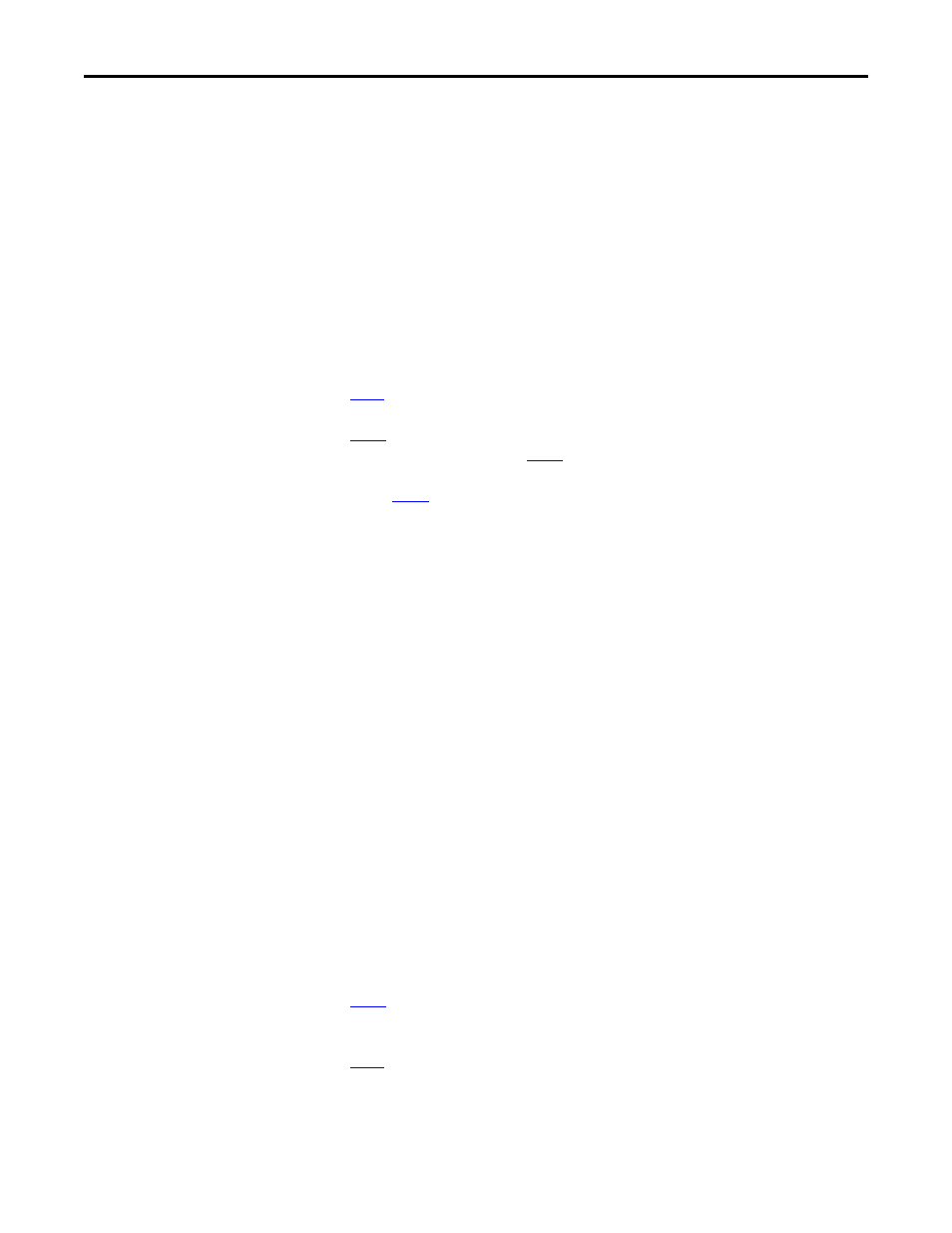
Rockwell Automation Publication 520-UM001G-EN-E - September 2014
205
Encoder/Pulse Train Usage and Position StepLogic Application
Appendix E
Positioning Overview
The PowerFlex 525 drive includes a simple position regulator which can be used
in a variety of position applications without the need for multiple limit switches
or photo-eyes. This can be used as a stand-alone controller for simple
applications (up to 8 positions) or in conjunction with a controller for more
flexibility.
Please note that this is not intended to replace high end servo controllers or any
application that needs high bandwidth or very high torque at low speeds.
Common Guidelines for All
Applications
The position regulator can be configured for operation appropriate for a variety
of applications. Certain parameters will need to be adjusted in all cases.
[Speed Reference1] must be set to 16 “Positioning”.
[Motor Fdbk Type] must be set to the match the feedback device.
Positioning mode must use
[Motor Fdbk Type] option 4.
[Motor Fdbk Type] Options
0 “None”
indicates no encoder is used. This can not be used for
positioning.
1 “Pulse Train”
is a single channel input, no direction, speed feedback
only. This should not be used for positioning. The Single Channel
selection is similar to a Pulse Train, but uses the standard encoder scaling
parameters.
2 “Single Chan”
is a single channel input, no direction, speed feedback
only. This should not be used for positioning. Single channel uses the
standard encoder scaling parameters.
3 “Single Check”
is a single channel input with encoder signal loss
detection. The drive will fault if it detects that the input pulses do not
match the expected motor speed. This should not be used for positioning.
4 “Quadrature”
is a dual channel encoder input with direction and speed
from the encoder. This may be used for positioning control.
5 “Quad Check”
is a dual channel encoder with encoder signal loss
detection. The drive will fault if it detects that the encoder speed does not
match the expected motor speed.
[Reverse Disable] should be set to 0 “Rev Enabled” to allow bidirectional
movement necessary for position control.
[Torque Perf Mode] default setting is 1 “SVC”. However, any mode can be
used to improve the low speed torque for positioning applications. For best
results, tune the application first. The autotune routine can be completed to
further improve the drive-motor performance.